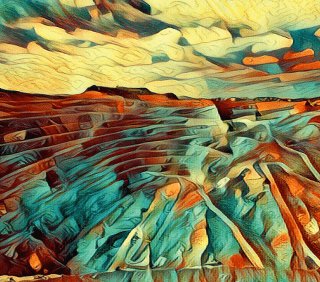

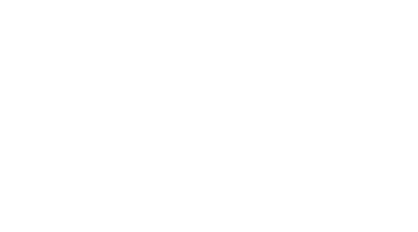
people × ideas × achievements
This project is an invitation to reflect upon creative collaboration in today’s context, when collaboration between human and artificial intelligence has become a reality. It features various genres, functions, forms of representation, and types of authorship. Innovative industrial facilities and the inventions behind them. Photos and digital graphics generated by a neural network along the themes of these photos.
gallery of innovations
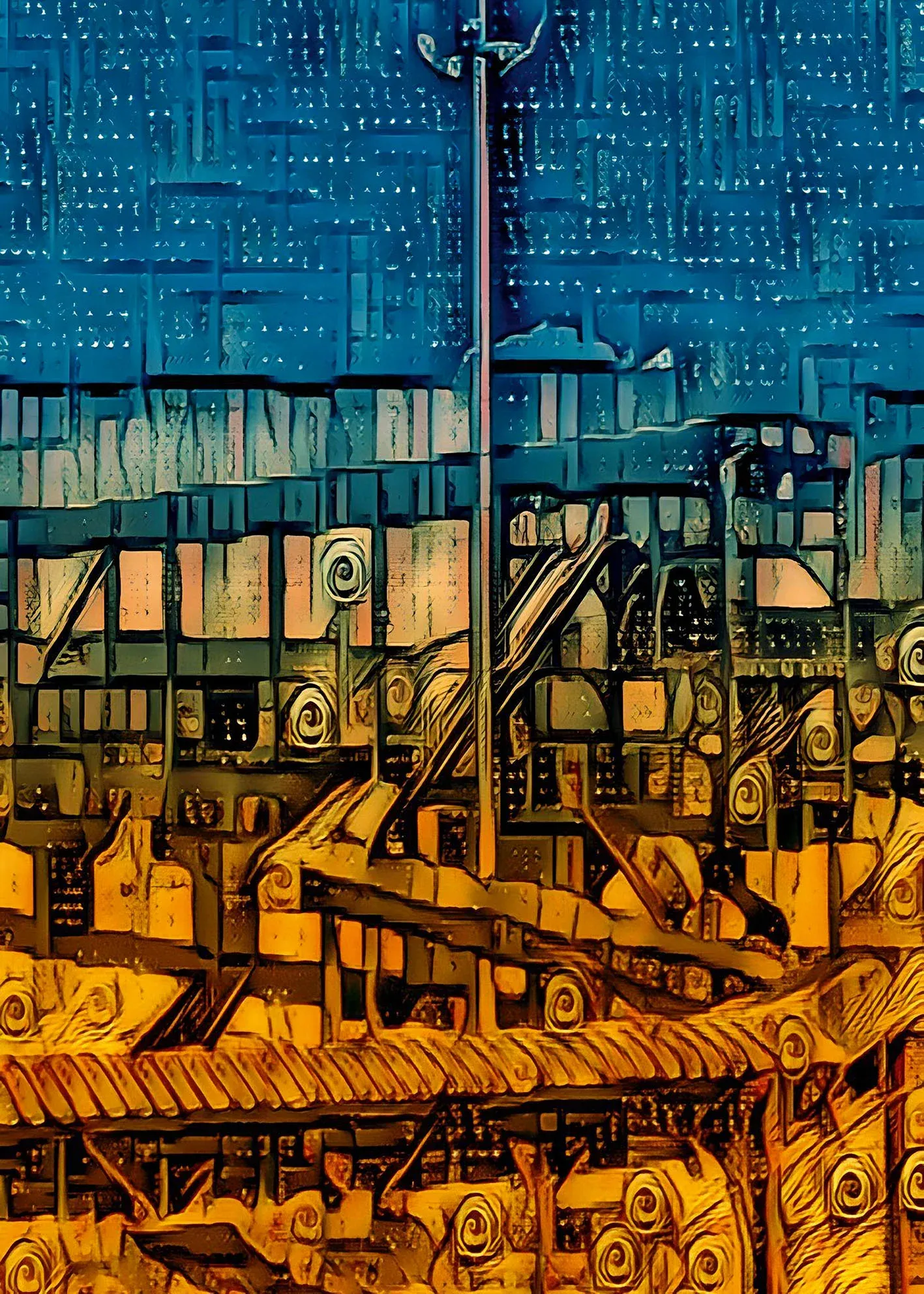
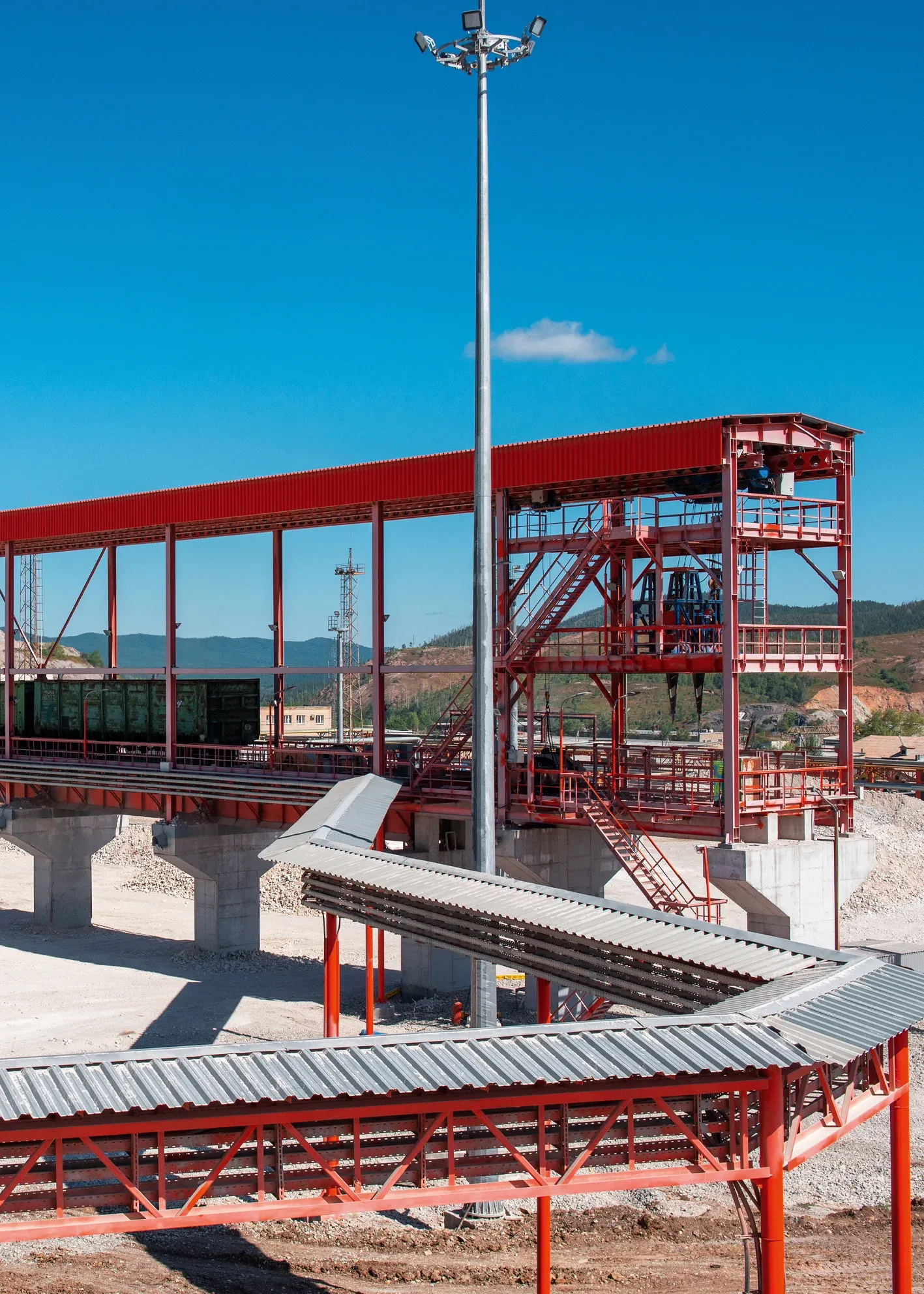
Record
dead-burned powder production facility
Railroad cars with raw materials from Siberia on a railroad overpass. Raw material preparation area.
Buildings of Beta Record 100-2, a multiple-hearth furnace
Raw materials from Magnezit Group’s Siberian deposits have certain valuable characteristics, including a high MgO content in the calcined substance and minimum impurity levels. The key priority of the company’s modernization program is to develop and implement advanced technology to unlock the natural potential of the unique raw material and transform it into high-quality products, thus opening up new opportunities for our customers.
The second Beta Record 100 multi-hearth furnace was built together with auxiliary infrastructure, with the railroad overpass as one of the most important facilities. A separate spur track leads to the railroad overpass to deliver raw materials from Siberia directly to the preparation area of the multi-hearth furnace.
Photo: Dima Galanternik / Artoniсa

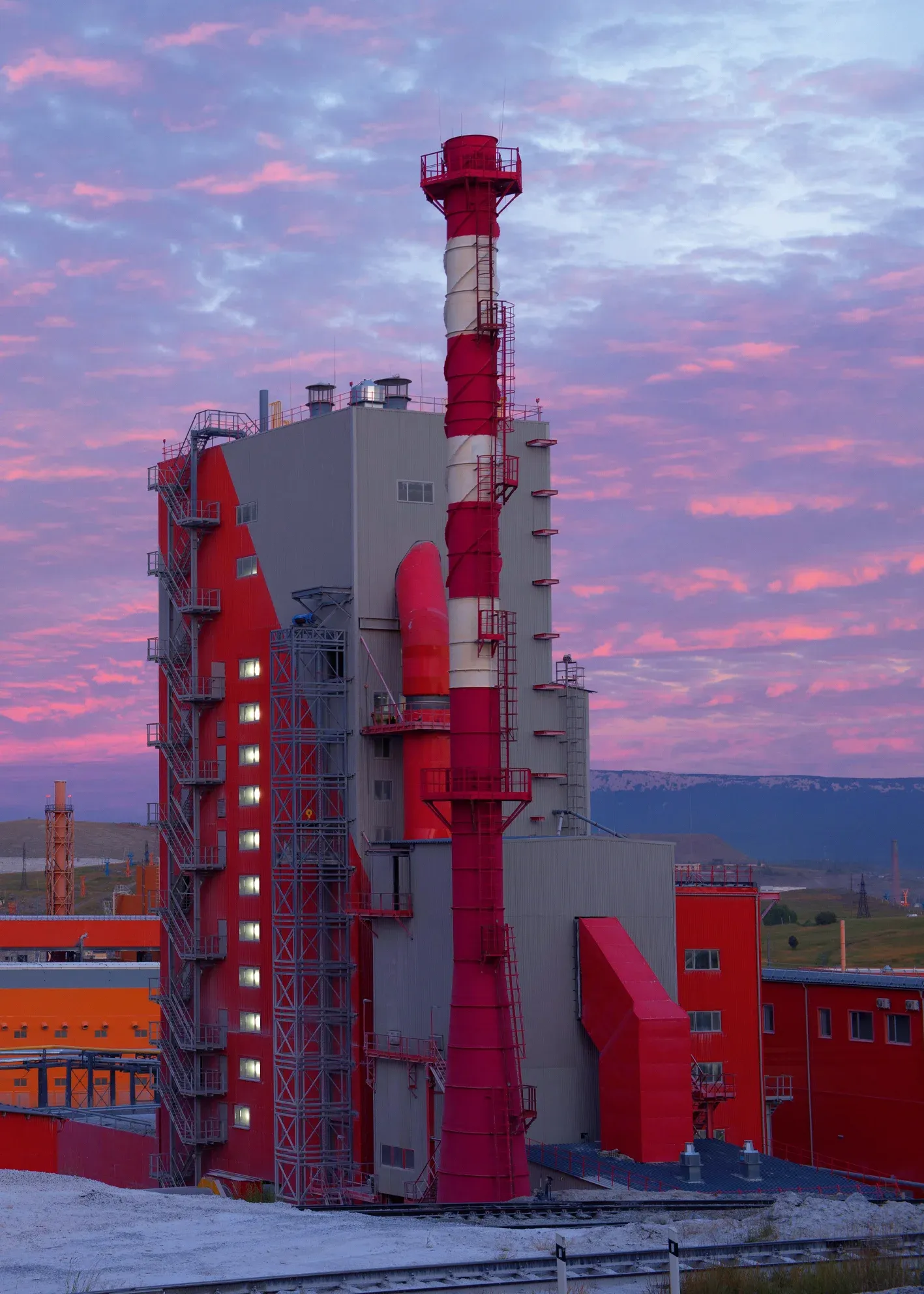
Record
dead-burned powder production facility
The Beta Record 100-2 multiple-hearth furnace facility.
In the background: the Avant-garde complex
In the multi-hearth furnace, magnesite is first decarbonized (CO2 is removed) by calcining. The maximum operating temperature of the furnace is 1,050 °C. The in-furnace treatment is a continuous process. The maximum furnace loading capacity is 25 tonnes per hour. The end product is the Russian Magnezit light-burned magnesia. The output of the Beta Record multi-hearth furnace is 100,000 tonnes per year. The Record complex includes two such furnaces.
Decarbonization in the multi-hearth furnace is the beginning of a double-step process to produce fused magnesia with a 98.5% MgO content for the Russian Magnezit line. The second step is dead-burning in shaft kilns. The Satka production site has two shaft kilns, both being part of the same Record complex.
Photo: Dima Galanternik / Artoniсa
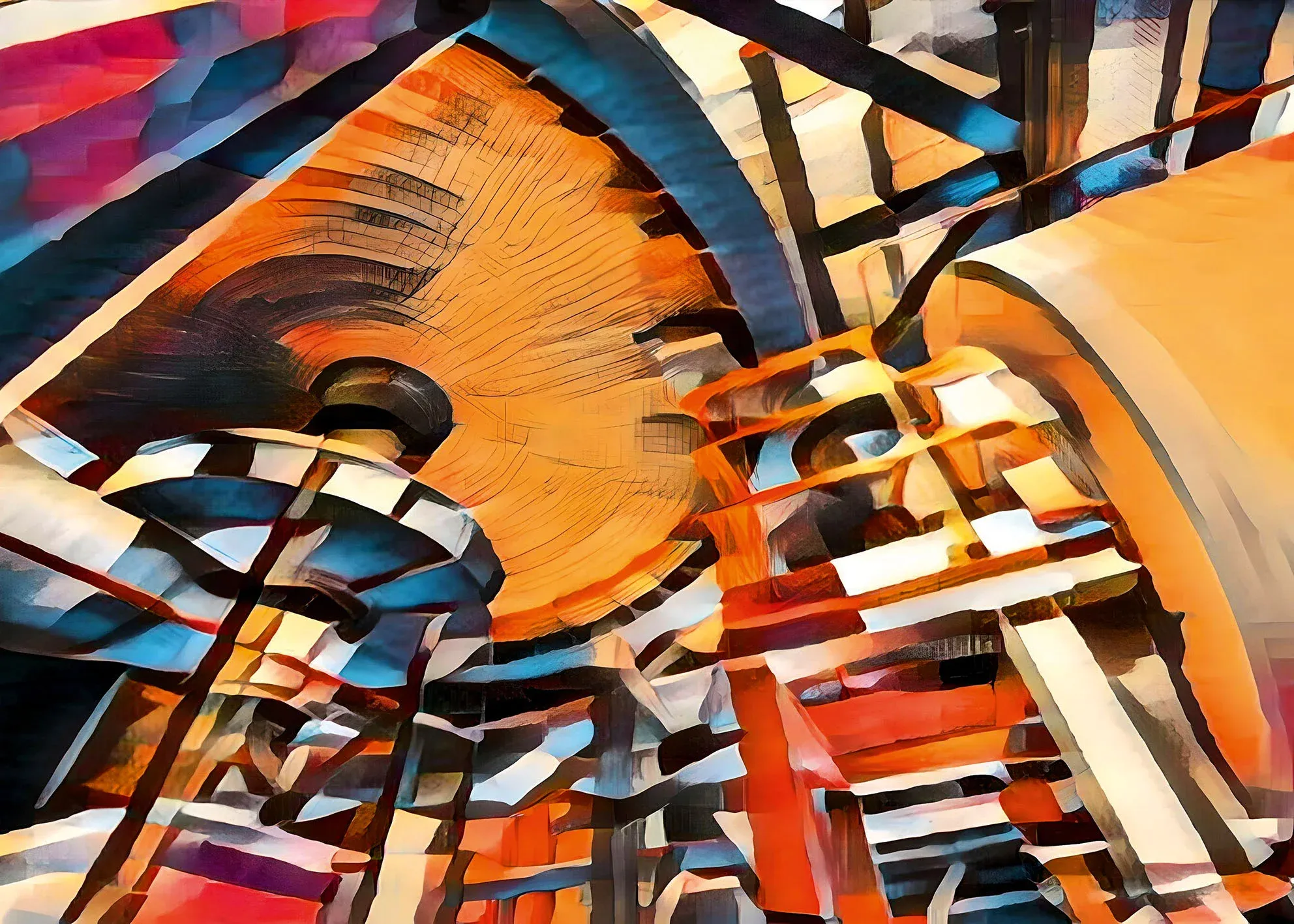
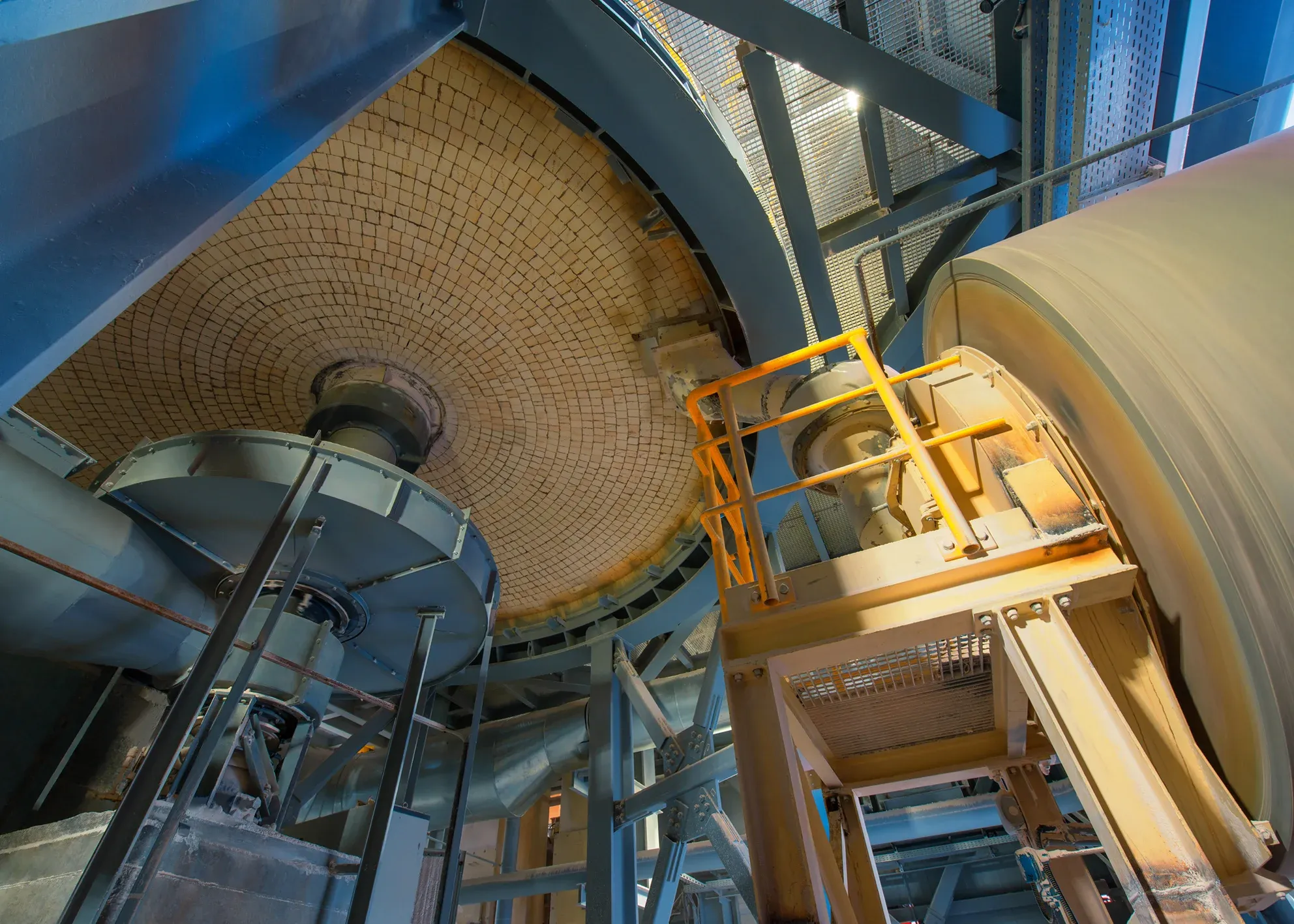
Record
dead-burned powder production facility
View of the lowest — 19th — hearth of the Beta Record 100-2 multi-hearth furnace from the service platform
The decarbonization process is based on the counterflow to the products of combustion — from the uppermost hearth number one down to the one below driven by the movement of the central shaft and vanes. The process is fully automated, including raw material charging and calcining. The furnace consists of 19 hearths; 11 of them are equipped with 42 blowpipes.
In the middle of the furnace, hearth temperature reaches around 900–1000 °C, depending on the preset parameters. The design of the Beta Record 100-2 furnace makes it possible for the heat treatment temperature to be regulated to an accuracy of 10 °C. This allows impurities to be removed from the product by thermal beneficiation. These processes result in obtaining light-burned magnesia of guaranteed quality.
