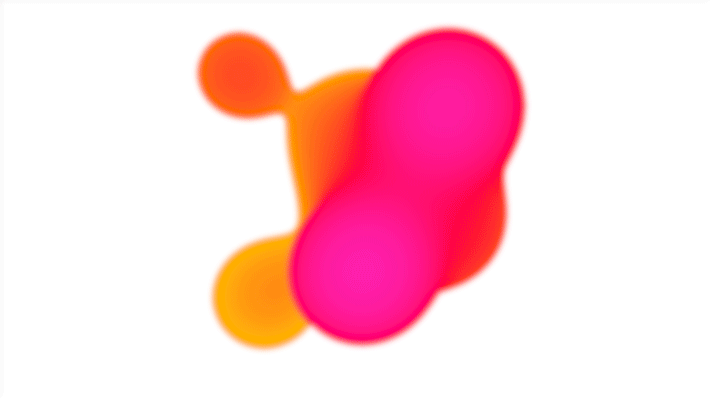
технологии разумдля созидания
«...не только гибко реагировать на любой запрос наших клиентов, но и предлагать инновационные решения...»
В рамках стратегии развития до 2025 года мы реализуем глобальную программу технологической модернизации, которая включает в себя внедрение современного оборудования, оптимизацию, автоматизацию и роботизацию процессов. Это обеспечивает рост объемов производства, расширение ассортимента продукции, сбережение ресурсов, повышение энергоэффективности и минимизацию влияния на окружающую среду.
Объем инвестиций с 2015 года
34 млрд руб.
Мы реализуем глобальную программу технологической модернизации, которая включает в себя внедрение современного оборудования, оптимизацию, автоматизацию и роботизацию процессов.
«Мы пересмотрели технологический подход к производству таким образом, чтобы не только гибко реагировать на любой запрос наших клиентов, но и предлагать инновационные решения, которые служат основой для нового этапа развития огнеупорных технологий».
Сергей Одегов генеральный директор Группы Магнезит
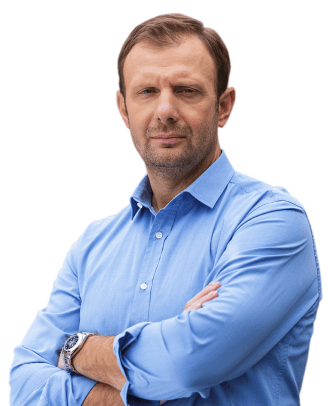
эффекты модернизации
имеют значение для Группы, страны, клиентов и партнеров, сотрудников и общества
для Группы
- технологическое лидерство
- внедрение современных стандартов экологичного производства
- оптимизация производственной инфраструктуры
- увеличение доли продукции с высокой добавочной стоимостью
- улучшение функциональных свойств продукции на основе магнезиального сырья
- увеличение доли на существующих рынках и выход на новые
для страны
- импортозамещение
- повышение экспортного потенциала отечественной экономики
- экономический рост
- стабильная социальная ситуация
- экологическая безопасность
для клиентов и партнеров
- гарантированное высокое и стабильное качество продукции
- независимость от колебаний рынков и мировой политической конъюнктуры
- развитие производства
для сотрудников и общества
- новые рабочие места
- повышение компетенции сотрудников
- улучшение условий труда и качества жизни
- улучшение экологической обстановки
проекты модернизации охватывают все фазы производственного цикла
М
модернизация
К
комплексы
П
продукты
Э
экология
П
процессы
1. добыча и обогащение
разработка месторождений
процесс
Магнезитовая руда добывается двумя способами: открытым (в карьере) и подземным (в шахте). В обоих подходах применяются буровзрывные работы. После взрыва породу доставляют на Комплекс дробления и обогащения.
проект модернизации
проект модернизации
дробление, обогащение, сортировка
проект модернизации
проект модернизации
процесс
В комплексе дробления и обогащения происходит отделение магнезита от других горных пород (обогащение) — дробление до необходимой фракции и сортировка по химическому составу.