Photo: Dima Galanternik / Artoniсa
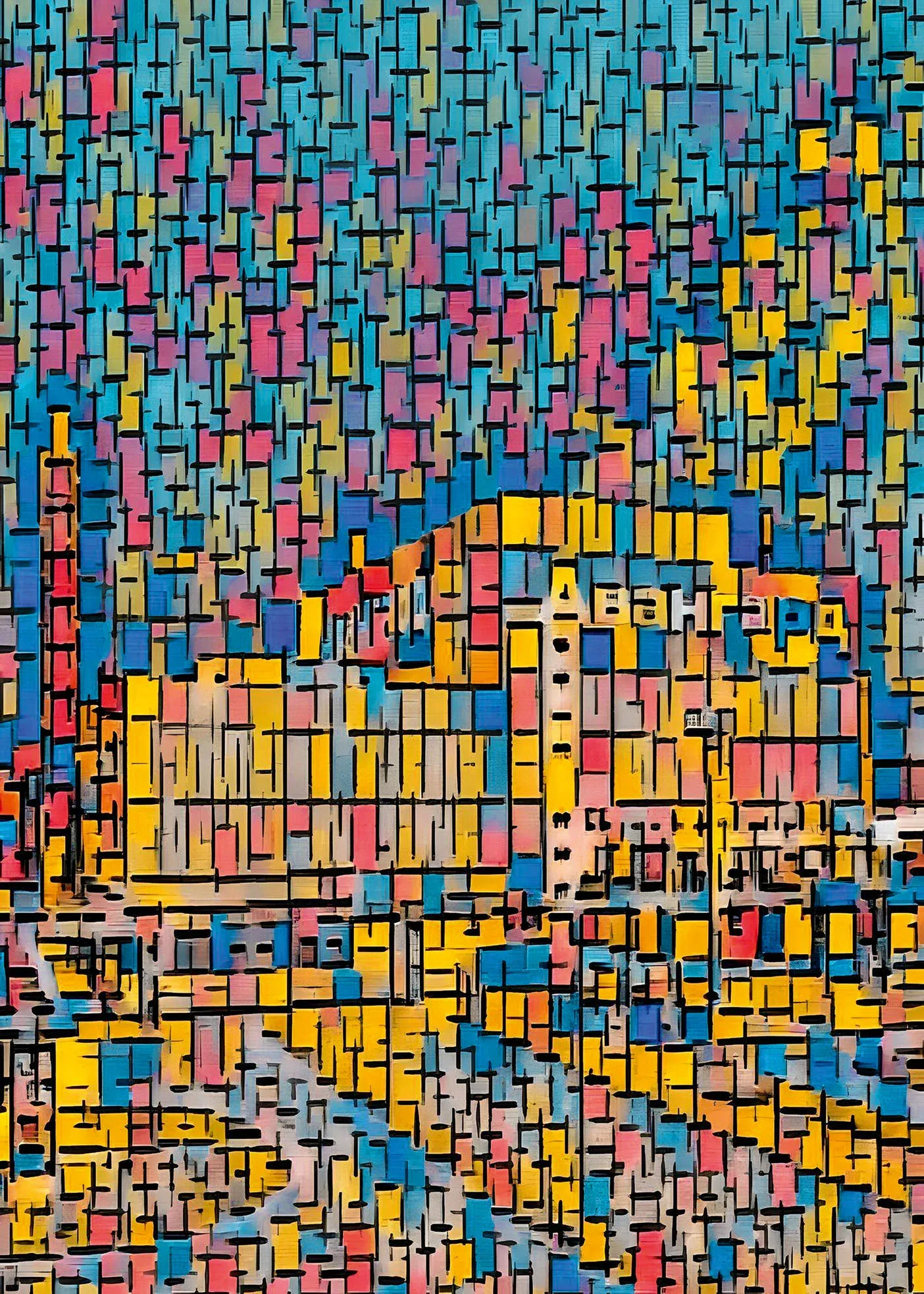
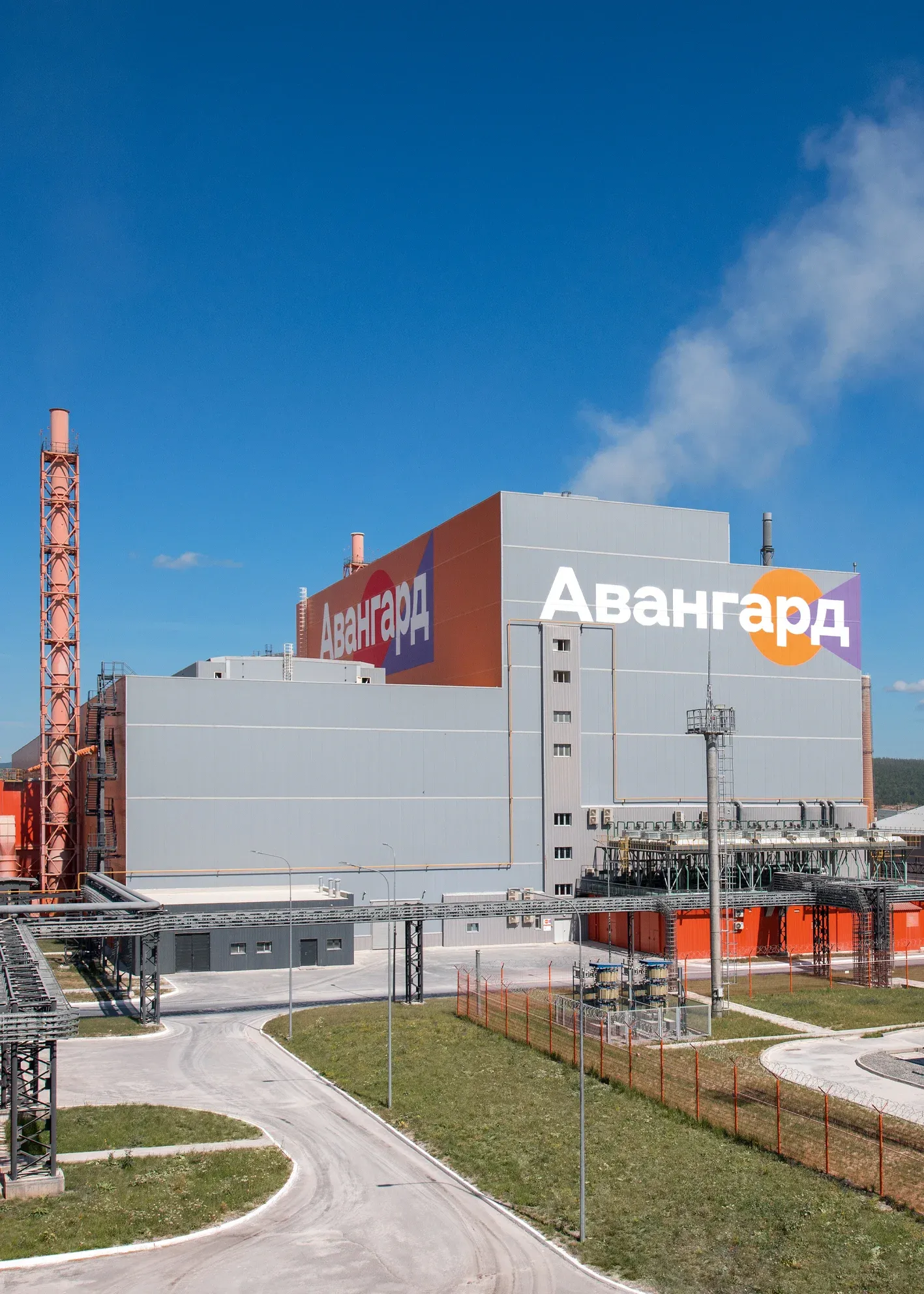
Avant-garde
fused powder production facility
View of the entrance to the fusion area and control room. Main building of the facility
The double-step process for producing fused magnesia from Siberian raw materials is completed at the Avant-garde complex, where electric furnaces are used. The fusion process results in high-purity, coarse-grained magnesia for the Russian Magnezit product line. Products containing this type of magnesia exhibit important characteristics for linings — higher resistance to slag and aggressive melts, and dense microstructure.
The new production facility has a planning and monitoring system for tracking quality metrics throughout the entire process, thus preventing defects and making the future product tailored to the customers’ needs.
Photo: Dima Galanternik / Artoniсa
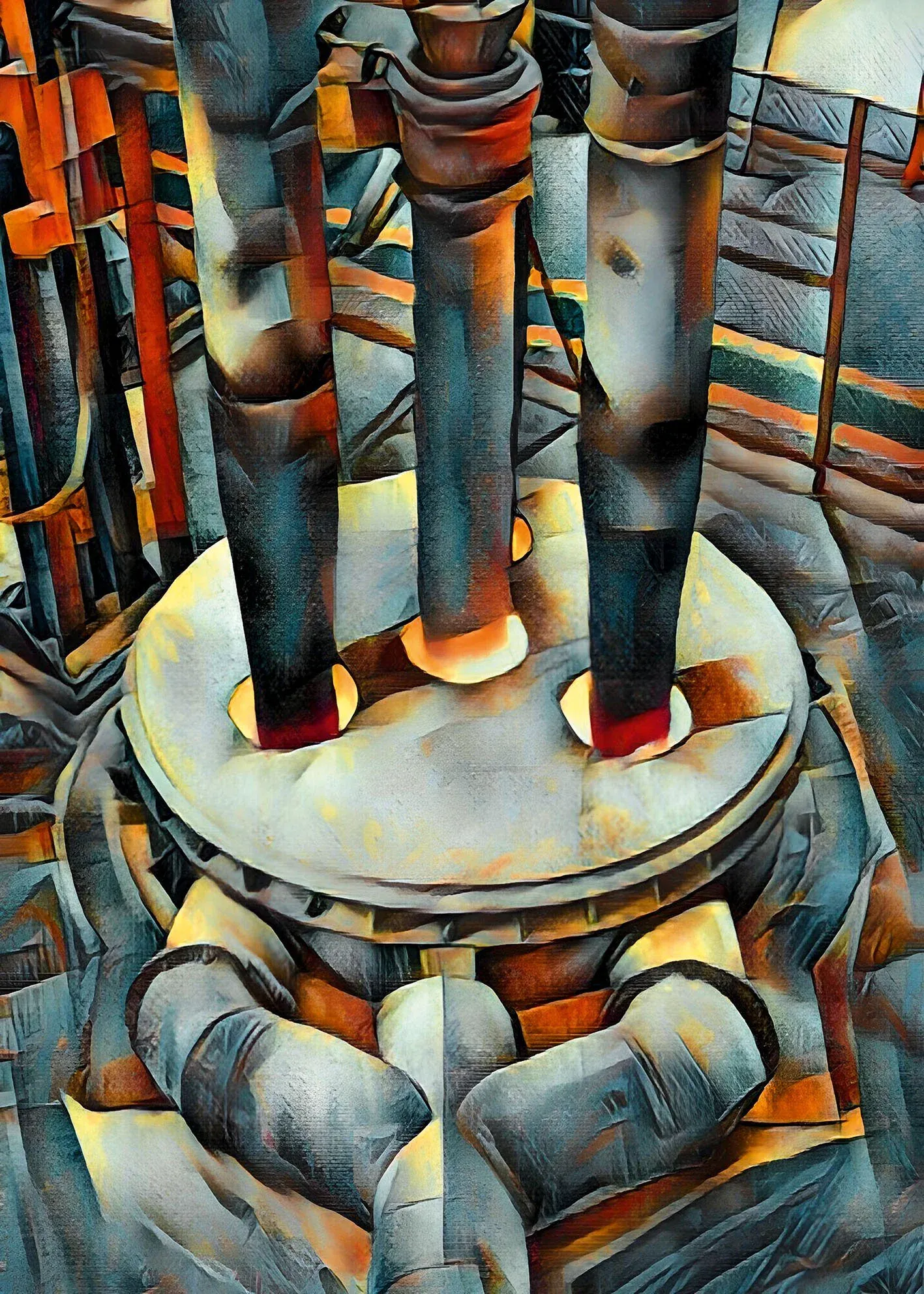
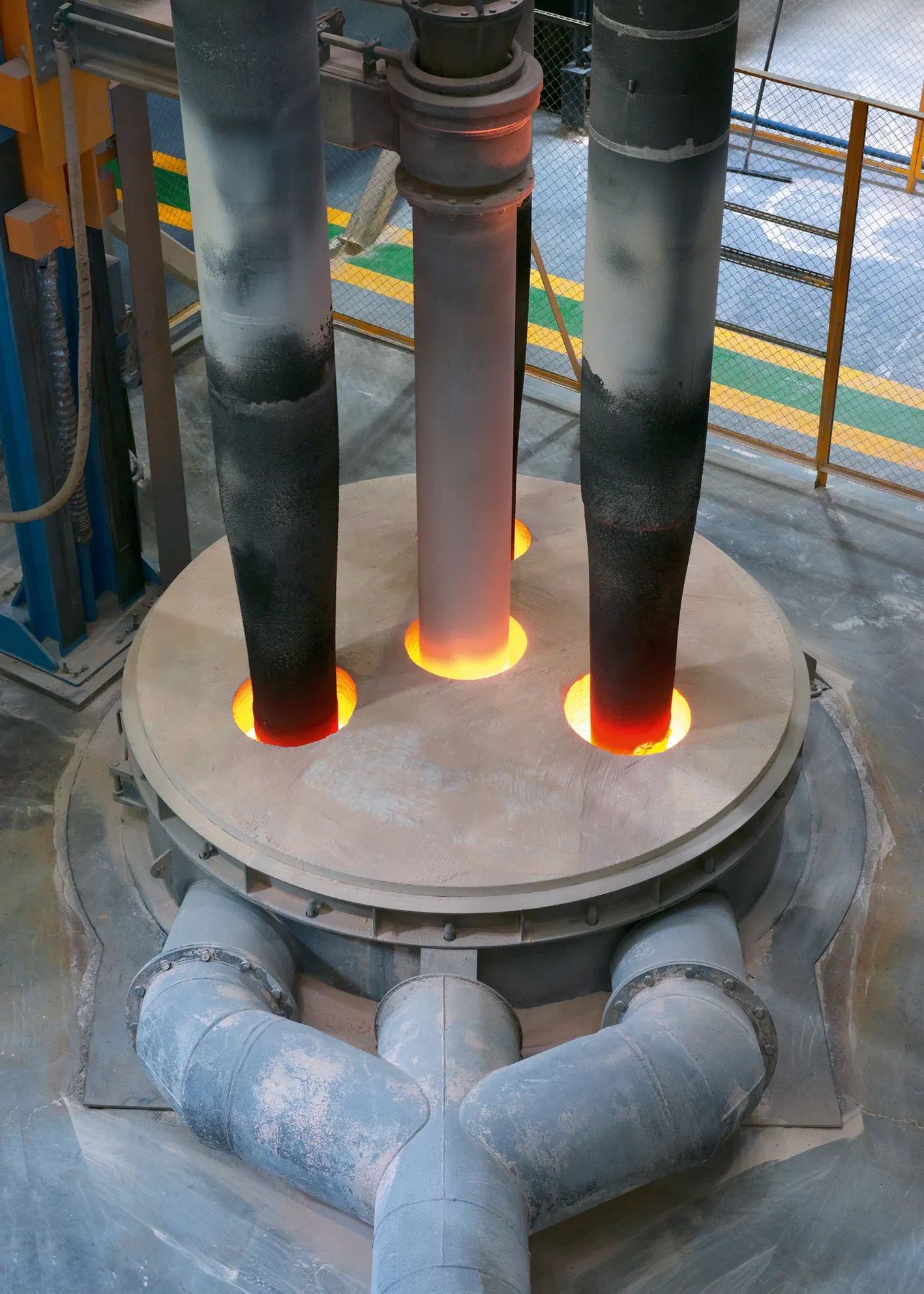
Avant-garde
fused powder production facility
The Delta Avant-garde 10–1 electric arc furnace at the final stage of the fusion process. Furnace platform. Fusion area
Avant-garde has five three-phase electric arc furnaces with unique design solutions:
— a rotary hearth to ensure even depth of fusion of the magnesia blocks, thus reducing the amount of unmelted raw material (crusts and spillage);
— an automated dosing system to ensure even distribution of the raw material across the smelting bath area. This results in reduced raw material consumption during charging and smaller percentage of unmelted raw material;
— a continuous fusion system and a hydraulic electrode-positioning system to make the fusion process stable and precise, as well as cut down the consumption of raw materials and lengthen the service life of electrodes.
Photo: Dima Galanternik / Artoniсa
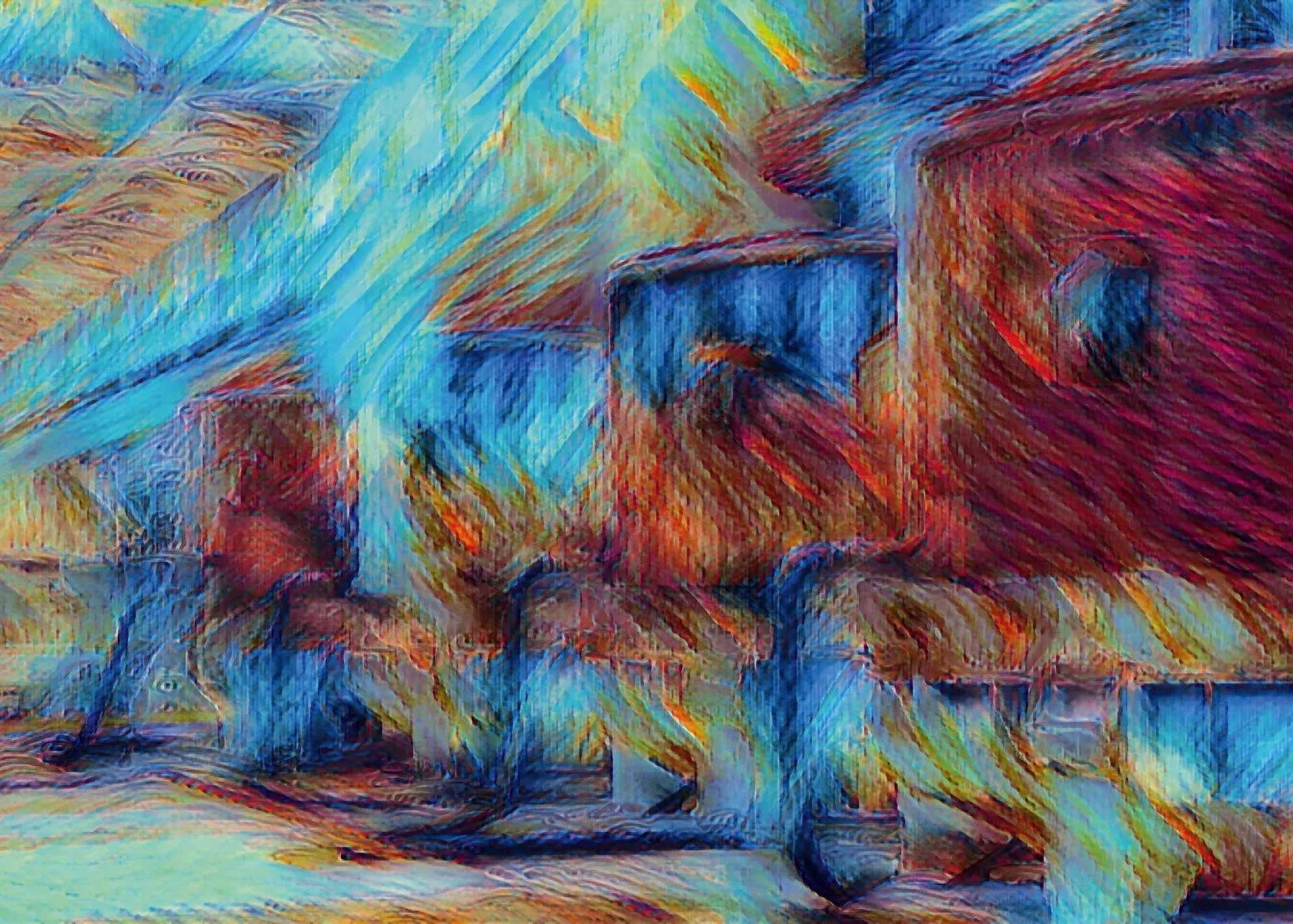
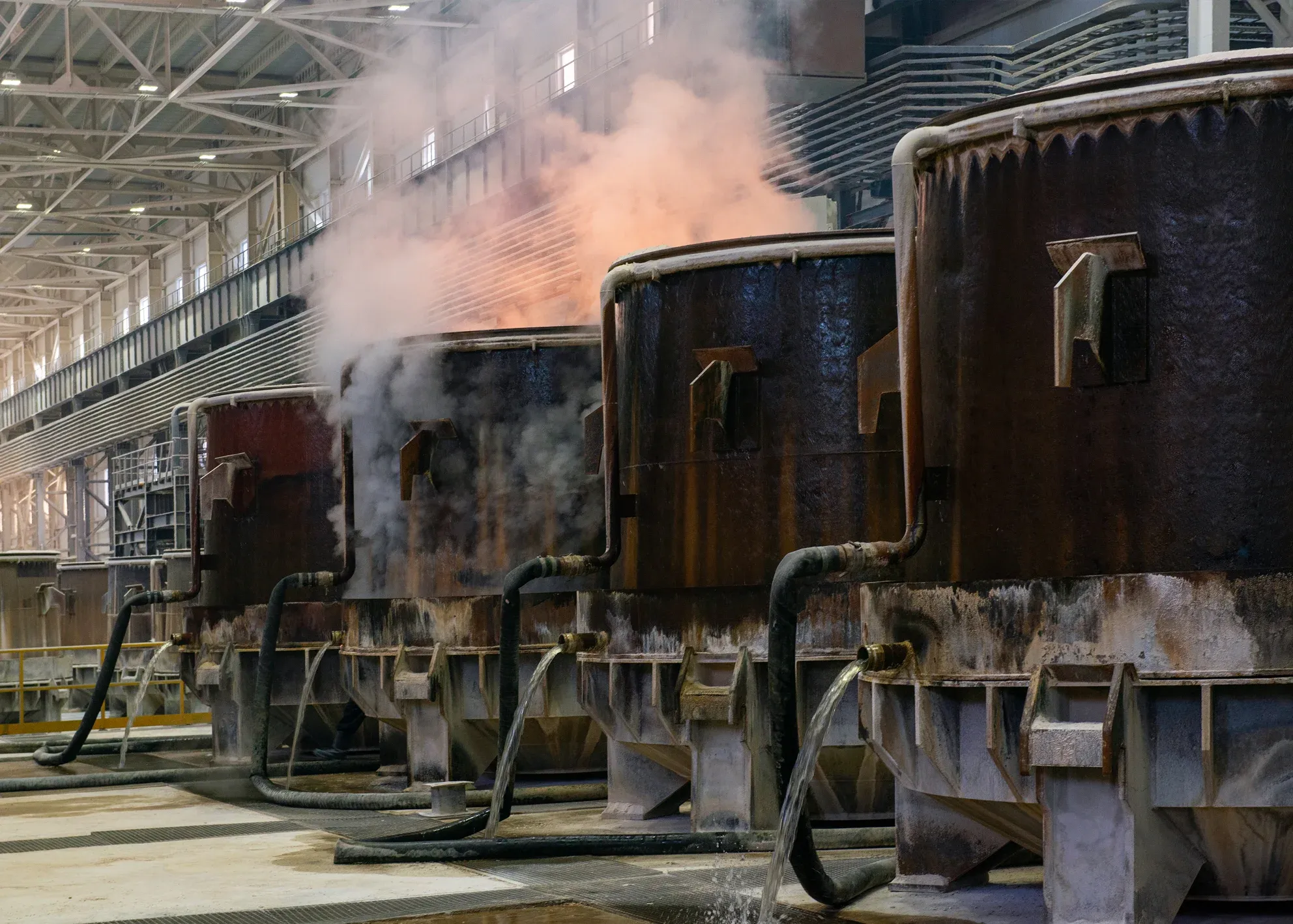
Avant-garde
fused powder production facility
Furnace baths with fused magnesia blocks in the water-cooling area. Cooling area
The bigger the periclase crystal is, the smaller the specific surface of the periclase grain and the melt contact area, and thereby the longer the lifetime of the lining. Active crystal growth occurs when periclase blocks are being cooled due to temperature differences. The production technology employed at Avant-garde is based on the ability to control crystal growth using a double-stage cooling methodology.
After fusion, the bath with fused blocks undergoes water cooling for 48 hours. Then the furnace bath is moved to the air cooling zone, where the cooling process continues for six more days at the normal surrounding temperature. Before crushing and sorting, the blocks are additionally cooled down for 24 hours outside the bath.
Photo: Dima Galanternik / Artoniсa
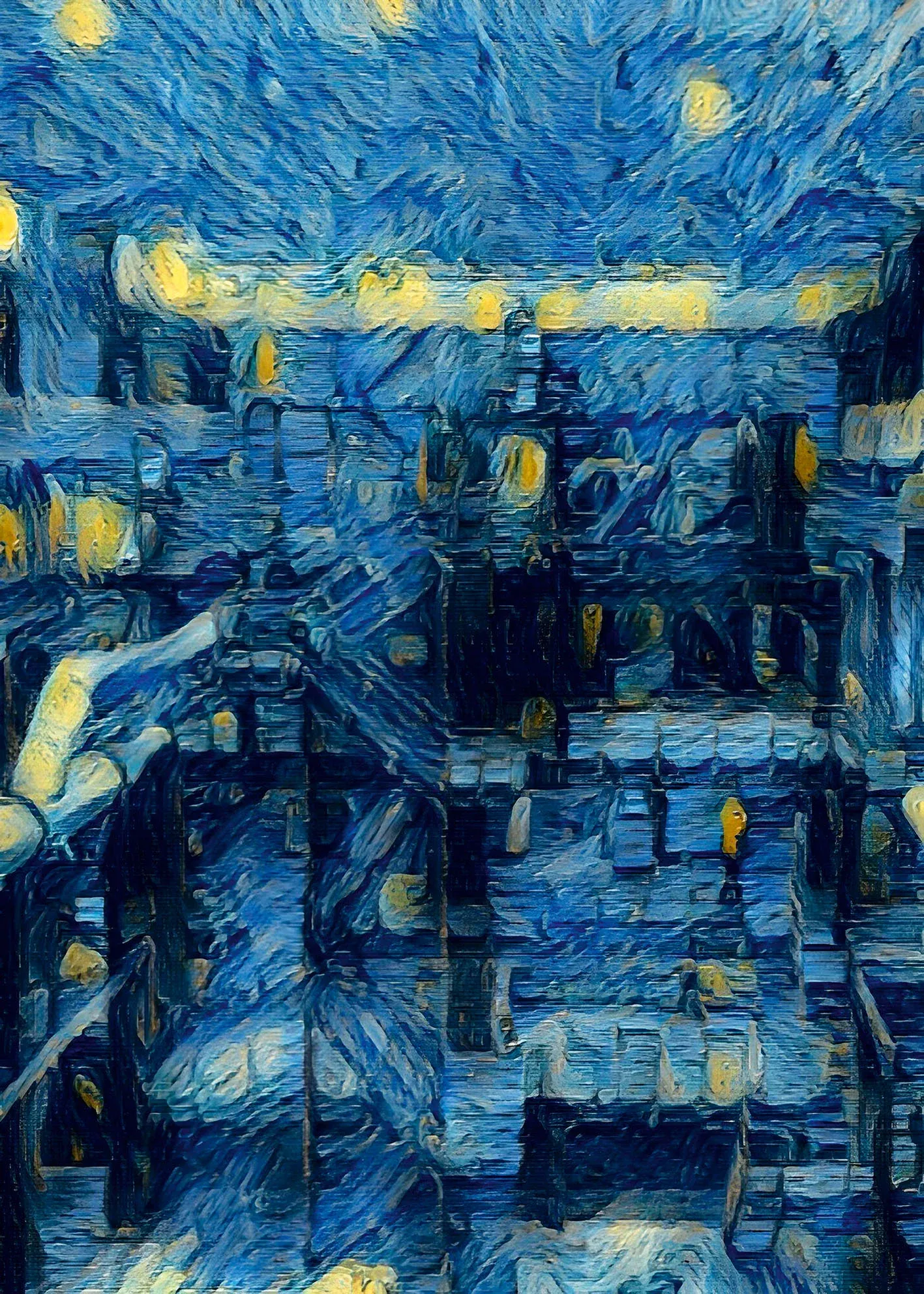
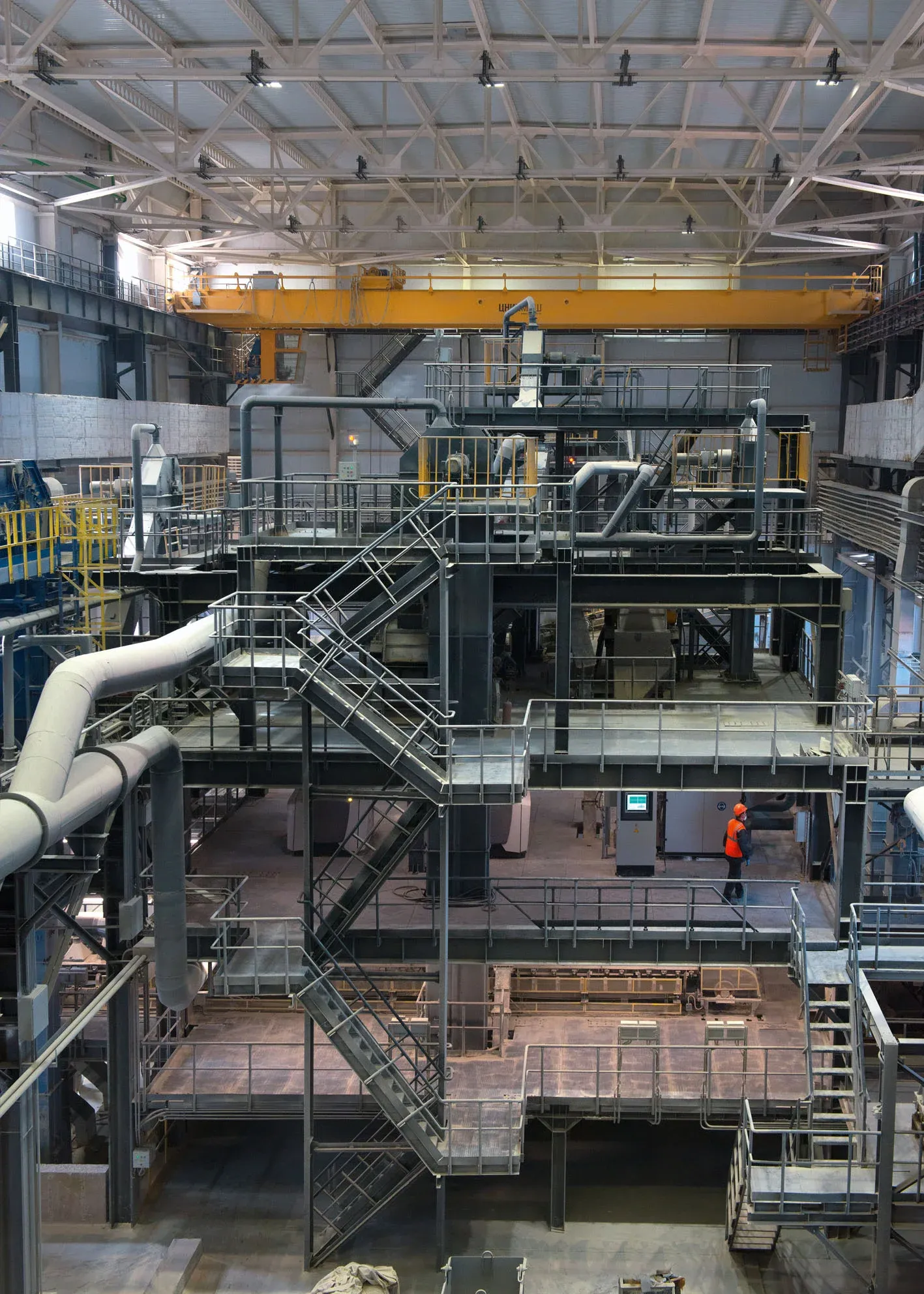
Avant-garde
fused powder production facility
View of optical sorting systems. Crushing and sorting area
The crushing and sorting area has three operating sorting systems for automated optical sorting of magnesia powder and crust. Each separator has two chambers to scan free-falling 40–20 mm grade material and a computer that analyzes the color and transparency of each fragment and transmits the results to a system comprising 256 air-operated valves. The latter separates crust from valuable product using air streams. The sorting rate is 25,000 particles per second.