экология
рациональное использование сырья
минимизация влияния на окружающую среду
2. производство материалов
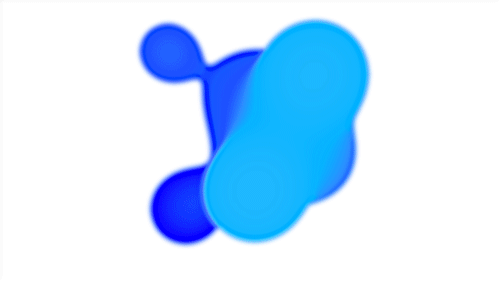
комплекс плотноспеченных порошков
Рекорд
проект модернизации
проект модернизации
экология
рациональное использование сырья
на окружающую среду
- планирование и контроль качественных параметров конечного продукта при обжиге в многоподовой печи
- сбор и возвращение в производство всей уловленной пыли
- конструкция многоподовых печей и технология обжига, позволяющие снизить эксплуатационные и ремонтные расходы почти в 3 раза
- более эффективное оборудование линии дробления, спроектированное для работы без простоев и ремонтов
- новая система логистики готового про-дукта, минимизирующая перемещение сырья по производственной площадке
на окружающую среду
- современные аспирационные установки и системы пылеподавления, установленные на каждой единице нового оборудования
- эффективность рукавных фильтров — 99,9%
- экологическая безопасность — 100%
декарбонизация
процесс
Первая стадия двухстадийного способа получения качественного спеченного периклаза. Происходит регулируемый обжиг сырого магнезита в многоподовой печи при температуре более 900 °С.
проект модернизации
помол
рассев
процесс
Рассев Слабообожженная магнезия проходит через несколько грохотов, где разделяется на фракции по размерам частиц.
ПомолСлабообожженная магнезия на мельницах измельчается до размера частиц менее
10 микрон.
После порошок будет спрессован в брикеты. Это необходимо, так как в шахтной печи можно обжигать только брикетированный продукт.
ПомолСлабообожженная магнезия на мельницах измельчается до размера частиц менее
10 микрон.
После порошок будет спрессован в брикеты. Это необходимо, так как в шахтной печи можно обжигать только брикетированный продукт.
брикетирование
процесс
Измельченный продукт брикетируется на специализированных прессах, предназначенных для получения из пылевидного продукта брикетов определенного размера и плотности.
обжиг
процесс
Брикеты слабообожженной магнезии подаются на обжиг в высокотемпературные шахтные печи, где под воздействием температуры более
1800 °С значительно увеличивается плотность исходного продукта и происходит перестройка его химической и физической структур.
1800 °С значительно увеличивается плотность исходного продукта и происходит перестройка его химической и физической структур.
дробление
проект модернизации
процесс
После обжига брикеты охлаждаются во вращающемся холодильном барабане до температуры не более
100 °С. Охлажденный материал поступает на дробление на разные фракции, нужные для конечного потребителя или для собственного дальнейшего производства огнеупоров.
100 °С. Охлажденный материал поступает на дробление на разные фракции, нужные для конечного потребителя или для собственного дальнейшего производства огнеупоров.
упаковка
рассев
процесс
Рассев Полученный периклазовый порошок просеивается через грохота на различные фракции, готовые для отгрузки клиенту или дальнейшего процесса собственного производства масс и изделий.УпаковкаСпеченный периклаз загружается навалом в автотранспорт или в бигбеги для отправки клиентам.
продукт
- спеченный периклаз, в том числе периклаз линейки Русский Магнезит
- каустическая магнезия
продукт
- слабообожженная магнезия, в том числе слабообожженная магнезия из сибирского сырья для произ-водства линейки Русский Магнезит
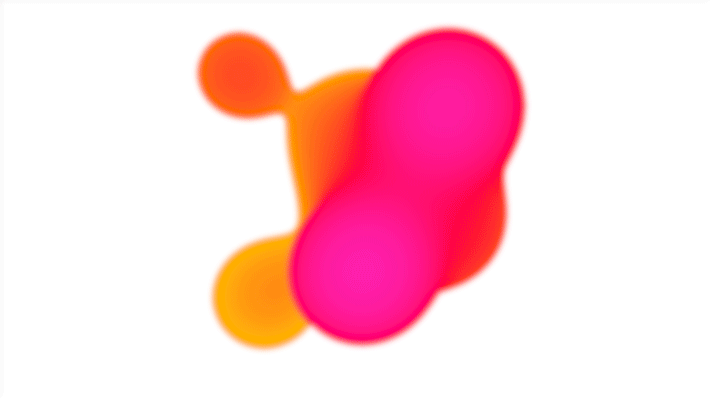
комплекс плавленых порошков
Авангард
проект модернизации
экология
рациональное использование сырья
- на 15% больше периклаза с каждого блока благодаря оптической сортировке
- сбор и возвращение в производство всей уловленной пыли, корки и осыпи
- сбережение ресурсов электродов
- увеличение производительности печей
- снижение удельных расходов электроэнергии
- использование отходящего тепла для обогрева производственных зданий
- сбор и очистка всех осадков в специальной системе
- оборотные циклы воды
- 26 аспирационных установок
- складирование всех сыпучих материалов в закрытых помещениях с системами пылеподавления и аспирации
плавка
проект модернизации
продукт
- слабообожженная магнезия из сибирского сырья для производства линейки Русский Магнезит
процесс
Плавленый периклаз получают путем плавки магнезиального сырья при температуре более 2800 °С.
Плавка происходит в руднотермических печах. В специальные печные ванны постепенно загружается сырье и опускаются электроды, на которые подается высокое напряжение. Между электродами образуется дуга. Излучение дуги плавит сырье вокруг нее. Процесс плавки занимает
11-12 часов, остывание наплавленного блока — до недели.
Плавка происходит в руднотермических печах. В специальные печные ванны постепенно загружается сырье и опускаются электроды, на которые подается высокое напряжение. Между электродами образуется дуга. Излучение дуги плавит сырье вокруг нее. Процесс плавки занимает
11-12 часов, остывание наплавленного блока — до недели.
дробление
проект модернизации
строительство Комплекса плавленых порошков Авангардсостав этапа проекта
- участок разделки блоков
- гидромолот
- системы пылеподавления и система аспирации
- на участке крупного дробления может находиться до 20 блоков одновременно
- современная система пыле-подавления и аспирации предотвращает перенос пыли по помещению
процесс
Полностью остывший наплавленный блок разбивается гидромолотом на фракцию
0-300 мм и сортируется на периклаз и корку, смешанную с периклазом.
0-300 мм и сортируется на периклаз и корку, смешанную с периклазом.
сортировка
проект модернизации
строительство Комплекса плавленых порошков Авангардсостав этапа проекта
- 3 оптических сепаратора
- 2 линии дробления
- технология оптической сепарации позволяет отделять самые мелкие фракции корки от периклаза
- оптическая сепарация обеспечивают общий прирост выхода плавленого периклаза 340 т/месяц, что сопоставимо с ежемесячной производительностью одной печи
процесс
Периклаз проходит несколько этапов дробления до мелких фракций и рассева. С помощью технологии оптической сортировки корка отделяется от чистого периклазового порошка. Корка отправляется на переплавку, а периклаз сортируется по фракциям, готовым для производства изделий и масс.
упаковка
проект модернизации
строительство Комплекса плавленых порошков Авангардсостав этапа проекта
- 1 линия сортировки
- 6 бункеров для отгрузки периклазового порошка
- полностью герметичные бункеры и системы вакуумной подачи порошка в закрытый автотранспорт
процесс
Периклазовый порошок проходит взвешивание и упаковку для дальнейшего перемещения по производственной площадке или для отгрузки клиентам.
продукт
- плавленый периклаз линейки Русский Магнезит
продукт
- плавленый периклаз линейки Русский Магнезит
Периклазом высокого качества считается периклаз с высокой плотностью, большим размером кристаллов и высокой чистотой содержания MgO — более
97%
Крупные стабильные кристаллы периклаза образуются благодаря равномерному охлаждению наплавленного блока, а высокая чистота достигается за счет двух-стадийной технологии темпера-турной обработки оксида магния.
комплекс плавленых порошков
проект модернизации
проект модернизации
плавка
продукт
- слабообожженная магнезия, в том числе слабообожженная магнезия из сибирского сырья
проект модернизации
процесс
Плавленый периклаз получают путем плавки магнезиального сырья при температуре более 2800 °С.
Плавка происходит в руднотермических печах. В специальные печные ванны постепенно загружается сырье и опускаются электроды, на которые подается высокое напряжение. Между электродами образуется дуга. Излучение дуги плавит сырье вокруг нее. Процесс плавки занимает
11-12 часов, остывание наплавленного блока — до недели.
Плавка происходит в руднотермических печах. В специальные печные ванны постепенно загружается сырье и опускаются электроды, на которые подается высокое напряжение. Между электродами образуется дуга. Излучение дуги плавит сырье вокруг нее. Процесс плавки занимает
11-12 часов, остывание наплавленного блока — до недели.
дробление
процесс
Полностью остывший наплавленный блок разбивается гидромолотом на фракцию
0-300 мм и сортируется на периклаз и корку, смешанную с периклазом.
0-300 мм и сортируется на периклаз и корку, смешанную с периклазом.