Optical sortation increases magnesia yield from each block by 15%.
Photo: Dima Galanternik / Artoniсa
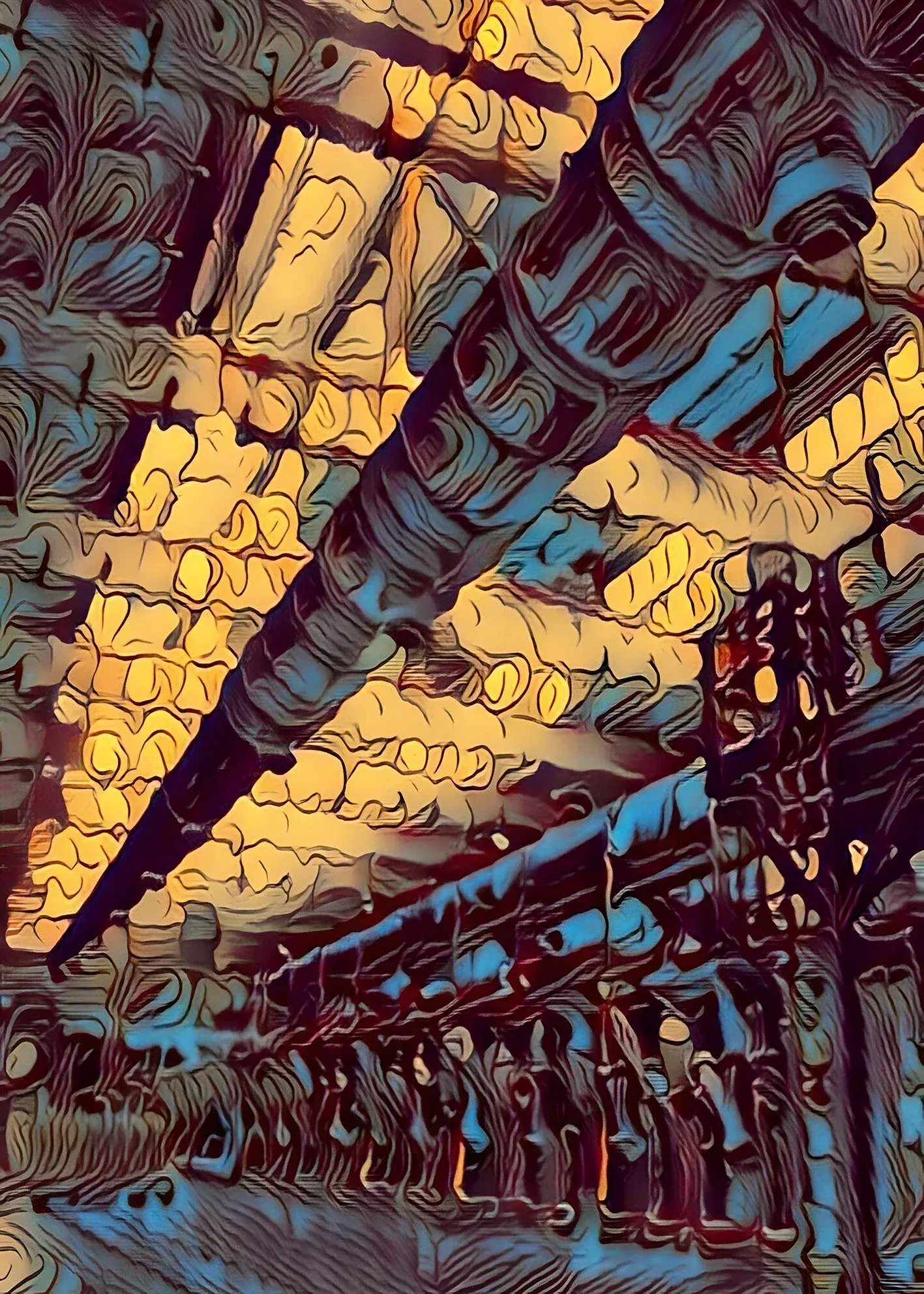
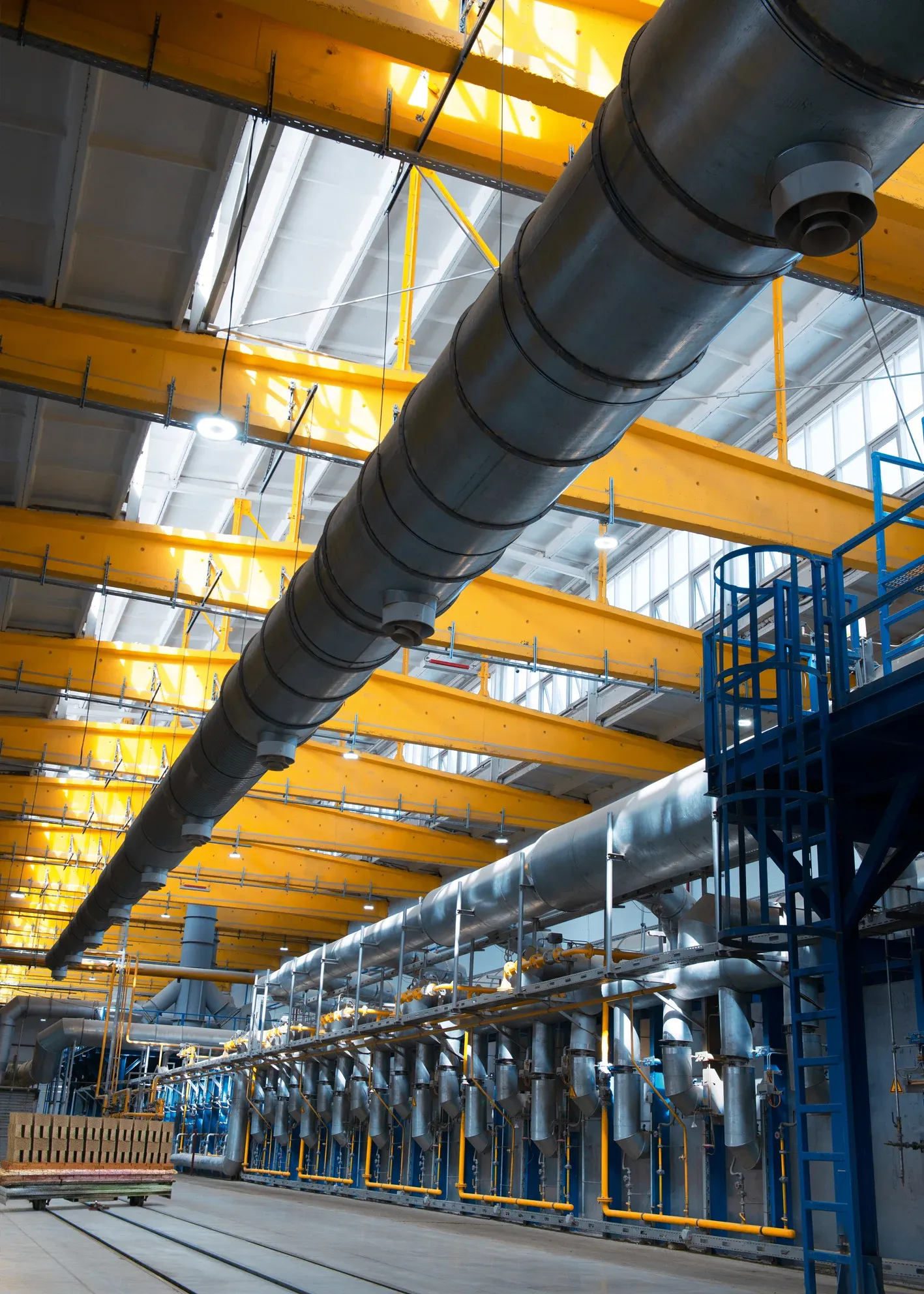
Impulse
fired shaped products facility
View of the Omega Impulse 40 tunnel-type kiln and a kiln flat-deck car with products. Firing area. Production line of shaped magnesia-spinel products for the cement industry.
The new line has been designed to automate the process and minimize human error.
Uniform brick treatment and minimized energy consumption in the Omega Impulse 40 kiln is achieved through automated control of the firing temperature, particular blowpipe arrangement, and high-quality lining structure. The temperature differential is 5 °C or less. The kiln operates at 1,750 °C.
A completely new layout has been developed for putting bricks on the kiln flat-deck cars, which is instrumental in improving the firing process, minimizing possible inherent defects, and enhancing durability.
Photo: Dima Galanternik / Artoniсa
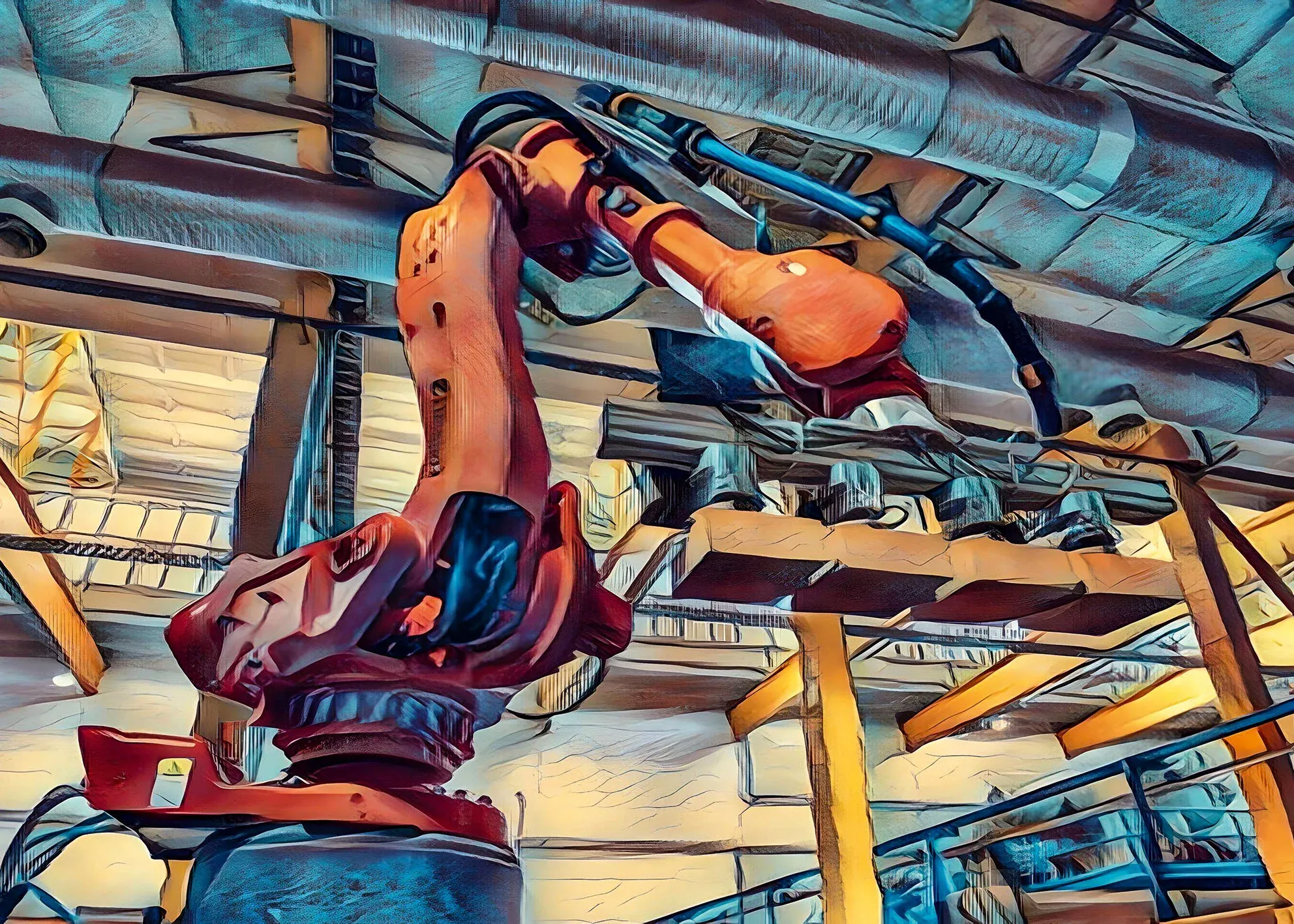
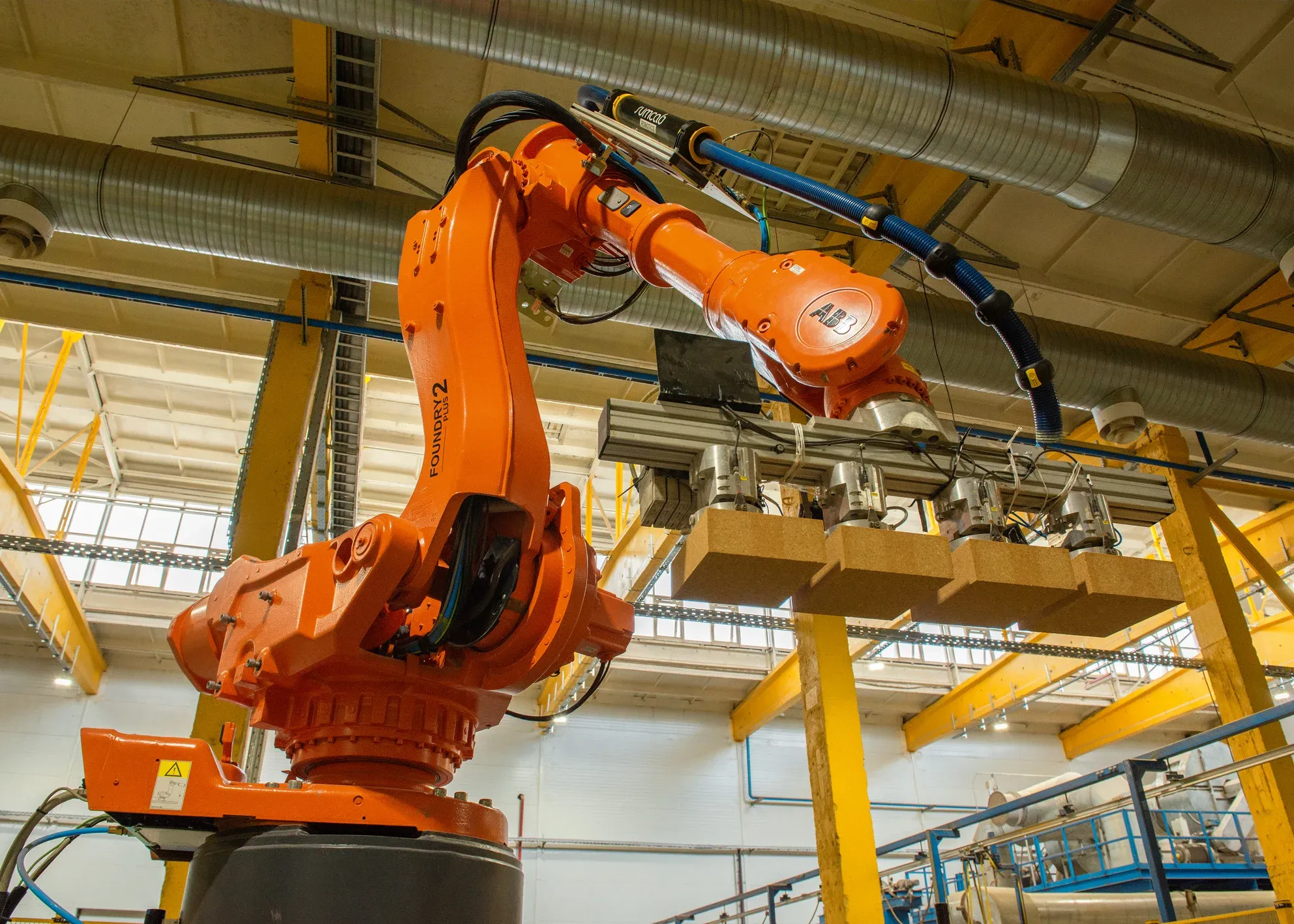
Impulse
fired shaped products facility
A manipulator sorting products after firing. Sorting and packaging area. Production line of shaped magnesia-spinel products for the cement industry
This area is a unique robot-equipped project for automated product sorting. Every brick that comes from the kiln is examined for internal and external defects. Its external parameters are monitored with the help of six 3D cameras. As many as 48 visual parameters are tested, including dimensions, chipping, flatness, etc. The internal defects are revealed using acoustic testing (the facility earlier used the ultrasound method at this stage, but it allowed checking selected bricks only).
The non-stop process continues with applying temperature resistant lining and color marking to the verified products, after which a manipulator places them onto a pallet, interlaying the rows with polyethylene film and cardboard.
As the area combines so many solutions in a single automated system, it has become possible to significantly boost its throughput capacity, which is 4,700,000 bricks a year; the monitoring process takes 4.9 seconds per brick.
Photo: Dima Galanternik / Artoniсa
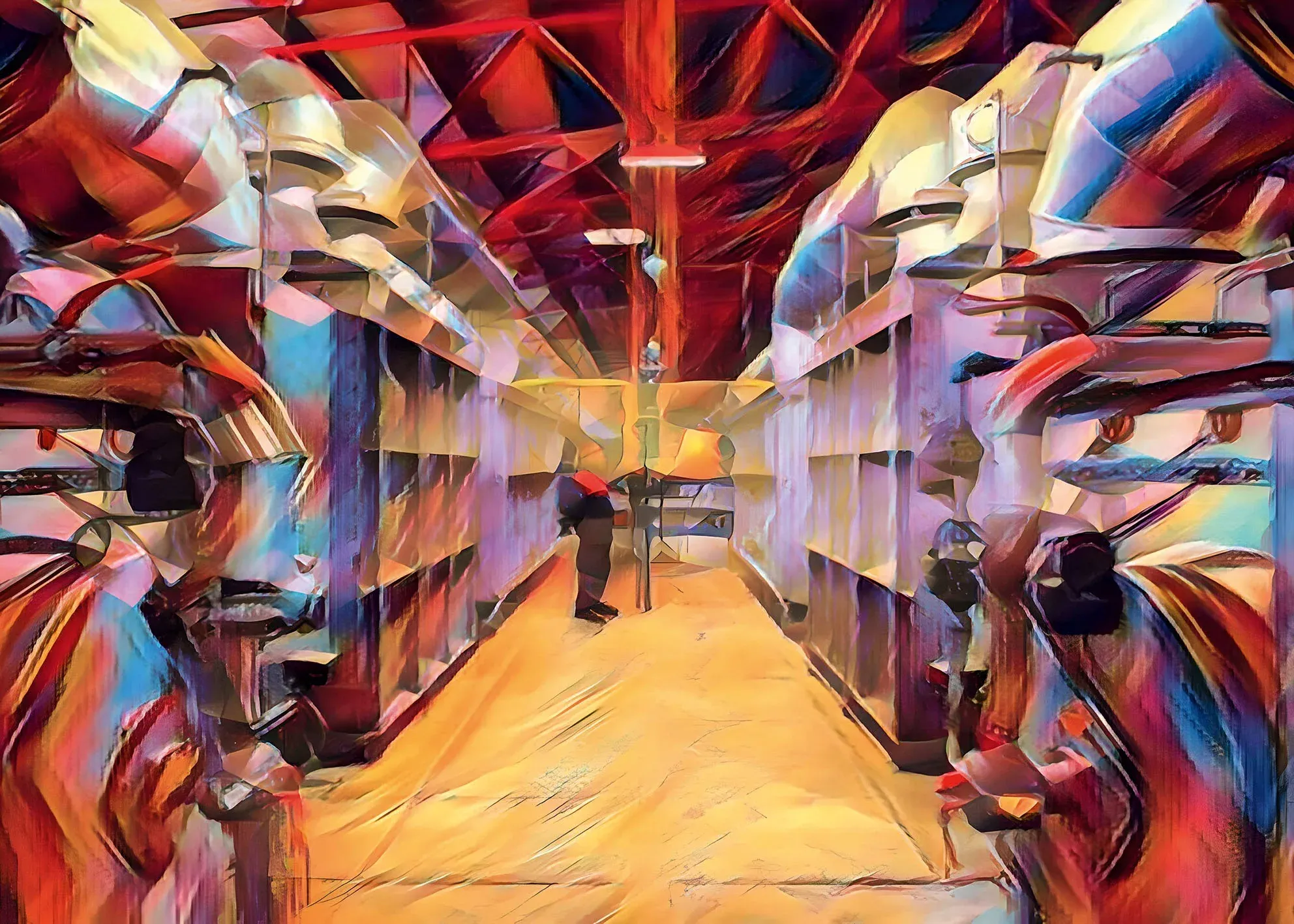
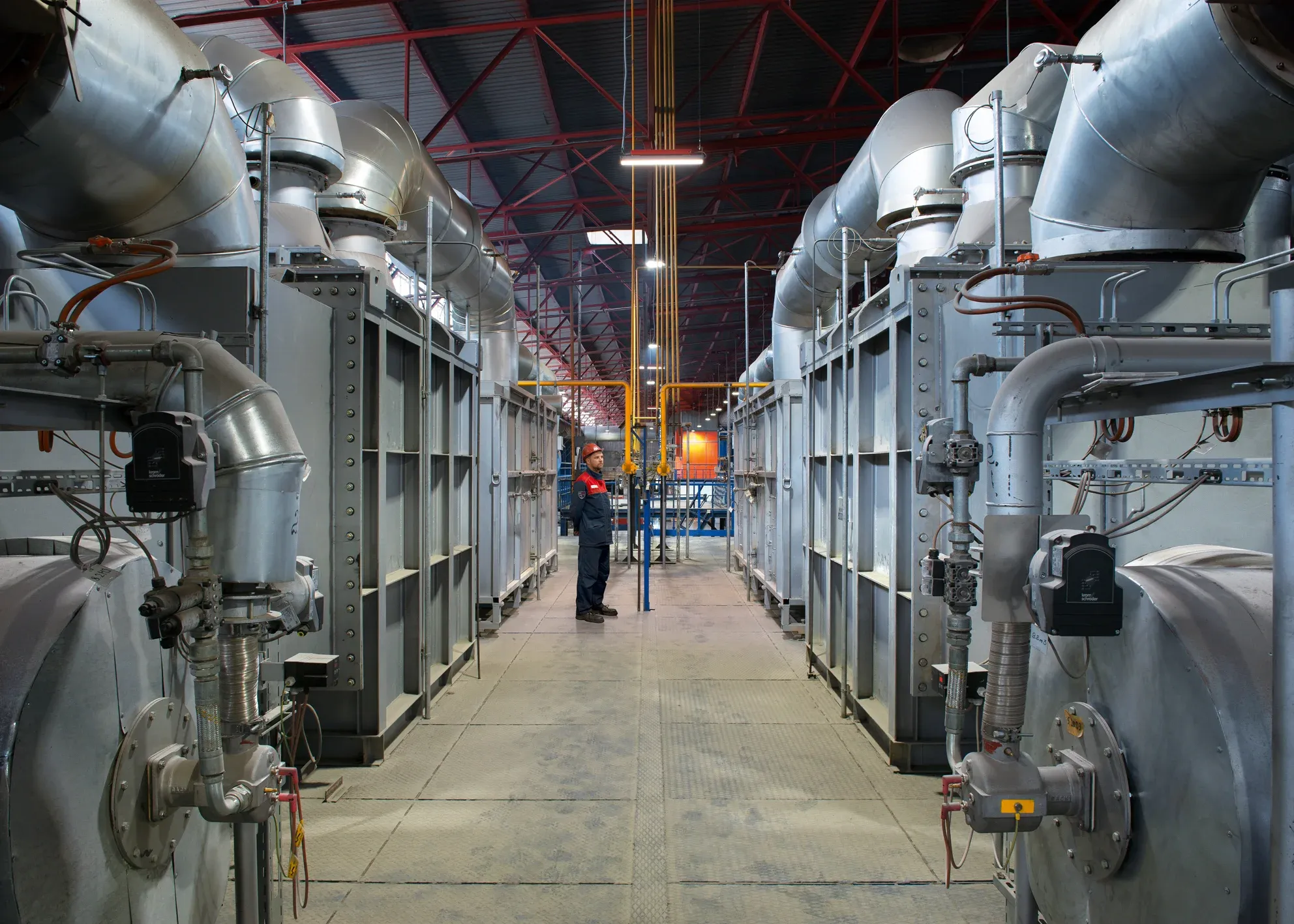
Progress
non-fired shaped products facility
An operator of the Sigma Progress 60 seasoning kiln in the waste gases burning section. Heat treatment area. Production line of magnesia-carbon bricks for the iron and steel industry
At the heart of the new line are two Sigma Progress seasoning kilns. Flat-deck cars with products continuously and smoothly move through the heating, drying, and cooling zones in a controlled manner. It takes 12 hours to process one car; the cooling time is 3.5 hours. The thermal tunnel can accommodate 45 cars at a time. The drying process in the kiln involves uniform heating of the heat carrier, ensuring uniform heat treatment of each brick. The operating temperature of the kiln is 200–260 °C.