сортировка
проект модернизации
процесс
Периклаз проходит несколько этапов дробления до мелких фракций и рассева. С помощью технологии оптической сортировки корка отделяется от чистого периклазового порошка. Корка отправляется на переплавку, а периклаз сортируется по фракциям, готовым для производства изделий и масс.
упаковка
процесс
Периклазовый порошок проходит взвешивание и упаковку для дальнейшего перемещения по производственной площадке или для отгрузки клиентам.
продукт
- Плавленый периклаз с содержанием MgO до 97%
3. производство изделий
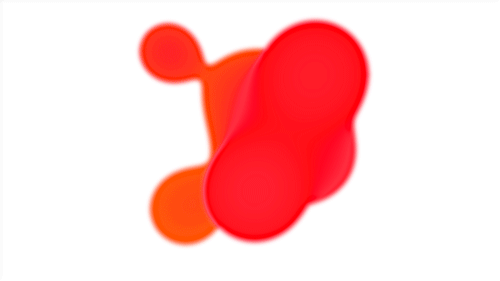
комплекс обжиговых изделий
Импульс
проект модернизации
экология
рациональное использование сырья
на окружающую среду
- минимизация брака благодаря автоматической оценке качества изделий
- максимально эффективное использование тепла внутри печи благодаря системе тепловых контуров
- максимальное снижение теплопотерь благодаря футеровке печи и теплоизоляции кожуха, а также конструкции вагонов
- на 40% ниже
материалоемкость и на
50% выше
энергоэффективность
на окружающую среду
- предотвращение выхода нагретых газов из активной зоны печи шлюзами
- возвращение отходящих газов в контур теплообменников
- оснащение каждого воздуховода печи датчиками выбросов
смешение
проект модернизации
строительство технологи-ческой линии производства изделий для цементной промышленностисостав этапа работ
- автоматизированный участок смешения
- смеситель производительностью
3,5 т/замес - система автоматизированного смешения и загрузки сырья
процесс
Компоненты строго дозируются и тщательно смешиваются в автоматическом режиме. Шихтовка (рецептура) изделий проектируется индивидуально с учетом требований заказчика. Оператор контролирует работу оборудования.
прессование
проект модернизации
строительство технологи-ческой линии производства изделий для цементной промышленностисостав этапа работ
- 2 гидравлических пресса
- робототехнические комплексы
- 2 пресса пятого поколения, оборудованные робототехни-ческими комплексами (РТК) для садки сырца непосредственно на печные вагоны, что исключает излишние перемещения изделий
- оснащение новых РТК вакуумными установками вместо захватов, что снижает количество микроповреж-дений изделий
- новая схема садки сырца на вагон: рабочая сторона огнеупоров обращена вверх, а сторона примыкания не контактирует с другими огнеупорами при обжиге
процесс
После смешения масса необходимого состава поступает в прессформу, под воздействием давления пресса занимает соответствующий объем и принимает заданную форму. При этом многократно увеличивается плотность готового изделия.
обжиг
проект модернизации
процесс
После прессования изделия проходят стадию сушки при температуре
300 °С.
После сушки следует обжиг в туннельных печах при температуре
1700 °C
и выше. В процессе обжига происходят спекание связки, физические и химические реакции, результатом которых становятся высокая плотность изделий и другие важные для конечного применения характеристики.
300 °С.
После сушки следует обжиг в туннельных печах при температуре
1700 °C
и выше. В процессе обжига происходят спекание связки, физические и химические реакции, результатом которых становятся высокая плотность изделий и другие важные для конечного применения характеристики.
сортировка и упаковка
проект модернизации
процесс
Каждое изделие, вышедшее из печи, проходит контроль на внешние и внутренние дефекты. Затем происходят маркировка изделий, наклейка термокомпенсационных прокладок (сгораемого в процессе эксплуатации картона), укладка на паллеты, упаковка и маркировка паллет.
продукт
- RMAG — линейка современных огнеупорных изделий магне-зиально-шпинельного состава для вращающихся печей цементного производства. Широкий выбор характеристик для различных условий эксплуатации, в том числе для печей на альтернативном топливе. Производится на новой технологической линии.