The seasoning kilns are extremely energy efficient: they consume nearly half as much gas as the formerly used ones, while their productivity is three times higher.
Both furnaces are equipped with a waste gases burning system: all the by-products remaining in the gas-air mixture after the heat treatment of products are completely burned at 750 °C, in a special zone.
Photo: Dima Galanternik / Artoniсa
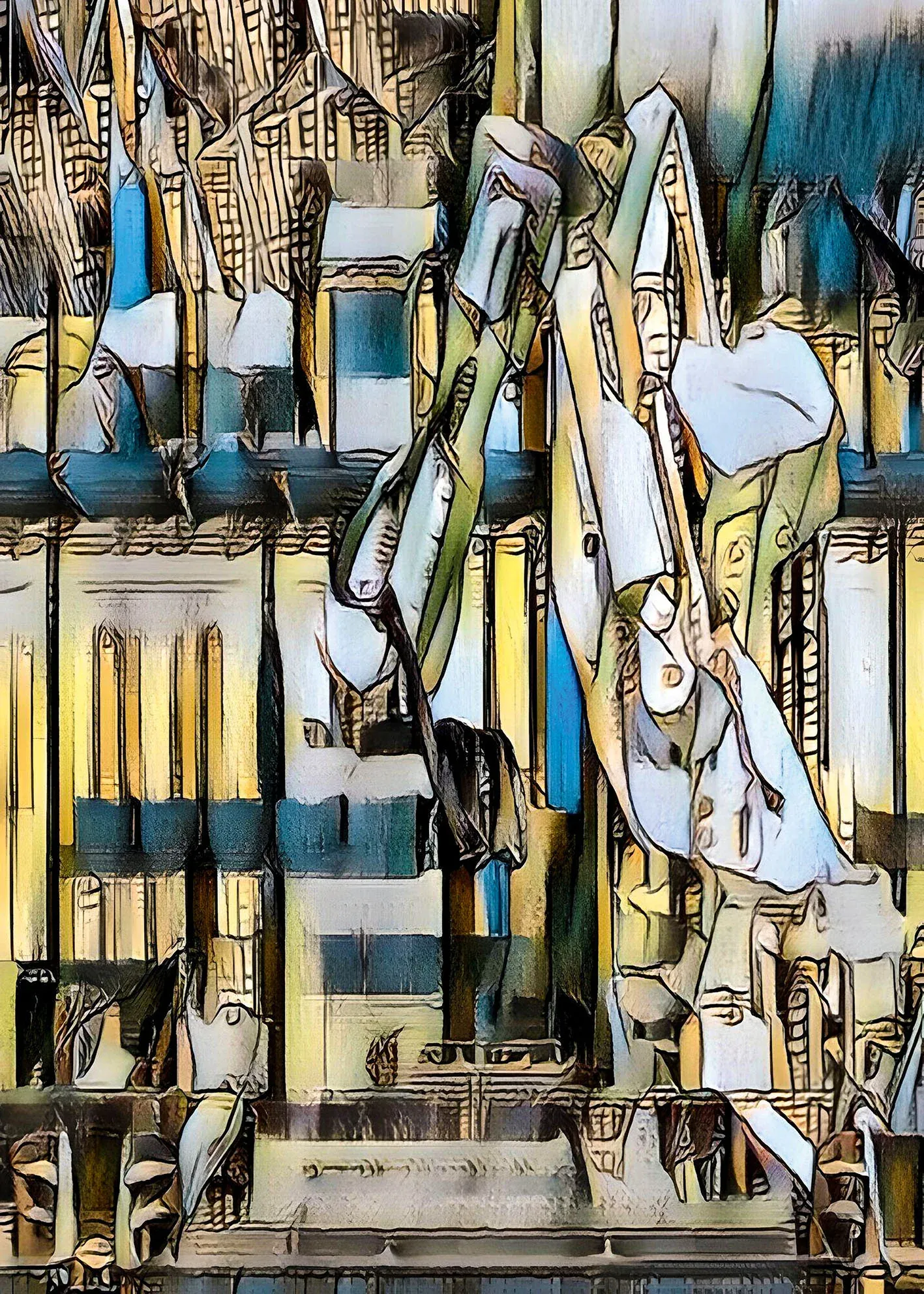
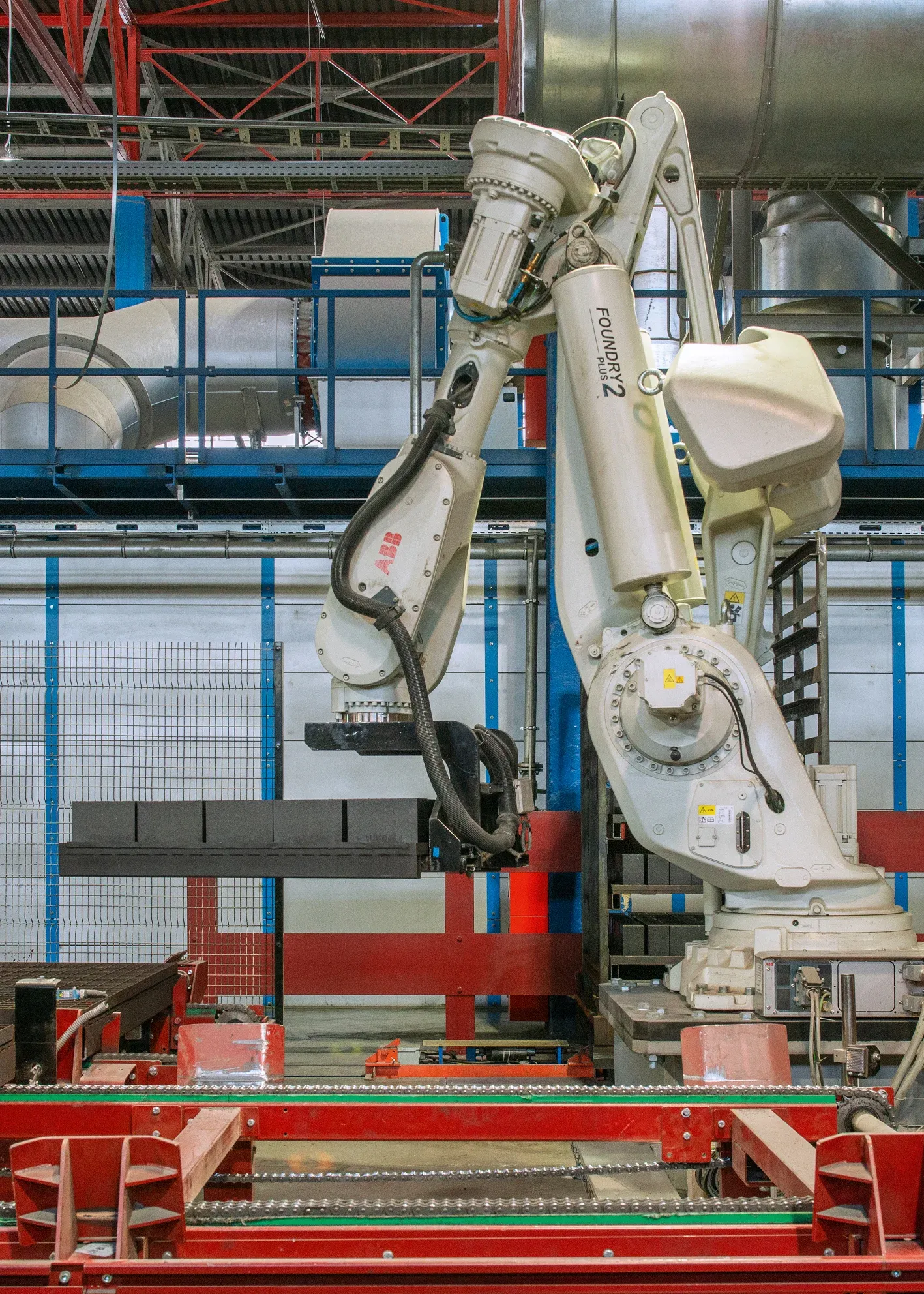
Progress
non-fired shaped products facility
A manipulator removing a pallet with products after heat treatment. Sorting area. Production line of magnesia-carbon bricks for the iron and steel industry
All the processes — from mixing to sorting — are fully automated. The line needs only eight people on one shift.
It also has a well-designed logistics system: the core equipment is concentrated in one room, the process for moving the products around the workshop is almost entirely automated, and all the unnecessary movements have been eliminated. This makes it possible to prevent chipping, cracking, and other product defects.
On the sorting line, a manipulator picks up the pallets with products from the rack and puts them on the conveyor. Pallets are then distributed between five sorting lines.
Photo: Dima Galanternik / Artoniсa
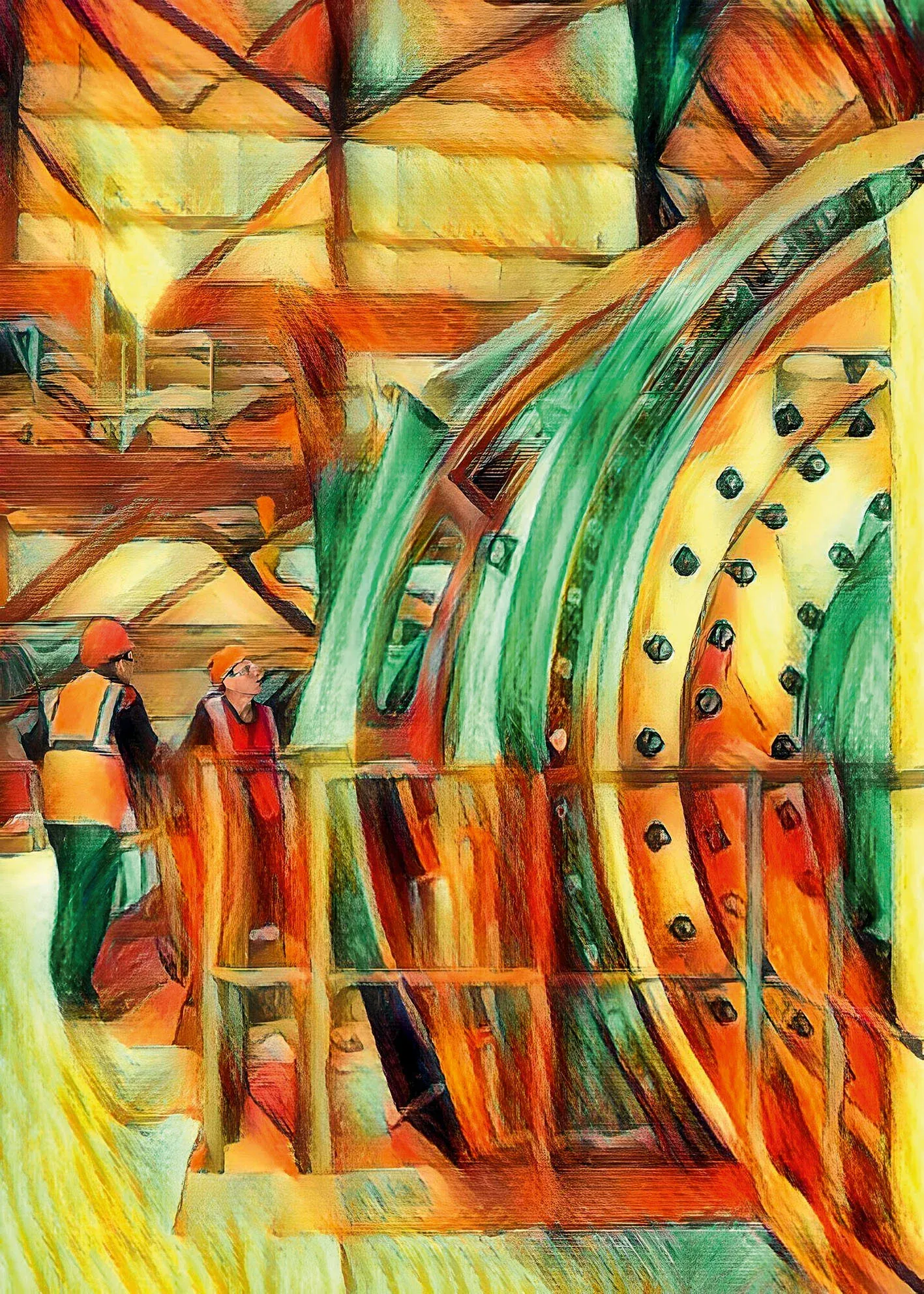
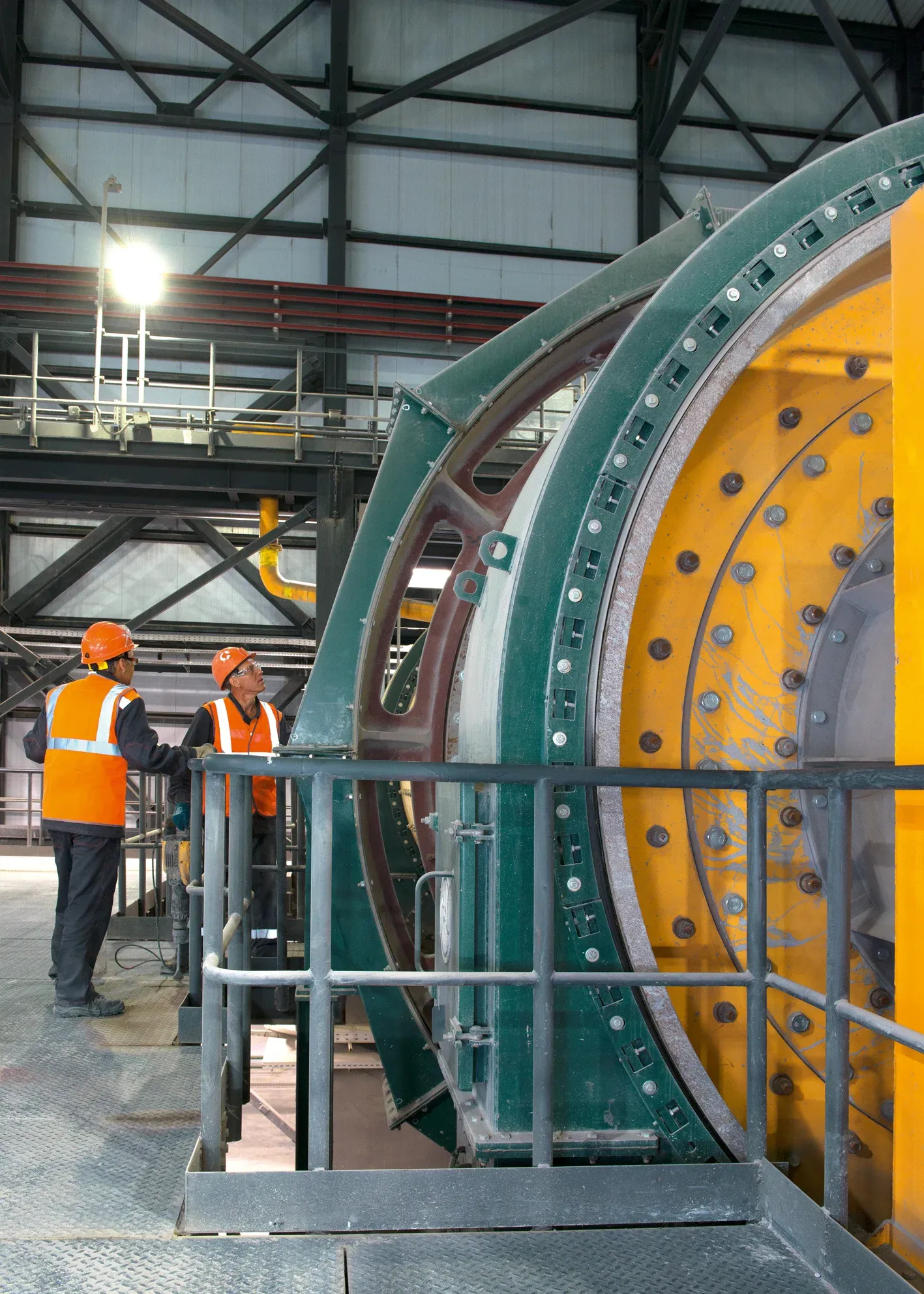
Stowing facility
of the Magnezitovaya Mine
Operators of the crushing machinery near grinding mills. Milling area
By 2029, Magnezit Group plans to completely abandon open-pit mining and focus on underground mines. In order to keep on developing new mine floors at Magnezitovaya Mine, it is necessary to stow the goaf.
The two grinding mills grind and mix a hardening mixture (similar to concrete) at a rate of 110 cubic meters per hour. Then it flows by gravity into mining chambers through pipes laid inside boreholes and mine shafts.
The underground cavities formed by mining are thus filled to ensure the stability of the land surface after complete extraction of the mineral deposits.
Photo: Dima Galanternik / Artoniсa
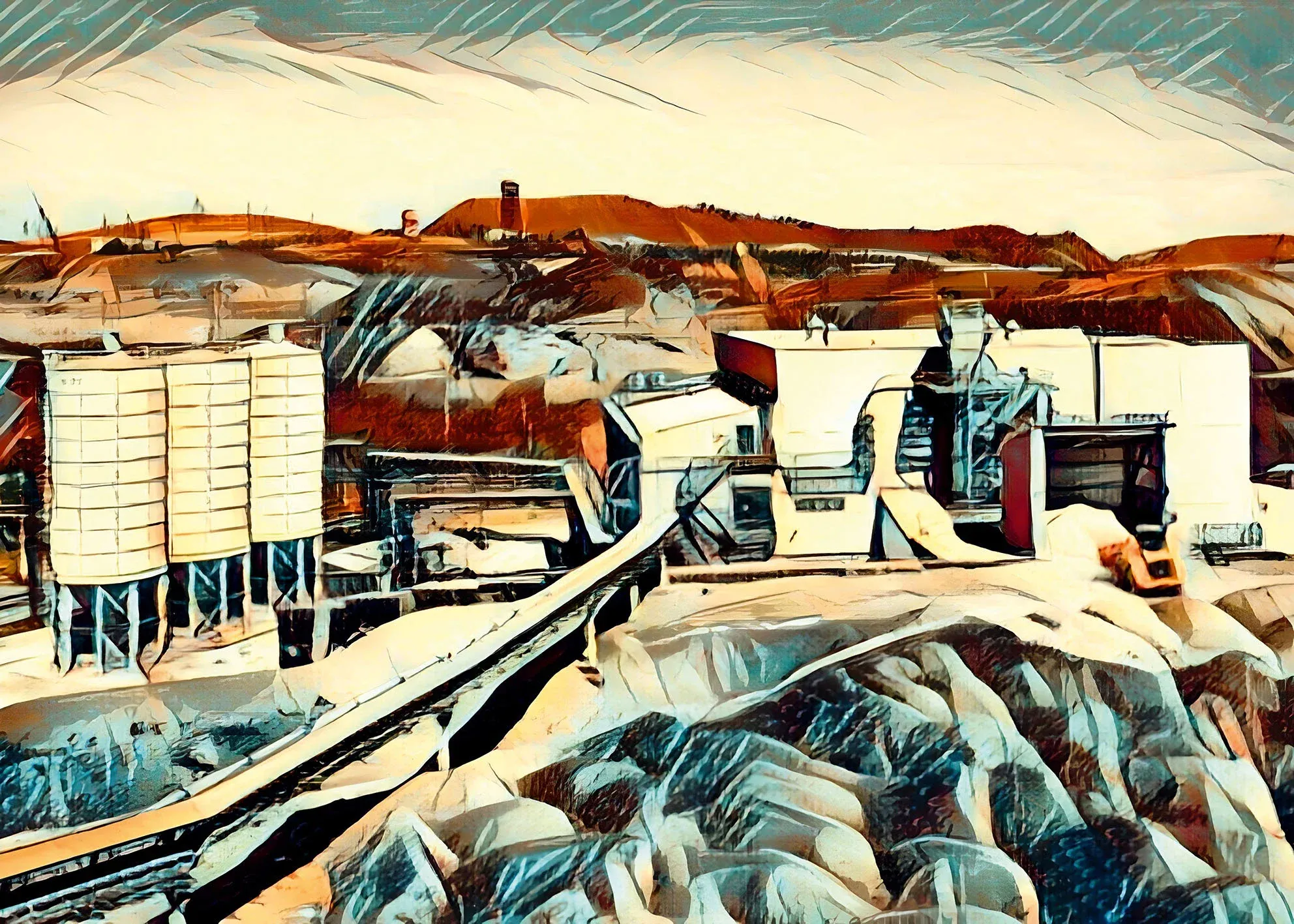
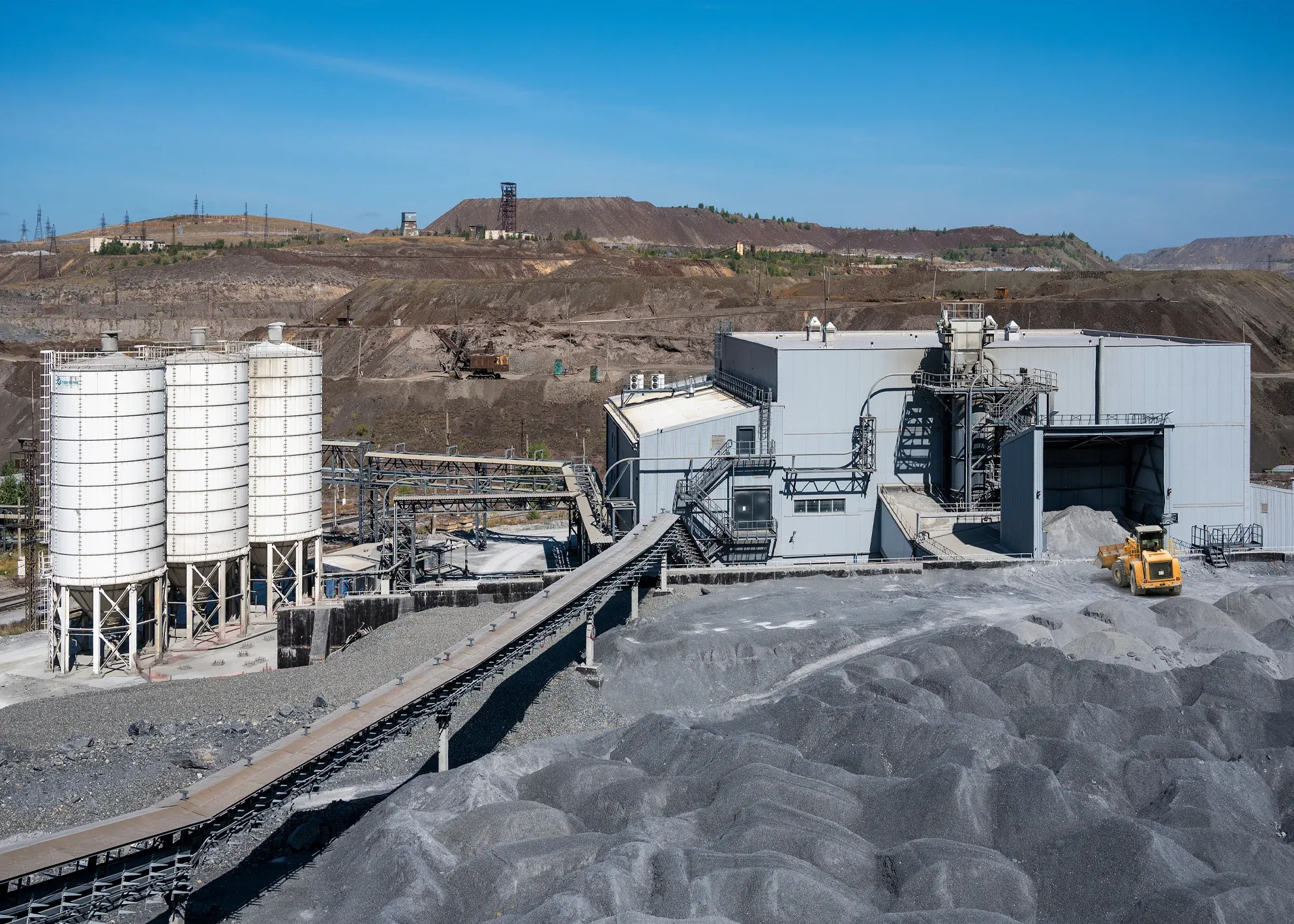
Stowing facility
of the Magnezitovaya Mine
Stowing facility building and open storage of dolomite
The stowing material consists of cement, dolomite, and water. The cement is stored in bins with a capacity of 3,000 tonnes and a height of 22 meters each. The cement mixture is automatically pumped from the bins into bin feeders.
The composition of the stowing material was devised specifically for the Magnezitovaya Mine, which took nine months. The material meets certain flow curve and strength requirements.
Dolomite is produced by processing in-house mining dumps. This allows for the complete utilization of mined rock and reduces the environmental footprint.
Photo: Vasiliy Maksimov
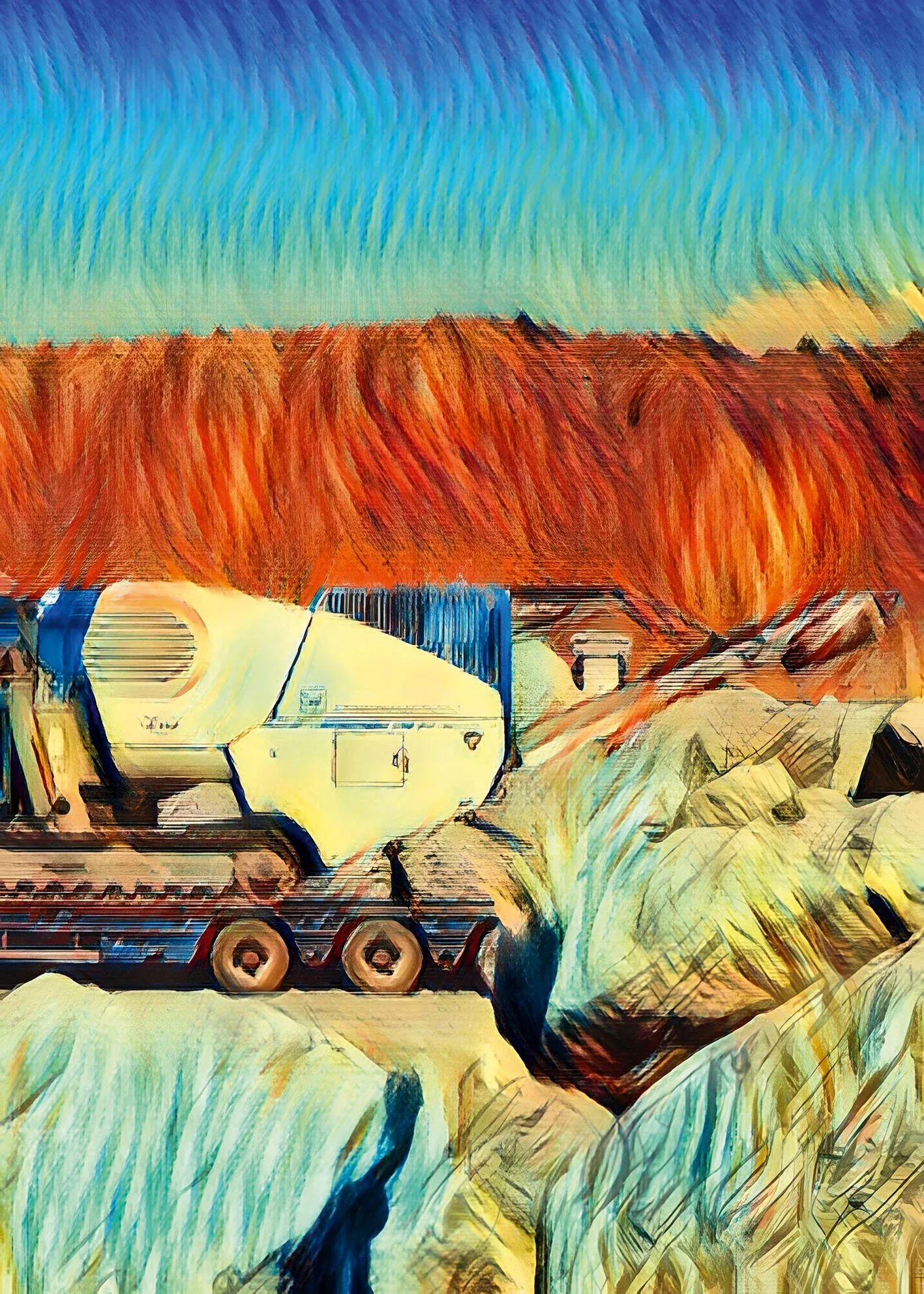
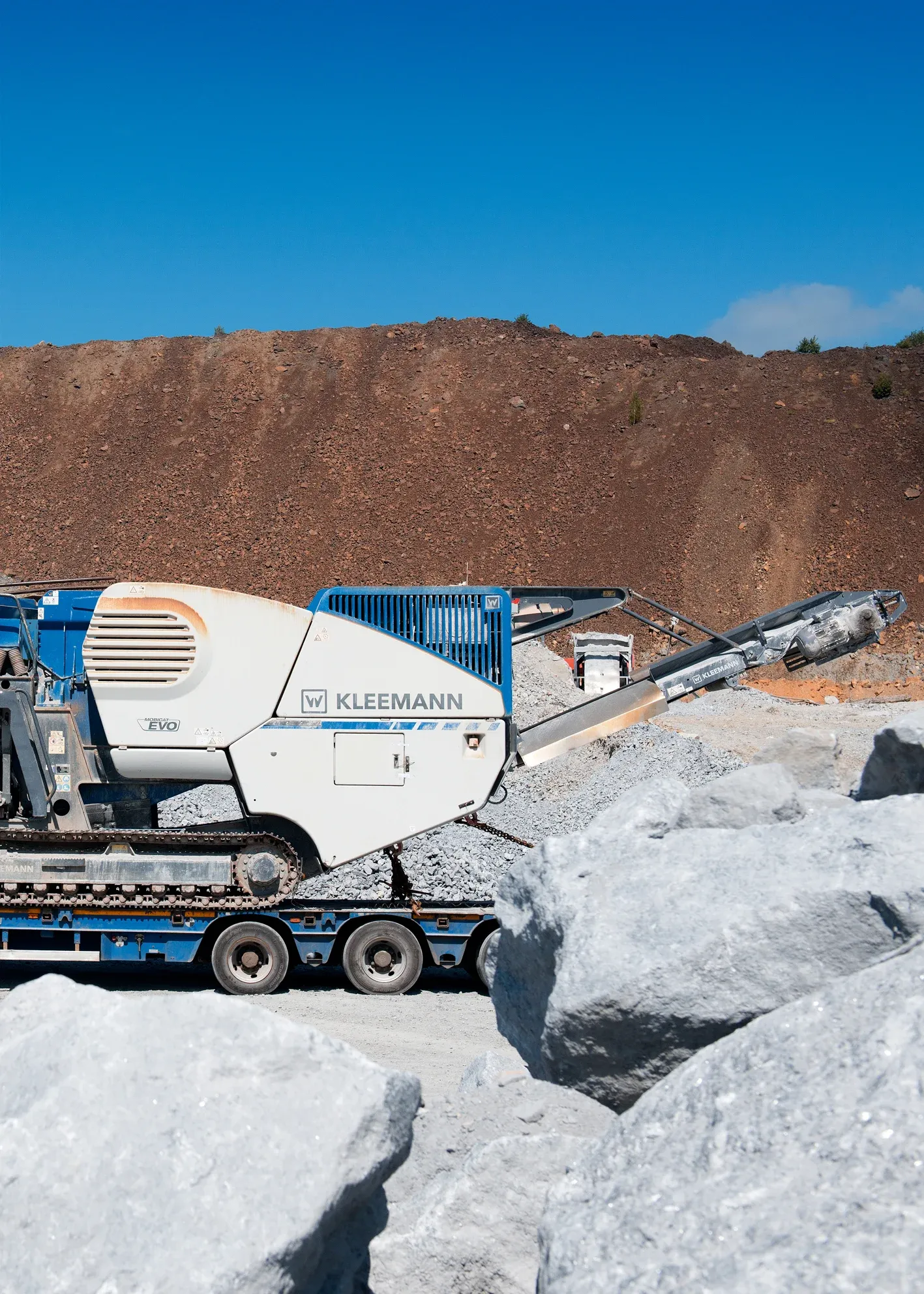
Semimobile crushing and sorting facility
A mobile jaw breaker in transportable mode. Crushing area
This facility is used both for mineral processing and crushing of high-quality magnesite to the target fraction (as required for subsequent decarbonization), bypassing the existing stationary facilities. This helps significantly reduce logistics costs and boost production efficiency.
The main advantage of the facility is its mobility. It can be relocated and quickly put to use wherever the production site is. All the equipment has been selected to operate in severe, extremely continental climate.
Photo: Dima Galanternik / Artoniсa
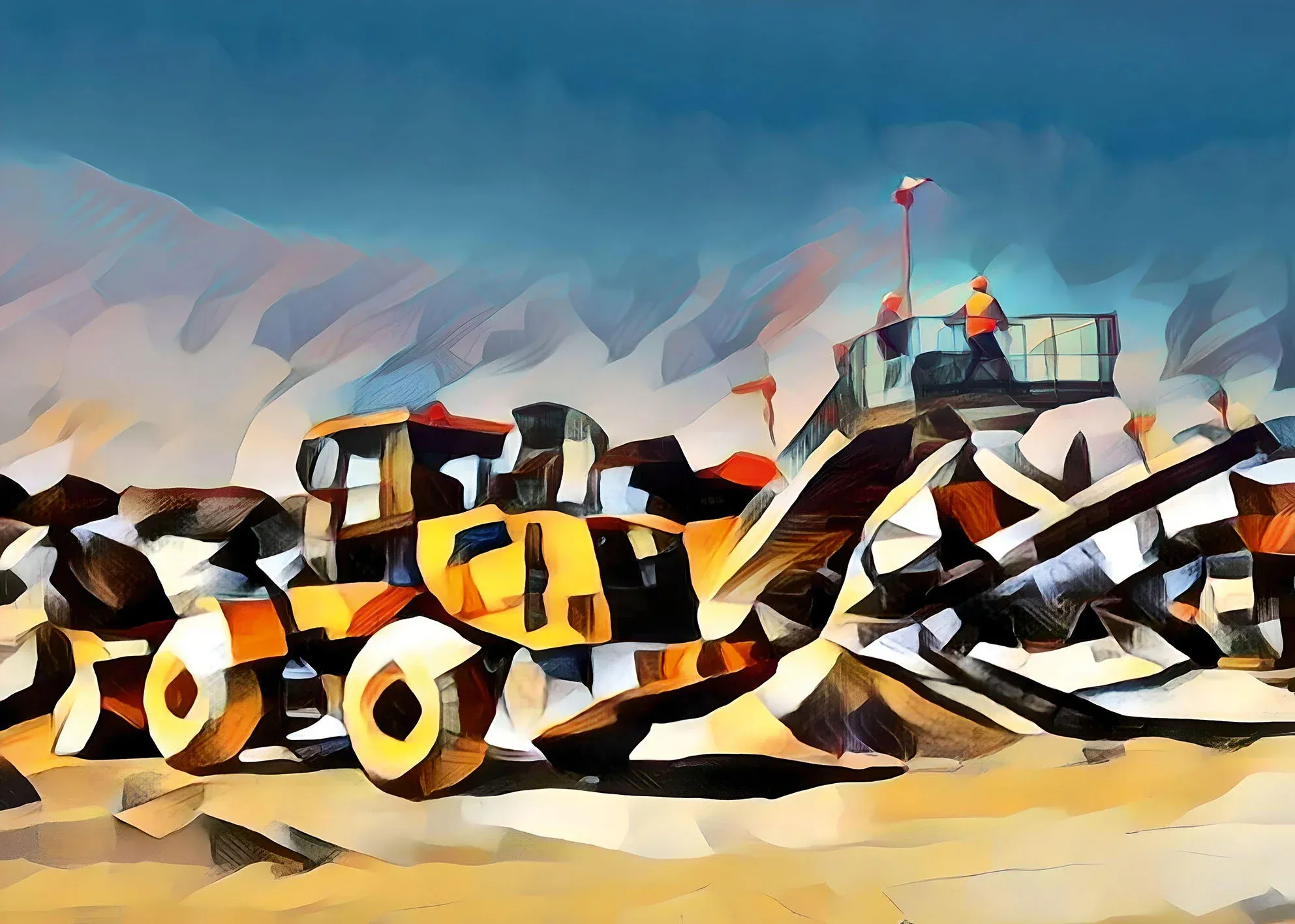
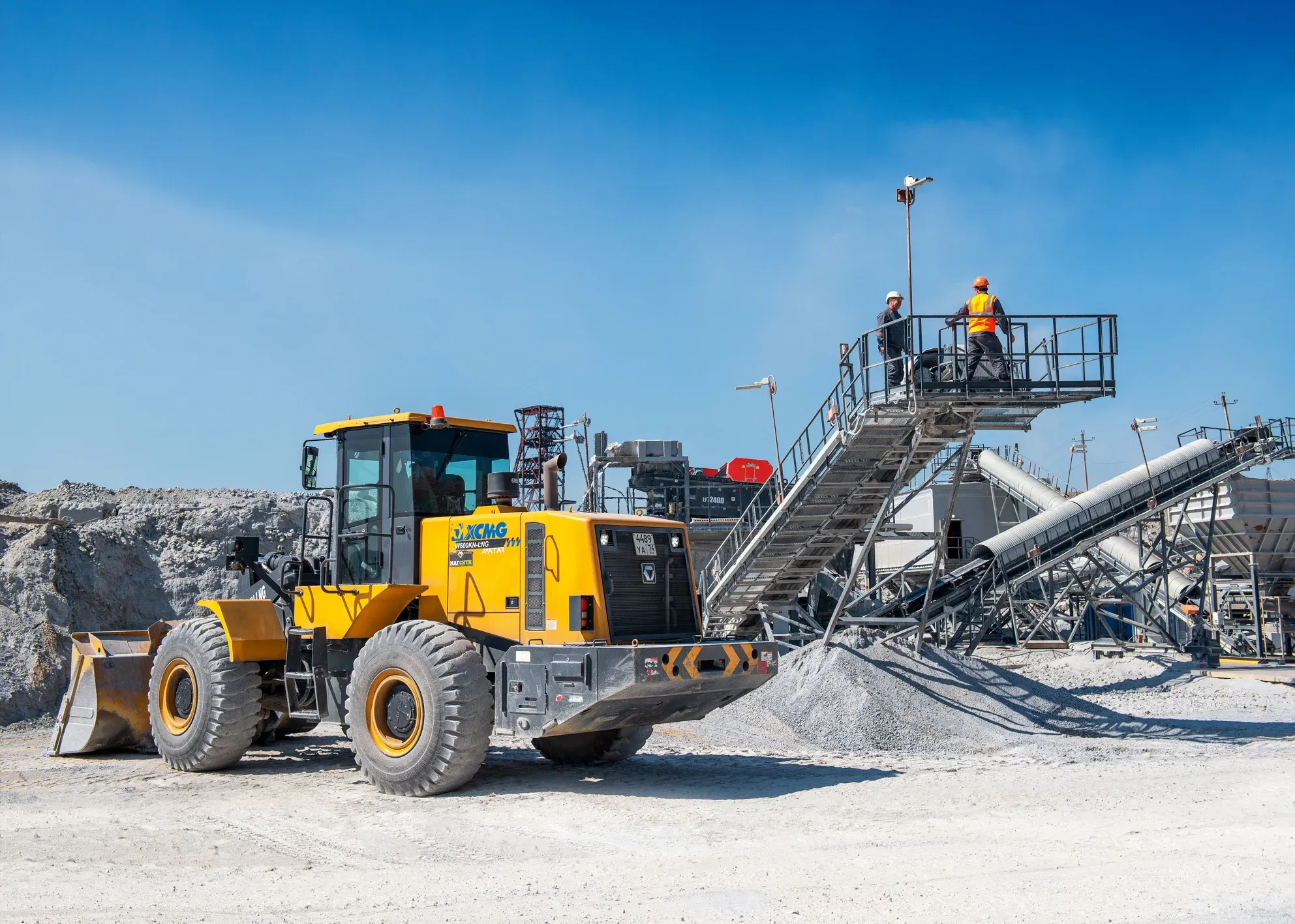
Semimobile crushing and sorting facility
Crushing and sorting area
The facility has multiple crushing plants, a screening system, and an X-ray transmission sorting system.
The X-ray transmission sorting system operates on a principle that materials can absorb X-ray radiation, which is measured using special detectors. The separation occurs based on difference in radiation intensity.
The complex produces raw magnesite with a fraction size of 40–0 mm or 25–0 mm, which is then moved to the main process area for decarbonization.
Thanks to the innovative sorting technology and mobility of the facility, it is now possible to completely recycle dumps of substandard raw material, prepare the disturbed land for reclamation, and overall, reduce the negative impact on the environment.
Photo: Dima Galanternik / Artoniсa
generations of ideas
Мagnezit Group’s state-of-the-art refractory production is a myriad of big and small journeys from idea to implementation completed by several generations of people. Each of them made the achievements we have today possible. Perhaps, tomorrow the abundant collective intelligence of Magnezit Group will expand even more with the elements of artificial intelligence. But regardless of this, we will stay true to our commitment of making an impact on the future and realizing our responsibility for it.
patents granted for technical and process solutions
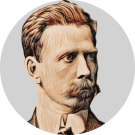
Vladimir Rogozhnikov
Manager of Magnezit Plant
-
Method for producing chrome-magnesia bricks
1914
Vladimir Rogozhnikov
Manager of Magnezit Plant
1914Method for producing chrome-magnesia bricks
Born in 1869 in Zlatoust (according to other sources — in Nizhny Tagil), Vladimir Rogozhnikov studied at the Ural School of Mines, Yekaterinburg. He worked as a lathe operator, junior foreman, mining technician, and rolling mill foreman at Zlatoust Steel Mill. He was one of the leaders of a social democratic labor group. In 1900, he was appointed as manager of Magnezit Plant, where he oversaw mining, construction, and equipment. In the 1920s, he was appointed as the plant’s technical superintendent. Starting from 1928, he served in the capacity of consulting engineer at Uralmet in Sverdlovsk.
Refractory bricks made of fused magnesia were very resistant to high temperatures, but had one critical drawback — low resistance to sharp temperature fluctuations. They quickly deteriorated following rapid temperature changes in steel furnaces. Chrome-magnesia bricks proved to be more mechanically stable. Thanks to the research work done by Vladimir Rogozhnikov, Magnezit Plant was the first in the Russian Empire to launch production of this type of bricks in 1914. The bricks demonstrated high mechanical strength and resistance to slag action. Therefore, they were suitable for lining the walls of steel furnaces, including the areas in contact with metal and slag. Chrome-magnesia bricks were also lighter than regular chromite bricks and so resistant to high temperatures that they could be used in roof lining of open-hearth furnaces.
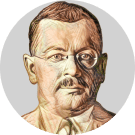
Zinoviy Tabakov
Director of Magnezit Plant
-
Method for producing magnesite bricks
1935
Zinoviy Tabakov
Director of Magnezit Plant
1935Method for producing magnesite bricks
Born on July 15 (28), 1895, in Kyiv, Zinoviy Tabakov studied at the Moscow Institute of Silicates and Construction Materials (today the Mendeleev University of Chemical Technology) and the Industrial Academy. In November 1931, he was appointed as head of Magnezit Plant, where he became the first executive with a higher vocational education. Under his leadership, the plant underwent fundamental technical upgrades, for which he was awarded the Order of Lenin in 1935. In October 1937, he was arrested under trumped-up charges of wrecking, sabotage, and terroristic setup. In 1938, he was sentenced to the maximum punishment. In 1956, he was rehabilitated.
For producing magnesia bricks, raw magnesite was burned at 1,600 °C to remove the carbon dioxide and dead-burn the magnesium oxide remaining after decarbonization with iron oxides, silica, etc. contained in the magnesite. The temperature was not enough for dead-burning all the calcium oxide in the raw material. Also, the burned material still had a certain amount of not dead-burned magnesia. These oxides can absorb moisture, with the particles expanding and forming hydrates. Expansion of the particles should be avoided once the product is set to shape. Therefore, the hydration phase should precede the forming. The process is quite slow and requires specific temperatures. The solution suggested by Zinoviy Tabakov was aimed at accelerating the hydration process to produce a more homogeneous mixture (in terms of hydration and moisture content), as well as to avoid powdered lime.
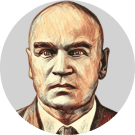
Aleksey Panarin
Chief Engineer of Magnezit Plant
-
Chrome-magnesia products for open-hearth furnace roofs
1941
Aleksey Panarin
Chief Engineer of Magnezit Plant
1941Chrome-magnesia products for open-hearth furnace roofs
Born on February 24 (March 9), 1905, in the village of Strelchataya Polyana, Yefremov District, Tula Governorate, Aleksey Panarin studied at the Bauman Moscow Higher Technical School. He started working at Magnezit in 1933 after receiving a placement at the plant. He worked as a technical supervisor of the caustic department, head of the magnesite powder shop and engineering department, and chief engineer. From 1946 to 1962, he served as director of the plant. It was under his leadership that the first stage of Magnesite’s New Plant was commissioned and construction of its second stage started. He was awarded the Stalin Prize (1943) and the State Prize (1950); and honored as a Hero of Socialist Labor (1958).
It was standard to use silica bricks in open-hearth furnace roofs, but they had many drawbacks, including high responsiveness to temperature fluctuations. When temperature changes, silica bricks start flaking. The start of commercial production of new magnesia-chrome bricks (following their development before the WWII) overseen by Aleksey Panarin was one of the most important milestones in the history of Magnezit. In 1941, the plant started making large-sized magnesia-chrome products for supporting suspended roofs in open-hearth furnaces. By the end of 1941, Magnitogorsk Iron and Steel Works used it as a basis for developing the world’s first armor steel smelting technology for heavy-duty open-hearth furnaces. Thanks to this technology, it became possible to fully supply the production of tanks in Chelyabinsk with armor steel.
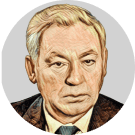
Nikolay Bugayov
Head of Magnezit Plant
-
Method for manufacturing plates for steel ladle slide gates
1973
Nikolay Bugayov
Head of Magnezit Plant
1973Method for manufacturing plates for steel ladle slide gates
Born on September 21, 1923, in the village of Markovo, Konstantinovsky District, Donetsk Region, Nikolay Bugayov finished the Artemovsk Ceramics and Mechanics Technical School in 1941. He fought on the Central, Bryansk, and first Ukrainian fronts, advancing into Germany. After graduating from the Kharkov Polytechnic Institute in 1955, he received a placement at Magnezit Plant. Under his leadership, the second stage of the New Plant was built and put into operation. He was awarded the Order of Lenin (1971), the Order of the Red Banner of Labor (1974), and the Order of the Badge of Honor (1958, 1966). He was also awarded Magnezit Group’s For Professionalism and Devotion to the Cause corporate prize in the Contribution to the Company’s Development category (2007).
With the development of the iron and steel industry, the locking gear used for steel casting was replaced with slide gates. In the USSR, the locking-free (slide gate) casting technology was first used in 1966 at Novolipetsk Steel. Slide gate kits for steel teeming ladles were supplied from Austria. They were very expensive: one set cost as much as a passenger car. Refractory engineers were tasked with replacing the Austrian products with domestic ones. The refractories were developed in collaboration with experts from the All-Union Institute of Refractories and Magnezit Plant. In 1973, the first refractories for slide gates were produced at Magnezit Plant and supplied to Novolipetsk Steel. In 1974, the products were supplied to West Siberian Metallurgical Plant and later to other iron-and-steel enterprises in the USSR.