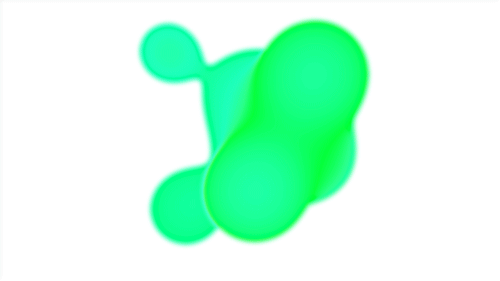
комплекс безобжиговых изделий
Прогресс
проект модернизации
экология
рациональное использование сырья
на окружающую среду
- предотвращение нецелесообразного использования сырья благодаря автоматической системе шихтовки
- исключение брака благодаря автоматизированной системе термообработки и конструкции печи
- сокращение потребления газа в печах почти в
2 раза - увеличение производительности новых печей более чем в
3 раза по сравнению с остальными печами Комплекса - максимальное использование тепла внутри печи благодаря
3 контурам теплообменника - максимальное снижение теплопотерь благодаря футеровке печи и теплоизоляции кожуха
на окружающую среду
- полное сжигание всех продуктов пиро-лиза исходящего из печи газа благодаря системе термического дожигания
смешение
проект модернизации
реконструкция и модернизация участка подготовки массы
- Саткинская производственная площадка
- сроки реализации: 2016–2017
- производительность:
8000 т/месяц
- 3 смесителя
- 20 бункеров
- автоматизированный процесс смешения, исключающий человеческий фактор
- смесители увеличенного объема, максимальный вес замеса 3,6 т
процесс
Компоненты строго дозируются и тщательно смешиваются в автоматическом режиме. Шихтовка (рецептура) изделий проектируется индивидуально с учетом требований заказчика. Оператор контролирует работу оборудования.
прессование
проект модернизации
строительство технологи-ческой линии производства изделий для черной металлургиисостав этапа проекта
- 5 гидравлических прессов
- робототехнические комплексы
- автоматизированный процесс прессования, контролируется оператором-прессовщиком с мониторов
- каждый пресс оборудован робототехническим комплексом (РТК)
- РТК снимают прессованные изде-лия с пресс-формы, автоматически проверяют на допустимые откло-нения, маркируют изделия и загру-жают на этажерки для перемеще-ния к термопечи
процесс
После смешения масса необходимого состава поступает в прессформу, под воздействием давления пресса занимает соответствующий объем и принимает заданную форму. При этом многократно увеличивается плотность готового изделия.
термообработка
проект модернизации
строительство технологи-ческой линии производства изделий для черной металлургиисостав этапа проекта
- 2 термопечи Сигма Прогресс 60
- длительность термообработки одного вагона с изделиями составляет
12 часов, длительность охлаждения —
3,5 часа - в термотуннеле может находиться 45 вагонов
- термообработка в печи произво-дится с помощью равномерного нагрева теплоносителя в прост-ранстве печи, что обеспечивает равномерную обработку каждого изделия
процесс
В термопечах происходит тепловая обработка формованных изделий для полимеризации связующего. Безобжиговые изделия проходят термообработку при температуре
200-260°C.
200-260°C.
сортировка
проект модернизации
строительство технологи-ческой линии производства изделий для черной металлургиисостав этапа проекта
- автоматизированный участок сортировки
- 5 линий смешения
- робототехнический комплекс
- паллеты с изделиями передвигает-ся автоматически
- все линии оборудованы автома-тизированными весами и сканерами
процесс
Готовые изделия проходят контроль на предмет дефектов и отклонений от заданных внешних и внутренних параметров. Прошедшие контроль изделия отправляются на сортировку по типоразмерам и составу, маркировку.
упаковка
проект модернизации
строительство технологи-ческой линии производства изделий для черной металлургиисостав этапа проекта
- автоматизированная линия упаковки паллет
- роботизированная выкладка изделий на паллеты
- автоматизированная упаковка паллет в стрейч-пленку
- уникальный QR-код каждой паллеты с информацией о продукции
процесс
Готовые изделия укладываются на паллеты таким образом, чтобы не повредить ни одно изделие при дальнейшей транспортировке.
продукт
- ПУ — группа изделий для черной металлургии. Производятся на новой технологической линии. Основной минеральный наполнитель — плавленый и/или спеченный периклаз, максимальное содержание MgO в котором до
98,5% - OXYDALCARTM — линейка современных огнеупорных изделий магнезиальноуглеродистого состава для футеровки кислородных конвертеров. Производятся на новой технологической линии с использованием новых типов экологически чистого связующего, что позволяет снизить нагрузку на окружающую среду при их произ-водстве и эксплуатации. Содержание MgO и С варьируется в зависимости от зоны применения конкретной марки