- Gripping device for lifting and handling several unit loads at a time
- Slide gate plate
- Unshaped refractories
- Ladle slide gate plate
- Method for manufacturing a refractory tuyere (PDF)
- Firing method for complex shapes in a tunnel-type kiln
- Method for producing refractory powder from caustic magnesia powder
- Batch for producing magnesia-chromite refractories
- Method for producing magnesia
- Unshaped refractories
- Method of decarbonizing magnesia powder
- Method for producing magnesia
- Batch-type kiln
- Batch for producing basic refractories
- Method for producing magnesia
- Batch for producing basic refractories

Konstantin Simonov
Deputy Head of Central Laboratory at Magnezit Plant, Head of Research Department
-
Electric arc furnace for magnesia fusion
1982
Konstantin Simonov
Deputy Head of Central Laboratory at Magnezit Plant, Head of Research Department
1982Electric arc furnace for magnesia fusion
Born on June 11, 1931, in the village of Bykovo, Vagai District, Tyumen Region, Konstantin Simonov studied industrial engineering at the Kirov Ural Polytechnic Institute. In 1957, he enrolled to the Eastern Research and Design Institute of the Refractory Industry. Starting from 1966, he worked as deputy head of the plant’s central laboratory and also as head of the research department. During his time at the enterprise, he authored and co-authored more than 70 scientific papers and 52 patents. A candidate of engineering science, he was awarded one silver and three bronze VDNKh medals.
The aim of his invention is to increase the yield of fused material and decrease the specific consumption of raw materials and electricity by reducing the mass of the non-melting zone of blocks. As follows from the author’s proposal, this aim is achieved by designing a movable guard in the form of a truncated triangular pyramid in the electric arc furnace for the “to-block” magnesia fusion, where the side edges are curved along the arcs coinciding with equipotential lines surrounding the electrodes. The ratio of the radius of curvature of side edges to the electrode diameter is 1.4–2.2; and to the electrode pitch circle diameter, 0.5–1.2. The proposed technical solution reduces the specific consumption of raw materials and electricity and increases the yield of usable products, which corresponds to a 47–52 % increase in the machine’s performance.
- Method of decarbonizing magnesia powder
- Batch for producing magnesia-chromite bricks
- Electric arc furnace for magnesia fusion
- Batch for magnesia-chromite products Method for producing porous magnesia refractories
- Batch for castable refractory products
- Batch for producing unfired shaped refractories
- Batch for producing magnesia-spinel bricks
- Unshaped refractories
- Method for multi-row loading of liners for composite plates in slide gates (“annular loading”)
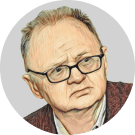
Andrey Luzin
Head of Thermal Engineering Laboratory at Magnezit Plant
-
Method for multi-row loading of liners for composite plates in slide gates
1984
Andrey Luzin
Head of Thermal Engineering Laboratory at Magnezit Plant
1984Method for multi-row loading of liners for composite plates in slide gates
Andrey Luzin was born on July 23, 1936, in Satka, Chelyabinsk Region. After graduating from the Satka Mining and Ceramics Technical School, he worked in the drying and kiln shop, the central laboratory’s research department, and as head of Magnezit Plant’s thermal engineering lab (from 1973 to 2000). From 1973 to 1987, he was a scientific secretary of the plant’s research and technology council. His titles and ranks: Inventor of the USSR (1990) and Honored Innovator of the Plant (2001). He was awarded the following medals: For Valiant Labor. In Commemoration of the 100th Anniversary of the Birth of V. I. Lenin (1971), and one silver (1980) and two bronze (1977, 1978) VDNKh medals.
His invention was designed for the refractory industry; specifically, the methods for loading liners of composite plates for slide gates. The aim of the invention is to reduce the reject rate during firing by creating an extended heat-exchange surface. The idea of the proposed loading method is to create an extended heat-exchange surface of the column where products are evenly washed over by the heat carrier when heated and by the cooling air when cooled. This makes it possible to reduce the thermal stress that causes crack defects and ensure the completion of the oxidation process for the organic temporary binders, consequently reducing the amount of defects due to underfiring (spots). The loading method helps reduce the rejection rate when firing liners by 75–84 % and stabilize the properties of the fired products.
- Method for producing light-burned magnesia-based bricks
- Mine water-removal unit
- Method for producing dead-burned magnesia-based refractories
- Magnesia-carbon refractories
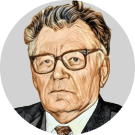
Evgeniy Mezentsev
Head of Engineering Department at Magnezit Plant
-
Method for producing unfired magnesia-carbon refractories
1986
Evgeniy Mezentsev
Head of Engineering Department at Magnezit Plant
1986Method for producing unfired magnesia-carbon refractories
Evgeniy Mezentsev was born on December 2, 1932, in the village of Bagaryak, Kamensk District, Ural Region. After graduating from the Kirov Ural Polytechnic Institute (where he studied metallurgical engineering) in 1955, he received a placement at Magnezit Plant. He worked his way up from a foreman to the chief engineer. He is the author and co-author of 26 patents. He was awarded the order of the Badge of Honor (1971), the order of the Red Banner of Labor (1986), and a VDNKh gold medal (1978). He is an Honored Innovator of Magnezit Plant (2001). He was awarded Magnezit Group’s For Professionalism and Devotion to the Cause corporate prize in the Contribution to the Company’s Development category (2006).
His invention was designed for the refractory industry; specifically, for manufacturing refractories used for lining steelmaking converters. The aim of the invention is to increase the strength of refractory products. According to the author’s idea, components of the mass are mixed at 25–60 °C. Their heat treatment is carried out with a heating rate of 3–15 °C per hour, holding at temperatures of 70–90 °C and 220–250 °C for 1–4 hours. Compressive strength ranges from 75.5 to 84.3 MPa, while bending strength is between 30.1 and 37.3 MPa (room temperature) and 21–25.6 MPa (at 1,500 °C). This manufacturing method delivers more durable magnesia-carbon bricks, increasing their resistance to mechanical erosive wear when used for lining steelmaking vessels.
- Method for producing unfired magnesia-carbon refractories
- Batch for production of magnesia-carbon refractories
- Method for producing fused magnesia-containing materials
- Batch for manufacturing magnesia-chromite refractories
- Method for producing unfired magnesia-carbon refractories
- Batch for production of magnesia-carbon refractories
- Batch for production of unfired magnesia-carbon refractories (PUE)
- Refractory material for production and maintenance of refractory lining in steelmaking furnaces
- Refractory batch for production of magnesia-carbon refractories
- Method for producing magnesia-chrome-containing material
- Method for producing fused magnesia-containing materials
- Refractory batch (SPKhT, MMShP, PPKhT, PPKhT‑1)
- Method for producing magnesia-carbon refractory
- Refractory batch for lining heat-treatment units
- Unfired magnesia refractory
- Batch for manufacturing refractories and linings (PGRBS‑90f)
- Method for producing magnesia-containing bricks
- Unshaped refractories
- Magnesia-carbon refractory (PUSKb, PUPEb)
- Method for producing magnesia-containing materials
- Magnesia refractory
- Unshaped refractories
- Method for producing fused refractory materials (rotary bath)
- Batch for xylolite production
- Single line-to-ground fault protection device in an isolated neutral system
- Tuyere for bottom blowing of molten metal and the method for its production
- Refractory material for production and maintenance of hearths in steelmaking furnaces (PPE‑88-1)
- Batch for producing magnesia-spinel refractories
- Batch for production of structural materials
- Rotary kiln lining
- Unshaped refractories
- Batch for production of clinker bricks
- Batch for producing low-silicon magnesia-spinel refractories
- Slide gate plate
- Magnesia binder
- Acoustical-electrical transducer
- Device for manufacturing thermoplastic bags
- Metal detector
- Carbon refractory (ShPUP)
- Method for producing magnesia-containing powders
- Transfer and sorting depot
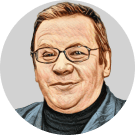
Viktor Koptelov
Deputy Head of Central Laboratory at Magnezit Plant
-
Method for producing fused magnesia powders
1993
Viktor Koptelov
Deputy Head of Central Laboratory at Magnezit Plant
1993Method for producing fused magnesia powders
Viktor Koptelov was born on August 5, 1946, in Satka, Chelyabinsk Region. After graduating from the Leningrad Technological Institute named after Lensovet, where he studied chemical technology, he worked his way up from an ordinary engineer to the head of the powder group at Magnezit’s central laboratory. For many years, he oversaw the plant’s process development department. He is the co-author of 78 inventions and holder of 7 patents. He was awarded two VDNKh bronze medals. He is an Honored Inventor of the Russian Federation (2001). He was also awarded Magnezit Group’s For Professionalism and Devotion to the Cause corporate prize in the Science and New Technologies category (2007).
The aim of his invention is to increase the density of fused magnesia powder by improving the fusion and grain size of the semi-finished light-burned magnesia, as well as to increase the yield of the semi-product and fused magnesia powder with an MgO content of over 91 % by means of thermal beneficiation with reduced energy consumption and by increasing the yield of fused magnesia powder granules. The raw material is decarbonized at 600–1,000 °C. The resulting product is cooled at a rate of 50–60 °C per minute, simultaneously causing its disintegration, and is fractured to isolate small-sized light-burned magnesia granules by classification. It is then fused at a rate of 20–50 °C per minute. Raw magnesite or brucite can be used as the raw material.
- Device for measuring ohmic resistance of live electrical circuits
- Device for bottom blowing of metal
- Method for producing basic refractories
- Method for producing magnesia powders (double-burned), Carbon refractory, PUSK (PU‑92-10-K, PU‑92-10)
- Single line-to-ground fault protection device in an isolated neutral system
- Method for producing magnesia-containing powders for refractories and a process line for its implementation
- Method for determining a given size fraction of lump material in a process flow
- Refractory binder for lining high-temperature heat-treatment units
- Method for open-pit mining
- Batch for producing castables and shaped refractories for structurally stable linings (PShPTs)
- Magud ameliorant fertilizer
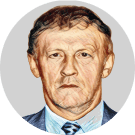
Evgeniy Krokhin
Head of Design Bureau at Magnezit Plant
-
Method for producing magnesia-containing powders for refractories and its production line
1996
Evgeniy Krokhin
Head of Design Bureau at Magnezit Plant
1996Method for producing magnesia-containing powders for refractories and its production line
Evgeniy Krokhin was born on June 2, 1948, in Kyshtym, Chelyabinsk Region. After graduating from the Chelyabinsk Polytechnic Institute, where he studied mechanical engineering, he worked as a design engineer at Kurgan Wheel Tractor Plant. In 1978, he was appointed as head of the design bureau for automation and mechanization at Magnezit’s central laboratory. He oversaw the design bureau until 2008. He was awarded the badge of the All-Union Central Council of Trade Unions For Active Work in Mechanizing Manual Labor (1982) and holds the titles of Honored Innovator of Magnezit Plant (2005), Professional Engineer of Russia (2005), and Honored Designer of the Russian Federation (2012).
The aim of his invention is to improve the efficiency of high-additive magnesite beneficiation and the quality of magnesia-containing powders used for producing refractories, while simplifying the technological process, allowing for an increase in the line’s productivity to up to 15 tonnes per hour. The effect is achieved by significantly increasing the width of the spread of dispersed grains when beneficiating the granular fractions of magnesia-containing powder. This is done by creating almost identical conditions for their charging and discharging by dedusting and heating the powder, and uniformly distributing the grains across the flow down to the size of a single grain. It is also the result of an intensified grain charging process in a uniform electric field of a corona discharge.
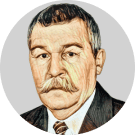
Vladimir Velikiy
Head of Central Laboratory for Automation and Mechanization, Magnezit Plant
-
Process line for preparing a multi-component mixture for production of refractories
1997
Vladimir Velikiy
Head of Central Laboratory for Automation and Mechanization, Magnezit Plant
1997Process line for preparing a multi-component mixture for production of refractories
Vladimir Velikiy was born on June 1, 1947, in the village of Solomensky, Stepnovsky District, Stavropol Territory. After graduating from the Chelyabinsk Industrial and Teacher Training College as a mechanical technician, he began working at Magnezit Plant as a technician in 1971, and moved his way up to the head of the mechanical installation section of the central laboratory for automation and mechanization, and then the head of the laboratory itself. He is the co-author of 7 patents and 113 streamlining proposals. He was awarded a bronze VDNKh medal For Achievements in the Development of the USSR National Economy (1981) and the badge of the Soviet Ministry of the Iron and Steel Industry For Mechanization and Automation in Metallurgy (1990). He is an Honored Innovator of the Russian Federation (2010).
His invention aims at simplifying the design of the production line and preparing a multi-component mixture from heterogeneous ingoing materials. The line helps to increase productivity by combining two processes, the loading of soft containers into a hopper and the installing of a sealed lid, as well as by reducing the time for supplying liquid binder by displacing it with compressed air; another improvement is the higher quality of the prepared refractory mixture due to separating and removing the chemically pelletized fragments of the powdered phenolic binder while simultaneously preventing the release of harmful substances along the entire process train — from loading to mixing — and rationing the measured liquid binder.
- Method for open-pit mining
- Rotary kiln lining
- Installation for side tipping of mine trolleys with hinged sides
- Batch for production of magnesia-spinel refractories MPShPlI
- Process line for preparing a multi-component batch for refractories (SFP)
- Spinel-magnesia-carbon refractory
- Spinel-magnesia-carbon refractory
- Method for controlling the light-burning of raw material in a rotary kiln
- Device for pressing powder materials
- Method for preparation of a carbon-containing batch for pressing dense shaped refractories
- Device for emergency shutdown of the electric drive of a cableway
- Cableway
- Aerostatic cable hoisting machine
- Rotary kiln
- Multichannel strain-gauge
- Device for monitoring the level of dielectric granular material
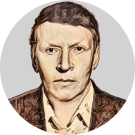
Germogen Chelpanov
Senior Engineer for Commissioning and Testing at Central Laboratory for Automation and Mechanization, Magnezit Plant
-
Multichannel strain-gauge
1998
Germogen Chelpanov
Senior Engineer for Commissioning and Testing at Central Laboratory for Automation and Mechanization, Magnezit Plant
1998Multichannel strain-gauge
Germogen Chelpanov was born on January 1, 1937, in Satka, Chelyabinsk Region. After graduating from the Satka Mining and Ceramics Technical School as an electrical technician and the Magnitogorsk Institute of Mining and Metallurgy as an electrical engineer, he started working at Magnezit Plant as an electrician in 1958 and then worked his way up from power electrical engineer, area supervisor at the instrumentation and automation workshop, and senior commissioning and testing engineer to deputy head of the laboratory for automated control of electric drives at the central laboratory for automation and mechanization. He is the co-author of two patents and 108 streamlining proposals. He is an Honored Innovator of the Russian Federation (1999).
His invention deals with automation of the material weighing, dosing, and testing processes. The technical result of the invention is simplification of the circuit, increased measurement accuracy, and noise immunity of the device. The use of the proposed design for the multi-channel strain-gauge allows (as compared to other known designs of the same device) a significant increase in the signal-to-noise ratio by increasing the supply voltage of strain-gauges and reducing the voltage amplifier gain. In addition, the simpler design proposed by the invention results in an increased measurement accuracy and resolution achieved by reducing the noise level and eliminating zero drift due to inclusion of decoupling capacitors.
- Shaft heat exchanger for a rotary kiln
- Method for producing silicon-carbide electric heaters using black silicon carbide
- Vibrating feeder
- Continuous-weighing scale
- Machine for working flat surfaces of parts
- Lifting gear
- Technological briquette for the non-ferrous metallurgy and method for its production
- Method for firing highly-carbonated raw magnesite in a rotary kiln
- Conditioning agent for magnesia smelter slag and method for its production
- Discontinuous-weighing scale with a dead weight compensation device
- Spinel-containing carbonated refractory (PShU-75-5-K, PShU‑75-10-K)
- Rotary kiln lining
- Shaft heat exchanger of a rotary kiln
- Method for producing high-duty carbon-containing refractory (PUPLb)
- Refractory mortar
- Comminution device
- Method for breaking up by explosives in the bottom hole of underground stopes
- Room-and-pillar underground mining method (shrinkage)
- Flux for the steel industry and method for its production
- Sinking method for room-and-pillar mining of ore deposits
- Ore drawing machine
- Method for transporting mined ore and means of its implementation
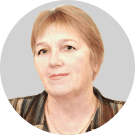
Raisa Polovinkina
Supervisor of Process Development Office, Engineering Department, Magnezit Group
-
Method for producing flux for the steel industry
2008
Raisa Polovinkina
Supervisor of Process Development Office, Engineering Department, Magnezit Group
2008Method for producing flux for the steel industry
Raisa Polovinkina was born on May 14, 1950, in the village of Stepanovka, Mariinsk District, Kemerovo Region. After graduating from the Tomsk Polytechnic Institute, where she studied process engineering for ceramics and refractories, she received a placement at Magnezit Plant and began working as a shift forewoman in the magnesia products workshop No. 2, later as an engineer in the research department of the plant’s central laboratory and as a senior engineer of the raw material and consumables processing study group. In 2006, she was awarded Magnezit Group’s For Professionalism and Devotion to the Cause corporate prize in the Science and New Technologies category. She is an Honored Inventor of the Russian Federation (2010).
The aim of her invention is to produce flux with an increased MgO content (that provides a sufficiently high rate of dissolution of the flux in slag during steel production) and an optimal particle size distribution, thus eliminating the need of additional crushing of large components of the burned product and screening of substandard breeze. The technical result of the invention is the production of flux in the form of biceramic granules with a specific gradient of chemical composition characterized by a non-uniform content of basic oxides in the shell and core of the granules, thus enabling a high rate of flux absorption by the melted slag in steelmaking and, thereby, ensuring better quality of skull coating of the converter lining.
- Flux for the steel industry
- Method for producing flux for the steel industry (Thermogran)
- Batch for manufacturing magnesia-spinel products
- Method for producing magnesia-spinel refractory batch for making shaped products
- Investment compound for filling the chimney of a steel teeming ladle
- Gunning refractory
- Method for steelmaking in an electric arc furnace
- Method for metallurgical dust recycling
- Batch for manufacturing magnesia-spinel refractories
- Roof lining in an open-hearth furnace
- Method for open-pit mining
- Suction sump (embodiments)
- Method for producing carbon-containing refractories and batch composition for them
- Mold block for producing lining using dry gunning masses
- Method for repairing the refractory lining of a degasser nozzle
- Method for producing magnesia conditioning agent
- Tundish ladle for continuous casting
- Tundish ladle for continuous casting
- Impact pot of a tundish ladle for continuous casting (straight)
- Impact pot of a tundish ladle for continuous casting (reducer)
- Batch composition for carbon-containing refractories and method for producing them
- Impact pot
- Batch composition for carbon-containing refractories and method for producing refractories
- Method for producing magnesia conditioning agent
- Water-cooled roof of an electric arc furnace
- Method for producing dolomite binder
- Protective hardening coating for refractory lining of thermal generating units
- Mold block for producing refractories using dry investment compound
- Method for steel production in an electric arc furnace
- Impact pot
- Shaped refractory for lining the top ring of a steel-pouring ladle
- Crucible
- Tundish ladle for continuous casting
- Crucible for a tundish
- Method for 3D printing refractories
- Method for processing steel in tundishes
- Refractory product for lining high-temperature machines
- Refractory product for the central part of an electric arc furnace
- Metallurgical flux and method for its production
- Crucible
- Tundish ladle for continuous casting
- Batch for producing forsterite-bonded refractories
- Batch for producing aluminum-ferrous spinel and a refractory product based on aluminum-ferrous spinel
- Refractory concrete composition
- Refractory block for a gas-distribution core (top)
- Refractory block for a gas-distribution core (bottom)
- Method for 3D printing products
- Method for producing magnesia bricks
- Composition for producing lightweight refractory
- Composition for producing magnesia-spinel refractories
- Refractory castable
- Dry gunning masses
- Method for thermomechanical beneficiation of magnesite in indirect-heating furnaces
- Magnesia-spinel refractory
- Refractory cooling panel
- Refractory product and a method for its production
- Composition for producing magnesia-spinel refractories
- Recycling method for metallurgy
- Chrome-magnesia refractory
- Chrome-magnesia refractory
- Batch for producing flux for the steel industry
- Batch for producing magnesia-spinel refractories
- Chrome-magnesia refractory
- Refractory makeup mass
- Method for monitoring the state of lining in heat-treatment units
game
who is
the author?
who is
the author?
Test your ability to distinguish between human speech and neural network output. Can you guess the author of each of the 10 statements?
collection of views
neural network as a co-author gallery
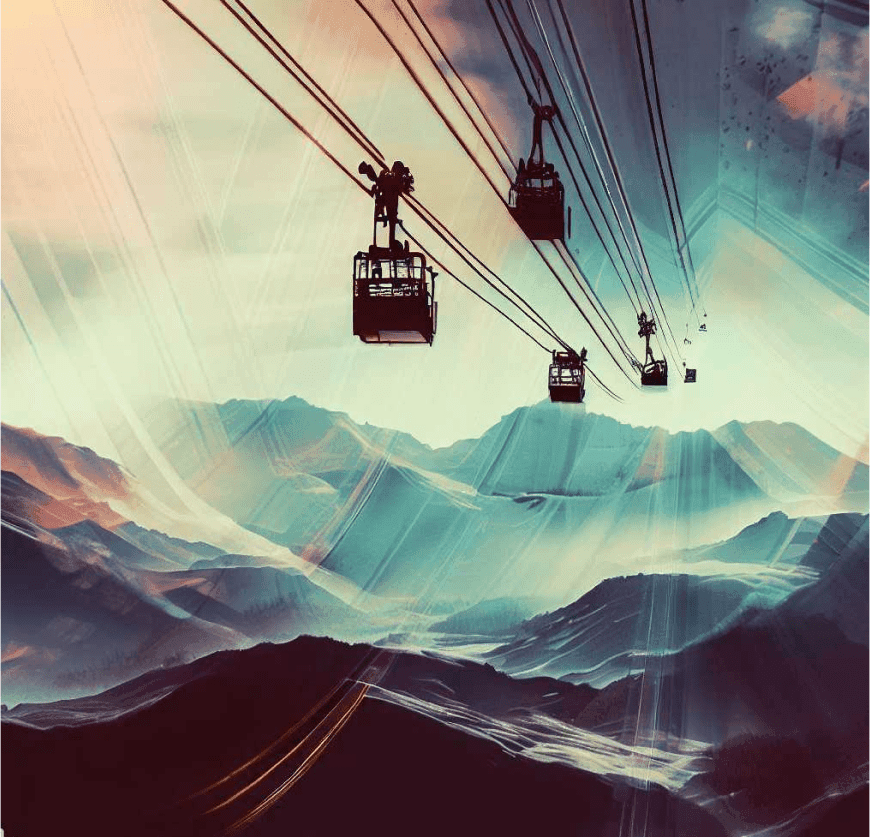
Yurij Zaripov. Heavenly way. 2023
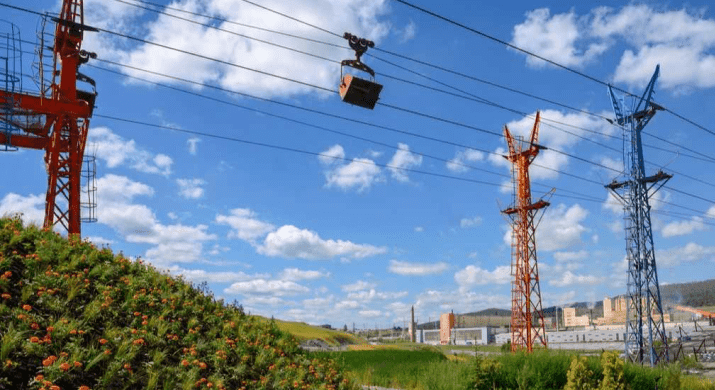
Original photo
Author's note
The process of generating photos is very exciting. You can use simple prompts to create almost any image. Even a person with no artistic or illustrator skills can do that. I chose a photo of a cable car line for the project, as it contains clear and expressive objects — cable cars. The neural network helped make this photo even more vivid and emotional and removed all the elements that I thought were unnecessary. When I saw the result, the name for the image popped up immediately.
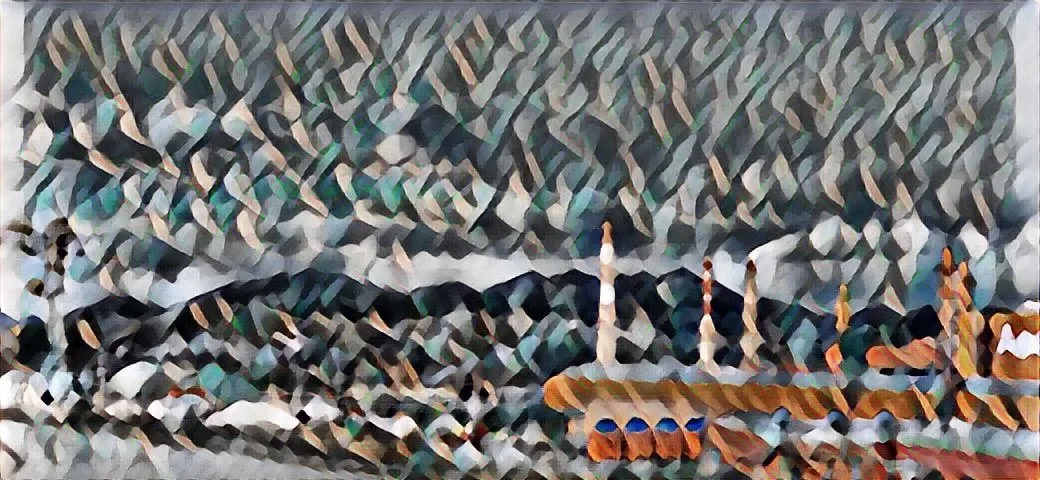
Alina Gumerova. Factory mosaic. 2023
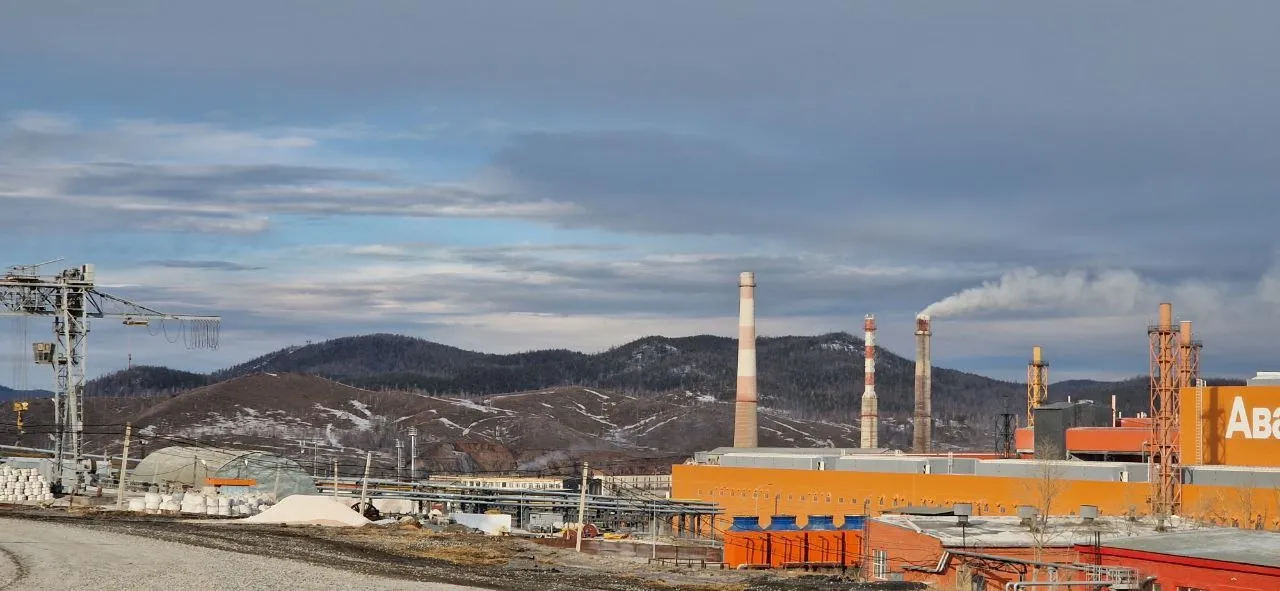
Original photo
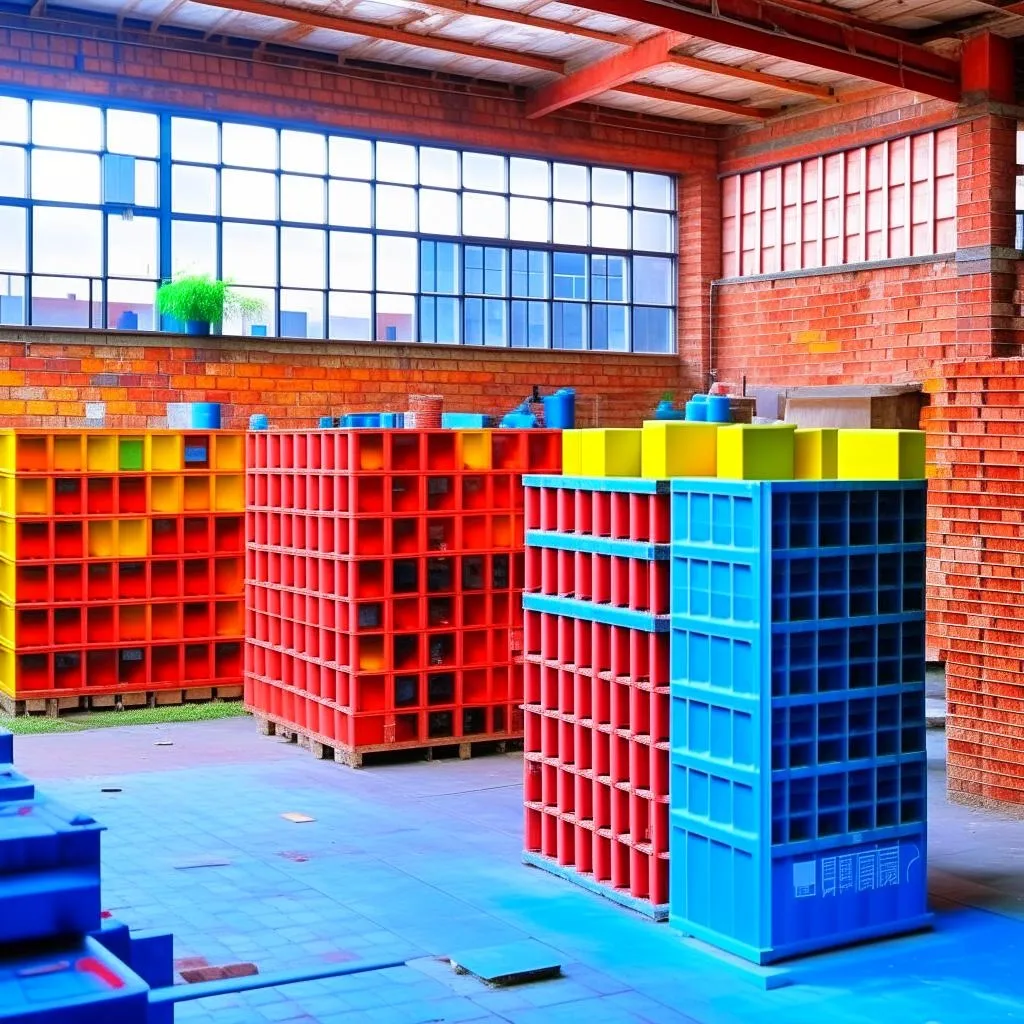
Liana Denislamova. Warehouse of finished products of magnesia products. 2023
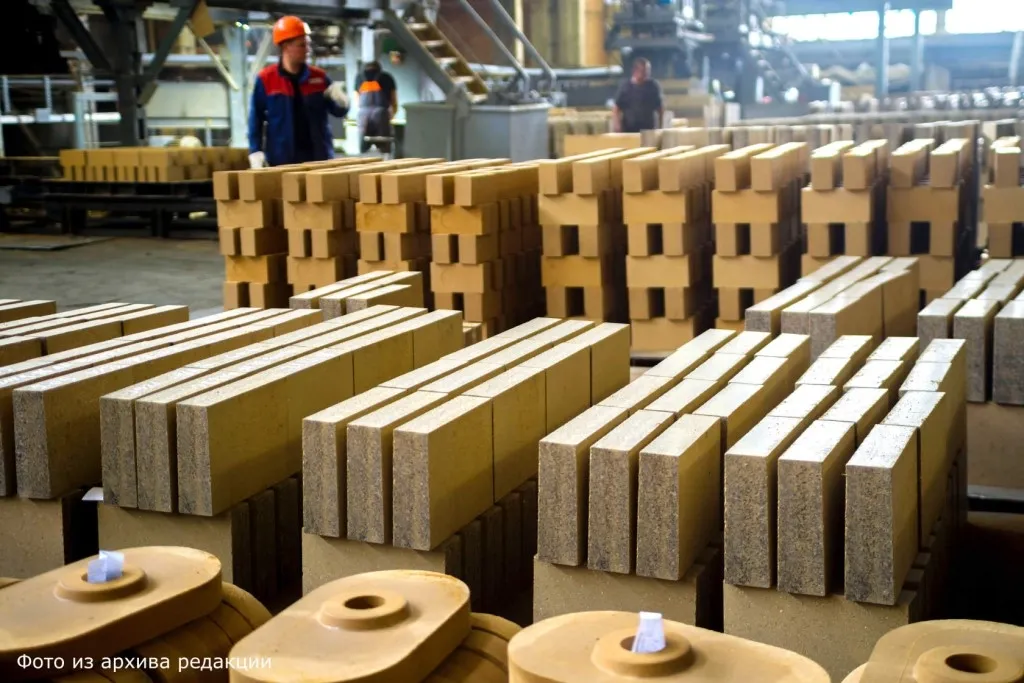
Original photo
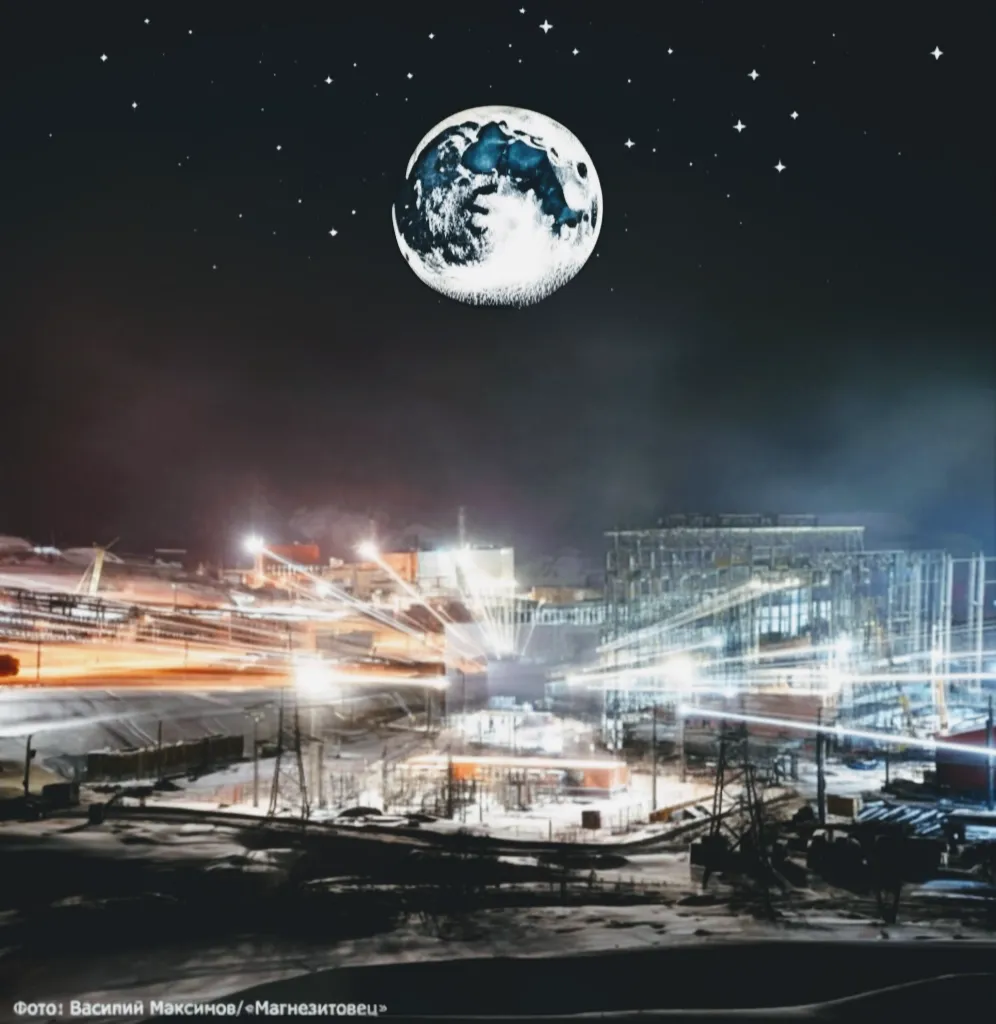
Nikita Filippov. Factory under the moon. 2023
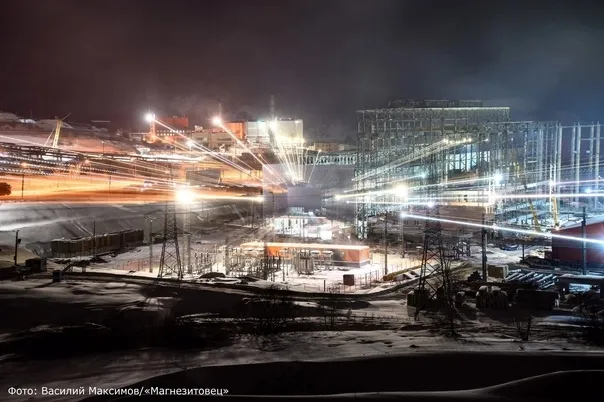
Original photo
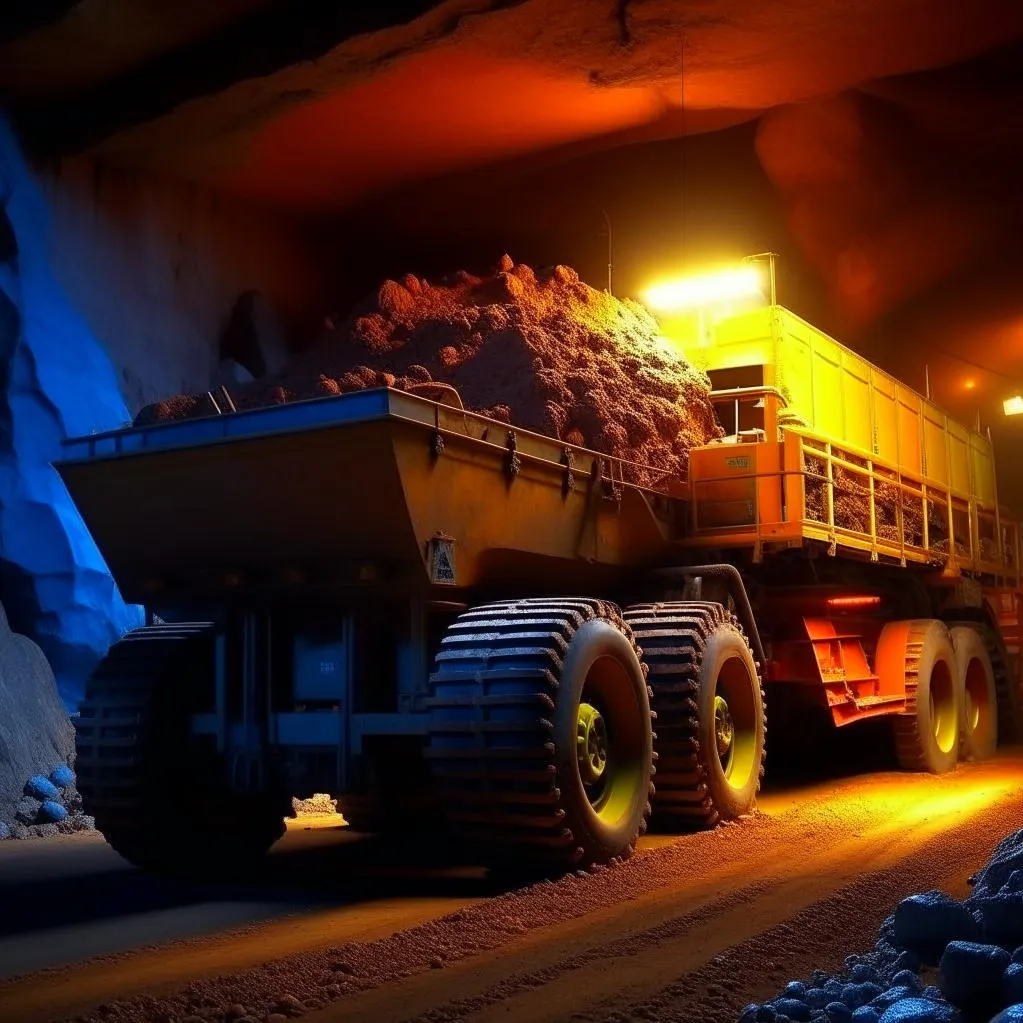
Mikhail Mikhailov. The magnesite mine. 2023
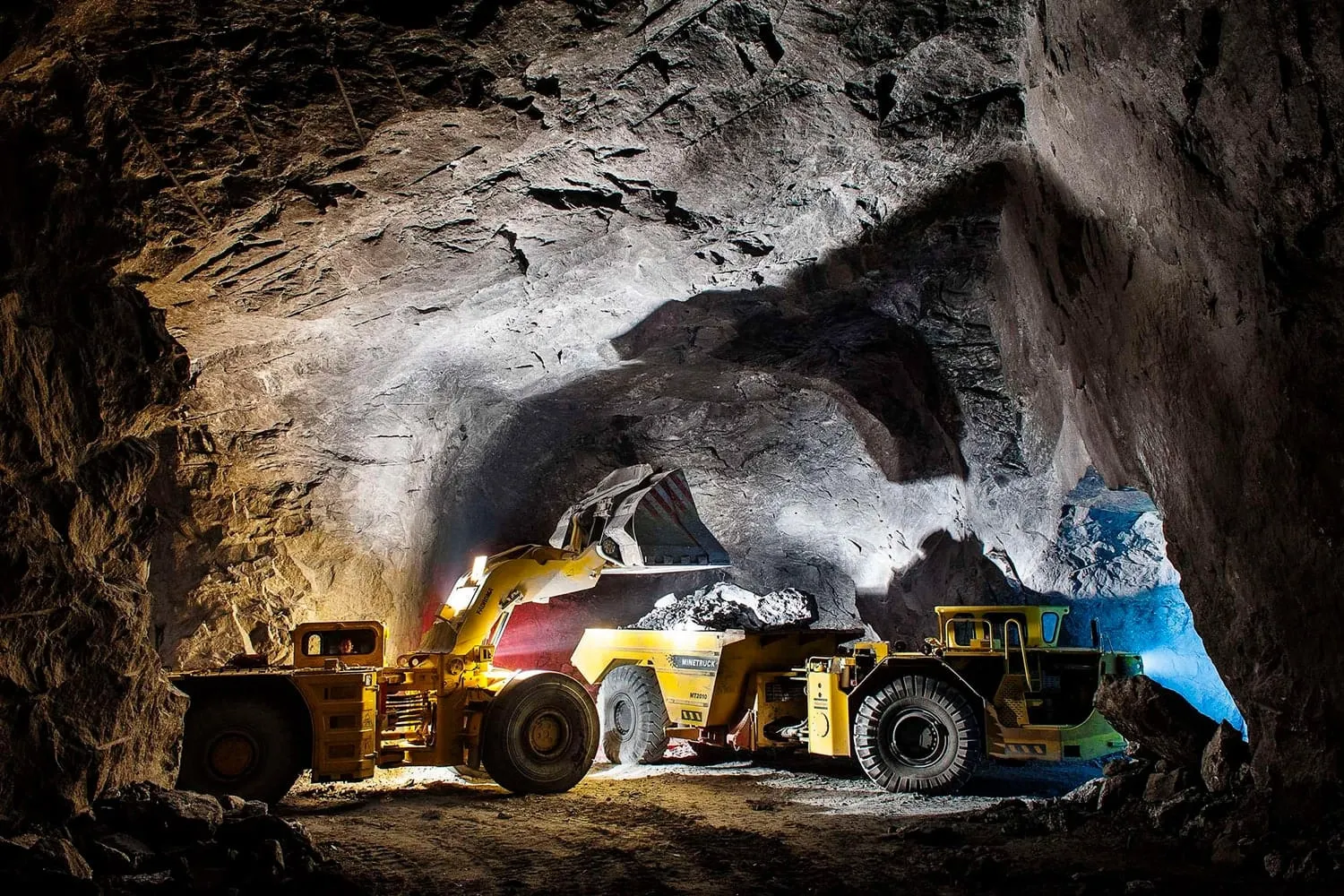
Original photo
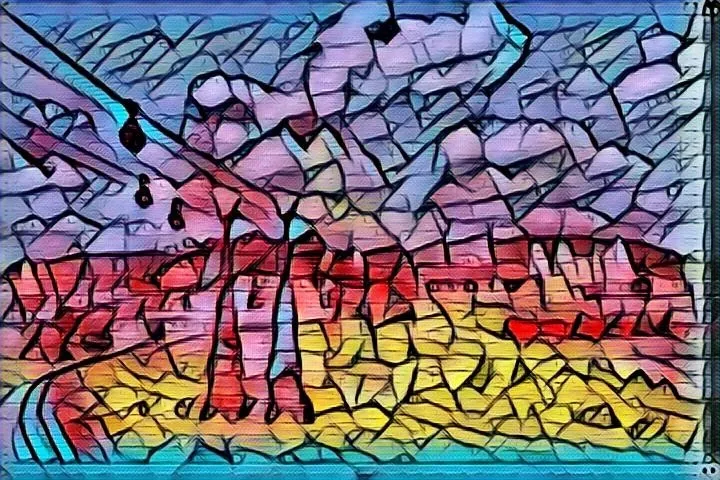
Diana Degtyareva. Industrial harmony. 2023
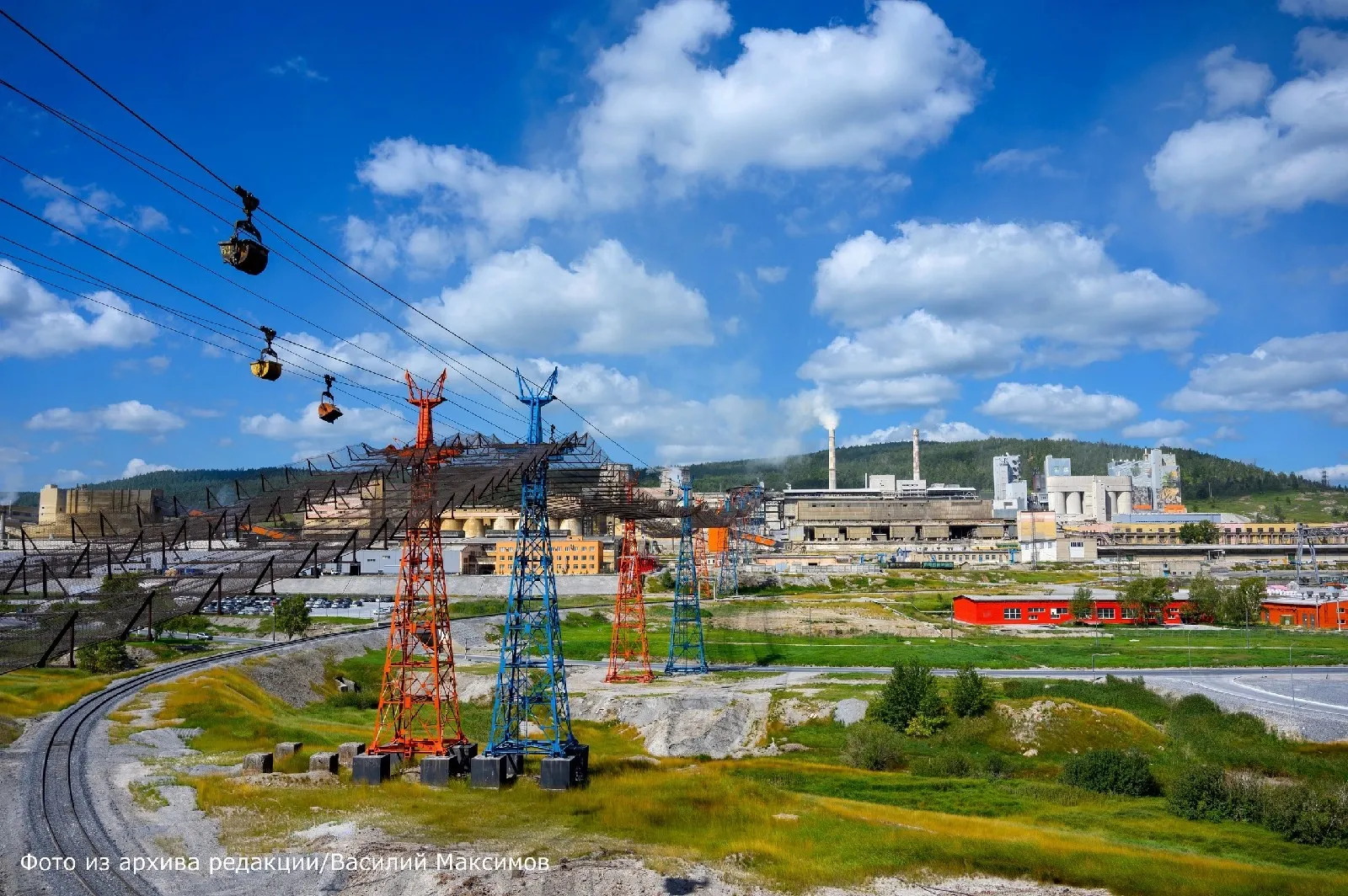
Original photo
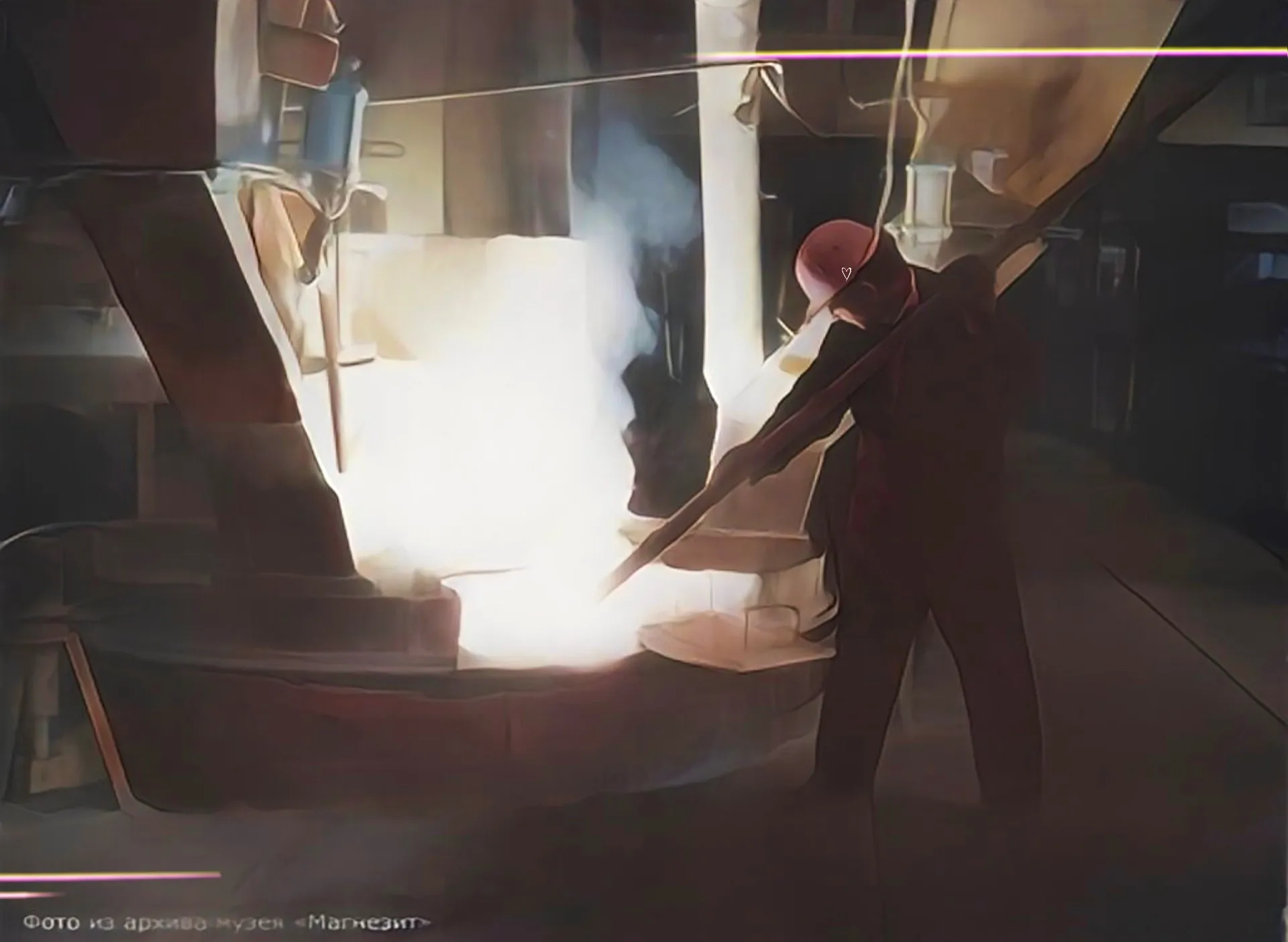
Daria Sagandykova. The metallurgist. 2023
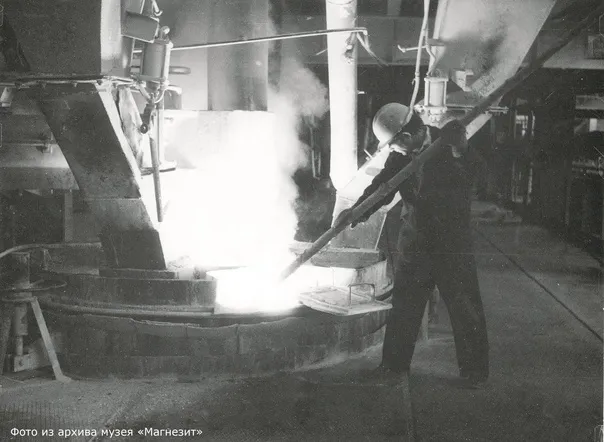
Original photo
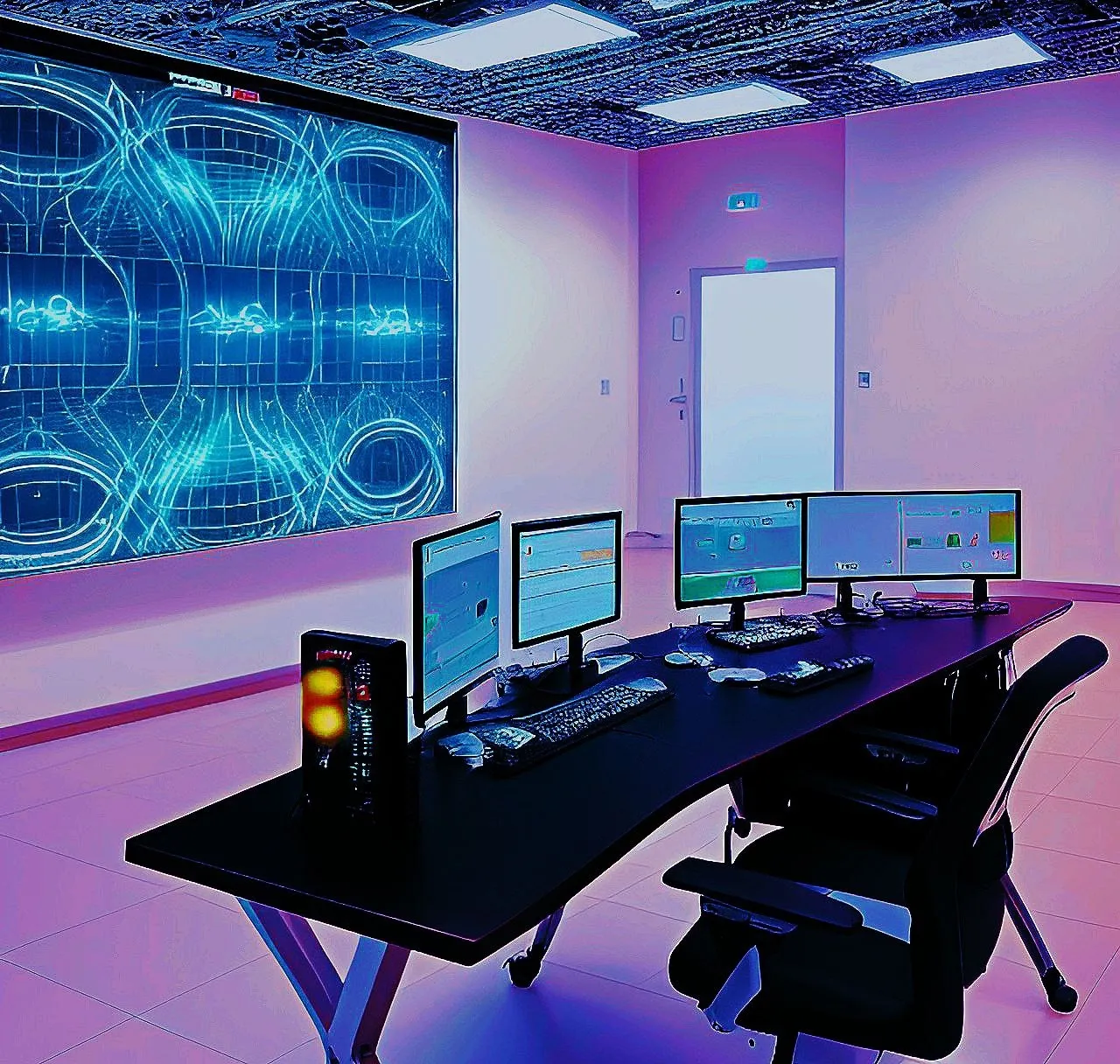
Grigory Tsepilov. Magnezit under observation. 2023
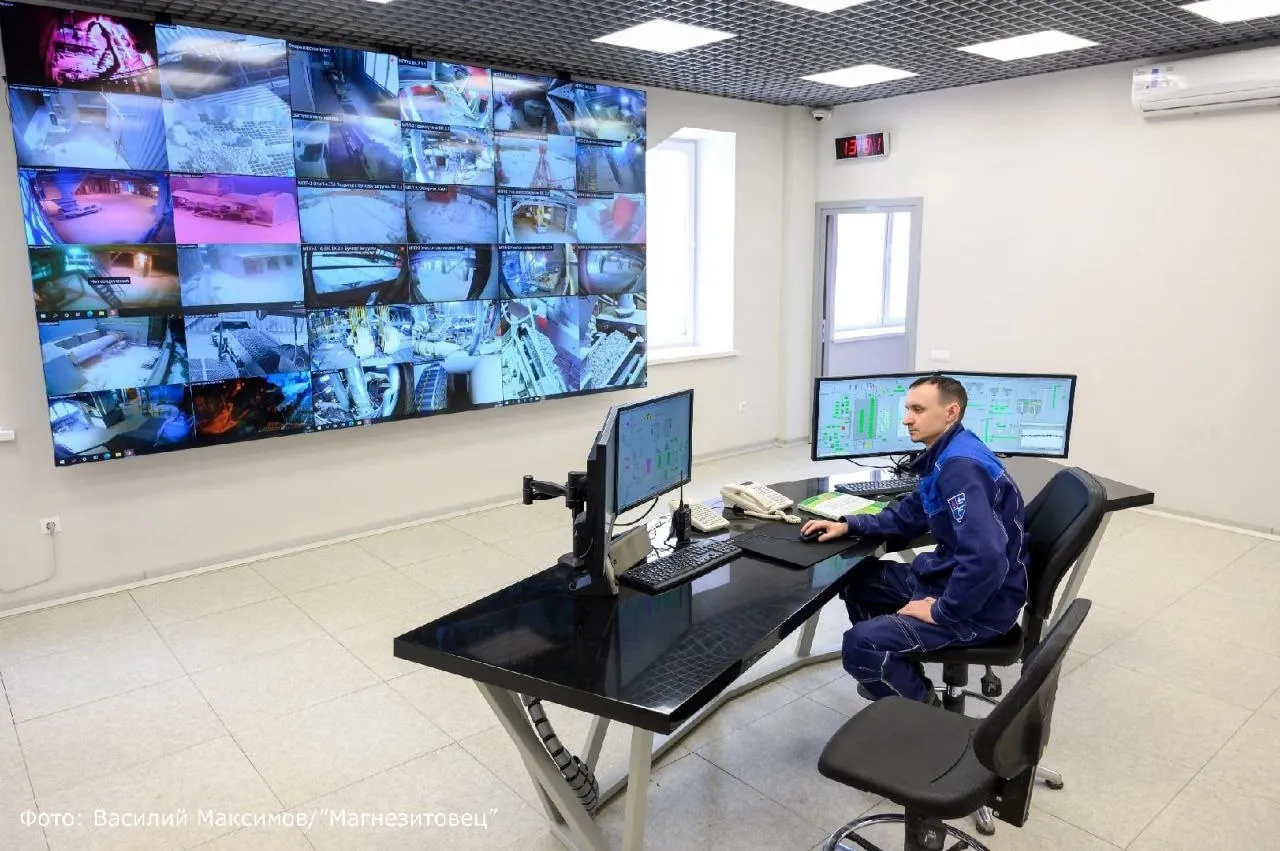
Original photo
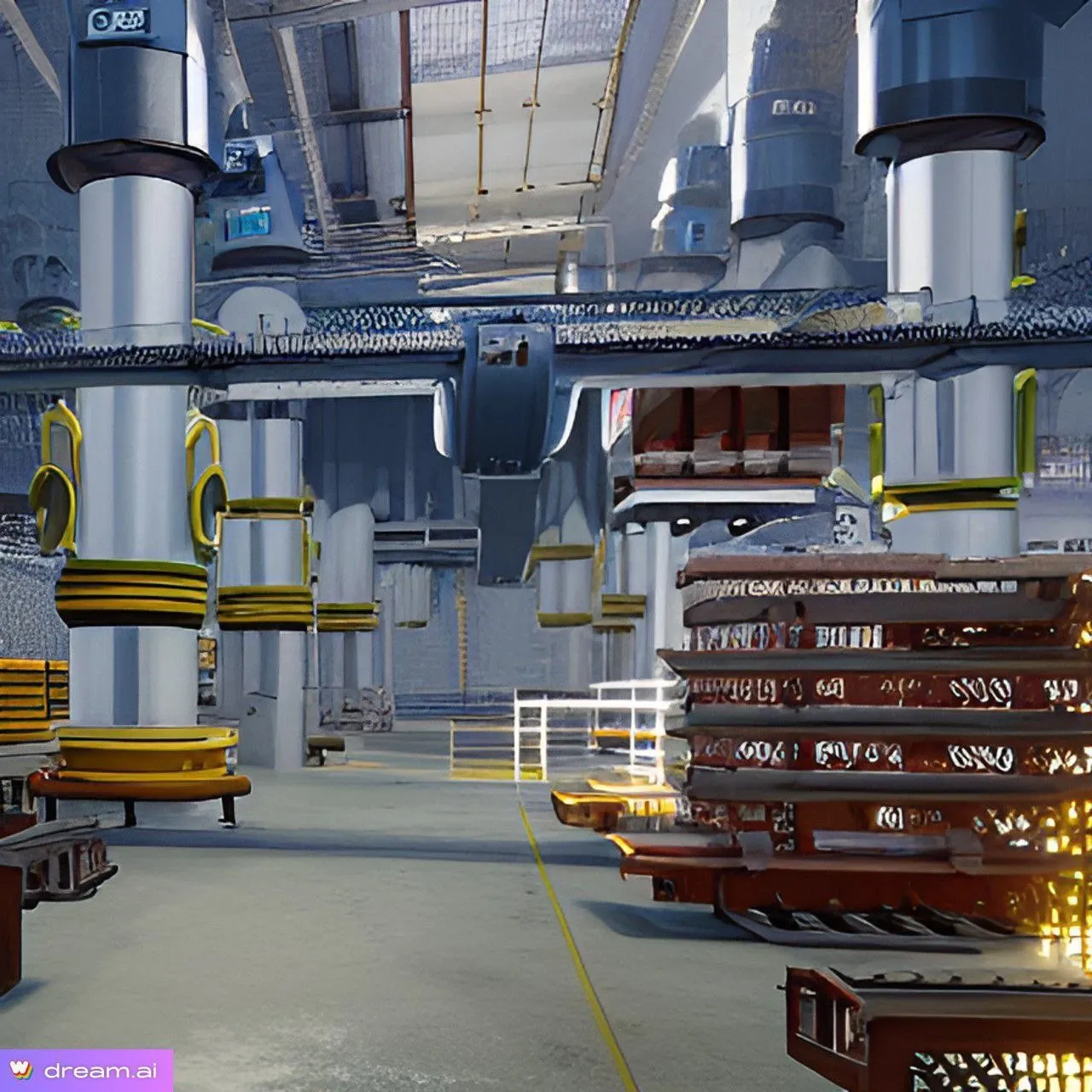
Vladimir Kozlov. The factory. 2023
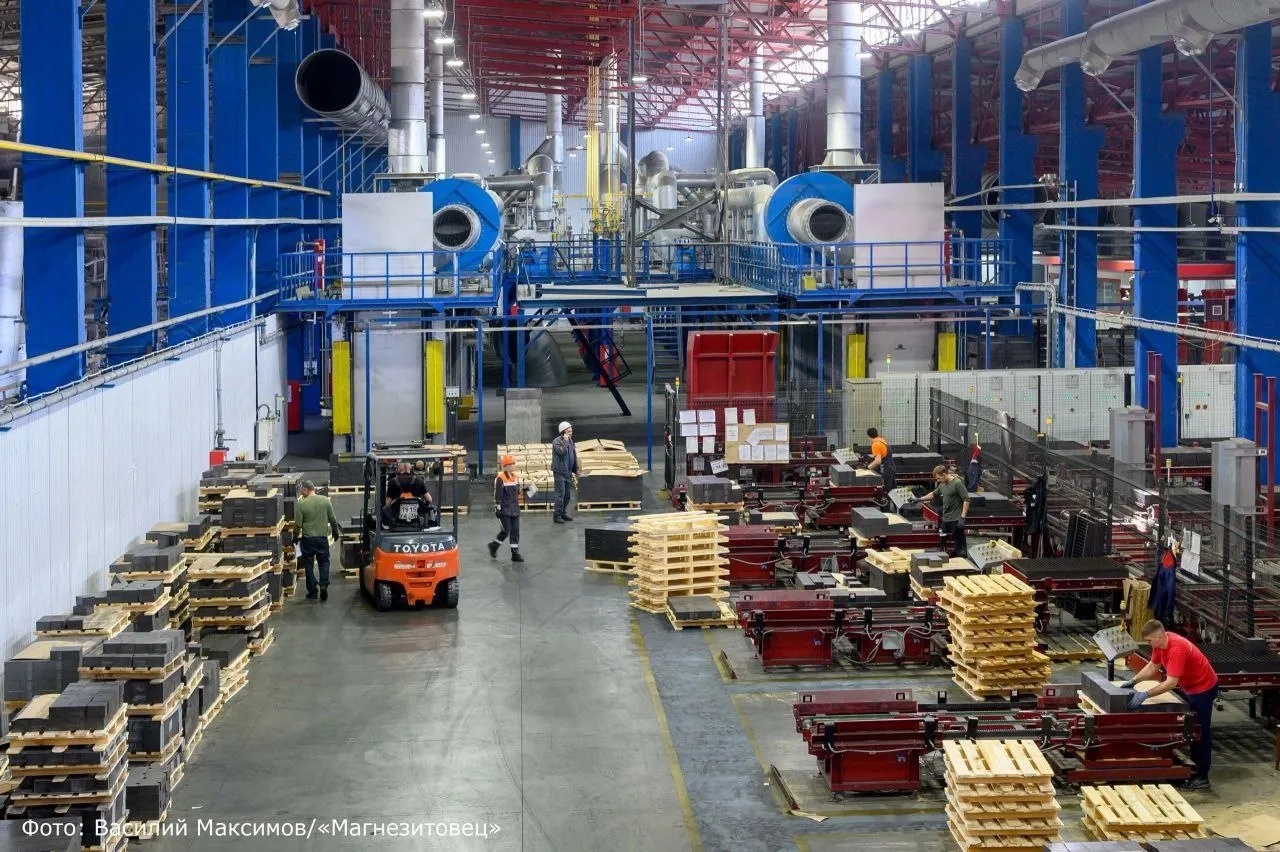
Original photo
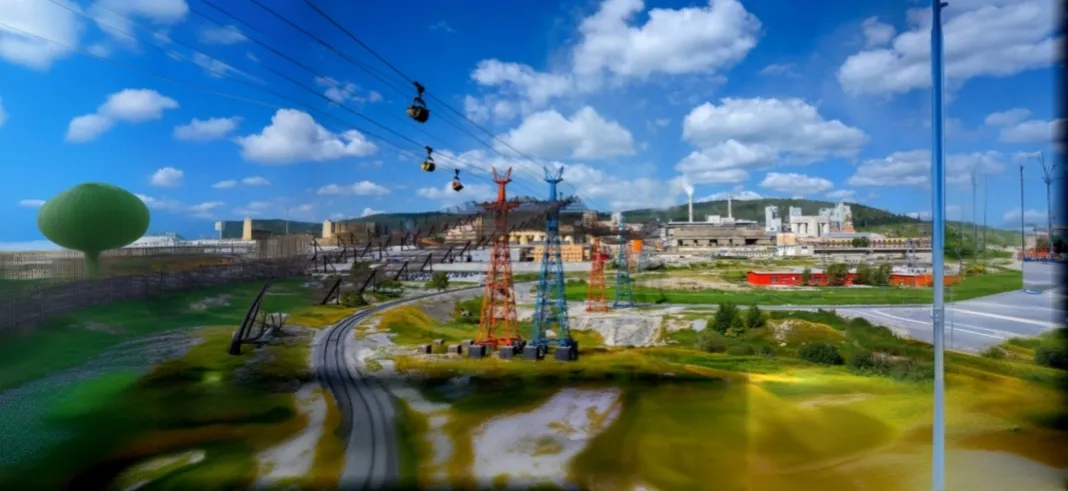
Veronika Lekontseva. Further — more. 2023
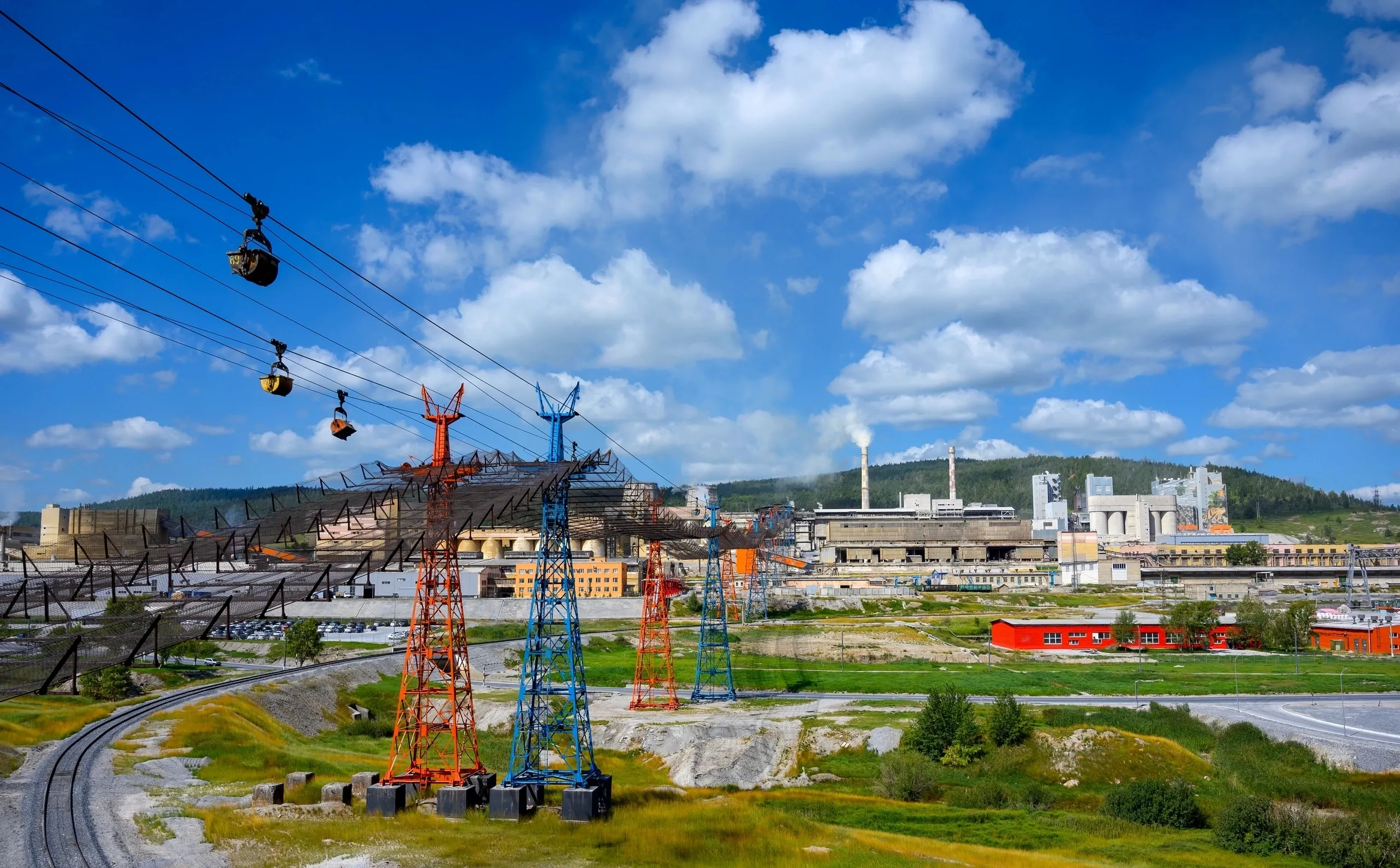
Original photo
Everyone can take part in the project. To do that, you’ll need to:
- Select a photo along the theme of “people x ideas x achievements.” The photo can be taken by you or selected from the Magnezit Group archives Magnezit Group archives
- Process the photo using any neural network capable of working with images.
- Send the original photo and the image generated by the neural network to museum@magnezit.com
- Include the title of the work and your first and last name in the letter.
You can see the works that have passed moderation here.
We wish you success in your creative endeavors!
exhibition
The project started as part of the same-name exhibition that opened at the Magnezit Museum on July 16, 2023. It was a notable event for residents and guests of Satka. The exhibition showcased the results of Magnezit Group’s modernization program as part of a broader history of people and ideas, and let us take a look at what generation and implementation of ideas may look like in the future.
-
The Art of Intelligence exhibition showcased the impact of modern technology on the art world. It demonstrated how art and technology can harmoniously coexist, inspiring new levels of creativity. One game invited participants to determine whether a certain phrase was authored by a human or a neural network, highlighting the striking similarity between artificial intelligence and human intelligence that we can witness today.
-
The combination of traditional exhibits, such as copyright certificates, patents, and trademarks, with the modern approach to showcasing production facilities and inventions through the lens of neural networks is truly impressive. It’s delightful to see how conventional exhibits can be seamlessly integrated with advanced technology. The museum team showed great creativity in designing the exhibition.
-
This exhibition is truly fascinating! I was particularly intrigued by the combination of AI-generated works and real photos. At first glance, they appear to be unusual paintings, but upon closer inspection, you realize that they are actually reproductions of the photos. It’s always interesting to witness the advancements in modern production lines as well.
-
We were amazed by the digital paintings created with the help of artificial intelligence. The neural network managed to recreate various art styles, exploring Impressionism, Cubism, and even reminding us of works by Van Gogh and Klimt. When leaving the exhibition, we felt that the future holds even more incredible opportunities through collaboration between humans and artificial intelligence. It was a truly unique and inspiring experience.
-
Thank you for the wonderful exhibition The Art of Intelligence. I’m grateful for the opportunity to remember the creative individuals who made invaluable contributions to the plant’s production process through their intellectual efforts.
Photo: Vasiliy Maksimov. 2023
more: "Magnezitovets"